- 締切済み
ボーリングバーボーイングバイトについての質問
- ボーリングバーおよびボーイングバイトについて知りたい
- φ8からφ16のH7穴加工を効率的に行う方法はあるか
- φ8~φ18の径に合わせられるボーリングバーを探しており、専用アタッチメントに関しても知りたい
- みんなの回答 (4)
- 専門家の回答
みんなの回答
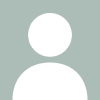
ボーリングバーでも良いですが、リーマで先端ヘッド交換式のリーマ830というものがサンドビックよりでています。 ヘッド交換は、スクリューを1/4回すことで簡単に脱着可能です。また、高送りで高精度な加工が可能です。 ヘッド寸法も10.0~31.75までありますので、工具としては1本でOKと思います。 また、ボーリングが良いということであれば、ファインボーリングヘッドというものがありますので、そのヘッドにボーリングバーを挿入して使用すれば径の調整も可能です。但し、リーマとボーリングバーを比較すると加工の面で一長一短ありますので、その辺りは考慮なさった方が良いと思います。 下記サンドビックWEBサイトですが、24時間フリーダイアルを受け付けておりますのでお気軽に問い合わせてみてはどうでしょうか。 私自身の経験上、ボーリングヘッドの目盛り調整に結構手間取ることも考えられます。
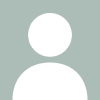
BIG-KAISER にあったと思いますが。 ボーリングバイトのシャンクφ16が付けれるように、ボーリングヘッドは大きいのを買います。ボーリングバイトのシャンクがφ10などを付けるときはφ16-φ10のコレットを使えばいいかと。 小径の穴用にはチップでなくてソリッドのボーリングバイトがあったような。
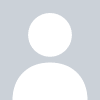
お礼
貴重な情報有難うございます。コレット使えば小径シャンクの工具も使えるので、大き目のボーリングヘッドを買ったほうがよいということですね。参考にします。
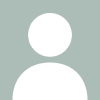
機械・材質・深さも不明だが・・・ 私も「アキオ」さんの意見に賛成です。 径が変る度に一々調整するのは現実的では無い。 1つの穴のセットだけでも容易では無いですよ。 深さにもよりますが、MCならエンドミルで真円切削で対応する方が良いのでは? 下穴のドリルはφ10以上なら ダイジェットのSカットが0.25飛びでありますよ。 仕上げなど場合、最終の仕上代が精度管理のポイントです。 それでもやってみたいならば BIG-KAISER をお勧めしますが。
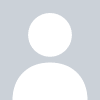
お礼
有難うございます。 <最終の仕上代が精度管理のポイントです。> <ダイジェットのSカットが0.25飛びであ>る。 早速探してみます。0.25ですと片肉0.125なので相当安全になります。これに銜え、小さい径のエンドミルたくさん用意してすべてヘリカルプログラムで加工するのも考えて見ます。
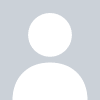
補足
失礼しました。 <訂> 銜え→加え
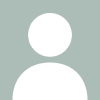
調整式の穴ぐりホルダーに大枚はたいて 調整に時間を食われるよりは、 リーマのホルダを余計に用意しておいて、 加工中にセットアップ、段取り替え時にそのまま入れ替えた方が よほど効率的だと思いますが... とりあえず、φ1?22という穴ぐりツールが ビッグ(大昭和精機)の取り扱い商品であるみたいですね. ただ、私は基本、旋盤屋だからよく判りますが、 内径をバイトで旋削してH7公差に入れるのは、 言うほど簡単ではないですよ. バイトは逃げるし、刃先は磨耗するし. 切れ味だけでコロっと数字が変わる世界です. 数値制御で数μm単位で調整してもヒヤヒヤするのに、 手回しのねじで一体どこまで対応できるでしょうね. 調整方式によっては、固定ねじの締め加減一つで、 5μmくらいは数字が変わってしまうハズ. 内径は測定誤差が3?4μmはあるので、 実質的なストライクゾーンというのはかなり狭いんですよね. H7は、φ16でも公差幅18μmでしょう? 最近はH7公差が一発で出るという触れ込みのドリルも 出回っている様ですし、ボーリング以外の道を探るのも 悪くないと思いますよ. 文字化けを起こしていました. ・φ1?22 → φ1~22 ・測定誤差が3?4μm → 測定誤差が3~4μm
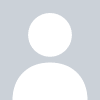
お礼
旋盤加工でもH7公差の加工は難しいんですね。やはり、リーマーのほうが無難かもしれないです。貴重な経験を教えていただき有難うございます。 <内径は測定誤差が3~4μmはあるので、> 旋盤でやってもない誤差は出てしまうんですね。エンドミルでコンタリング加工してもやはり、同じくらい誤差が出てしまいます。ヘリカルのプログラムを組んでらせん状にコンタリングしたとしても、やはり2μmくらいの誤差は出てしまいます。 とても参考になります。有難うございます。
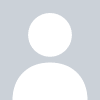
補足
失礼しました <訂> ない→これくらいの
お礼
有難うございます。