- ベストアンサー
ドリル加工のスピードを上げるためには
- 良いドリルを見つけることが難しいですが、エアーブロー又は切削油を使用し、ワーク毎に使い分けることでスピードを上げることができます。
- ドリル径はΦ0.5~Φ13位まで使用し、リーマのした穴加工を行っています。ワーク材質はS50C、NAK80、NAK55、STAVAXなどさまざまです。
- オールマイティーなドリルを使用することが理想ですが、ワーク毎に使い分けることも考慮しています。アドバイスをお願いします。
- みんなの回答 (7)
- 専門家の回答
質問者が選んだベストアンサー
- ベストアンサー
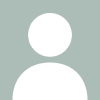
油性クーラントですね そうすると冷却性に不安が残りますので発熱のより少ない オイルホール粉末ハイスTiCNコートをおすすめします。
その他の回答 (6)
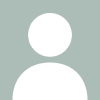
昔こんな風にやっていました φ3以下はG83 φ5~8まで 板厚30ぐらいまで G73板厚がそれ以上の場合G83 φ10以上は下穴あけてG83 φ3以下は曲がるし折れるし私は嫌い 今の会社はドリルチャックが二つしかないので アキュー用 センター用 あれ、ドリル用は??? 社長、ドリルチャック買ってください 愚痴ですが まじめに φ3以下はどうしてもG83を使い、工具交換しながらじゃないと、折れたり曲がったりしますが φ5以上なら30mmぐらいまではG79でやっていました どこかのHPで見ましたが 途中までG79の動きをして途中からG83になるマクロを見かけました そんなマクロも作ってみるといいかもしれません 主軸から油が出るようなタイプのマシンを使っているのなら ガンドリルなどもお勧めです(小径はありませんが) 不可穴は、基本的にキリコの排出と、ドリル先端の焼きつきが問題になってきますので 水溶性の切削油など使ってください
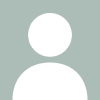
材質から、推理するとプラ型屋さんでしょうか? ドイツのグーリング社がお勧めです。。 http://www.guhring.co.jp/history/right.html 一味違いますよ。きっと。(経験者の意見です)
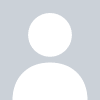
お礼
大変遅くなりましたが、ご回答有難うございました。
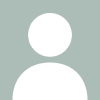
その場合は深さに注意が必要です ~5Dまでなら外掛けでも可能かと思います
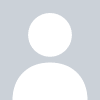
お礼
なるほど、試しに次回使ってみようと思います。 色々有難う御座いました。
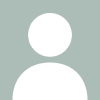
超硬ドリルでしょう! G83でステップかければ、あいた穴に、クーラントが残りますから、 5D以上いけます!工夫してやってみては?
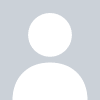
お礼
ご回答有難う御座いました。
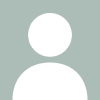
> ドリルの詳細は、NACHI HSS としかわかりません。 切削条件が不明ですが・・・・ 第一推奨:オイルホール超硬TiALNコート チッピングが出るようならオイルホール粉末ハイスTiCNコート 代表メーカ OSG クーラントは水溶性で量、圧力ともに十分上げてお使いください。
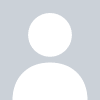
お礼
ご回答ありがとうございます。 なるほど、メーカーHPにて詳細を調査してみようと思います。 ちなみに、切削条件なのですが、ワーク、ドリル径によって変えておりますので、いつも条件が一緒というわけではないのです、すいません。 クーラントは残念ながら水溶性は使っていないのです。
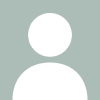
みなさんの聞く前に自分が使っているのを書かないと 「良いドリルを」の目的から外れる可能性がありますよ?
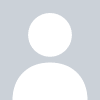
補足
そうですね、失礼しました。 ドリルの詳細は、NACHI HSS としかわかりません。
お礼
大変助かります! やはり、切削スピードを上げるには、熱と切りくず排出が大切ということですね。 更に質問なのですが、クーラントは外からではだめでしょうか? 今扱っている機械では、エアーは出せても、オイルは出ないタイプなのです。 切りくず排出という面で劣るとは思うのですが。。。 大変助かります! やはり、切削スピードを上げるには、熱と切りくず排出が大切ということですね。 更に質問なのですが、クーラントは外からではだめでしょうか? 今扱っている機械では、エアーは出せても、オイルは出ないタイプなのです。 切りくず排出という面で劣るとは思うのですが。。。