- 締切済み
マシニングでボーリングバーにて40h7深さ35mmの加工を行う方法と条件
- マシニングにおけるボーリングバーの使い方や条件について解説します。40h7深さ35mmの加工を行う方法や加工順序、固定サイクルについても説明します。
- マシニングでボーリングバーを使用して40h7深さ35mmの加工を行う際の条件や注意点をまとめました。材料にはS50Cを使用し、G86Z-40.0R5.F?のボーリングの固定サイクルをおすすめします。
- ボーリングバーを使用してマシニングで40h7深さ35mmの加工を行う方法と条件について詳しく説明します。主軸はBT30を使用し、下穴からの加工を行います。アドバイスや注意点もまとめました。
- みんなの回答 (4)
- 専門家の回答
みんなの回答
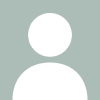
回答(1)再出です φ40H7 は 0~+25 ですかね エンドミルの振れ 機械熱変位 円弧補間時のサーボ誤差 位置決め精度バラつき etc. ひと穴、ふた穴なら大丈夫かもしれませんがもし量産加工なら... エンドミルは振れ精度の良い焼嵌めツールを使った方が良いかも まあ机上の推論より実機で確認した方が手っ取り早いでしょう
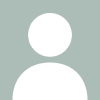
ボーリングバーを使った加工について異論を申し上げる意図はありませんが、 ご所望のφ40h7深さ35は、エンドミルを使って円弧加工すれば製作可能の ように思います。 もし宜しければ、ボーリングバーを使った加工を選択なさった理由をご教示 頂けないでしょうか。
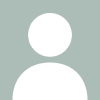
貫通穴ですかね? 精度穴ならG86よりG76(ファインボーリング)の方が無難かと思いますが。
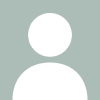
当サイトにおいて過去ログを検索すると参考になるQ&Aがみつかる 場合があります。下記参考に一例を示します。 G86はご存じの通り、穴底で停止→早送りで引き上げ→再度正回転、と 動作します。 ボーリングホルダへ取り付けるインサート(チップ)の材種はサーメット もしくはサーメットにコーティングを施したタイプが良いでしょう。 切削速度150m/min(1200min-1)、送り0.1mm/rev(120mm/min) 程度でまずはお試しください。 下穴は、ボーリングでの仕上げ代を0.1mm(径で0.2mm)としてφ39.8、 BT30主軸の能力を勘案すると、例えば ・φ16刃先交換式ドリル→φ12ソリッドエンドミルでφ39.8へ繰り広げ ・φ20刃先交換式エンドミルでφ36穴をヘリカルコンタリング加工 →φ12エンドミルでφ39.8まで繰り広げ のような方法が考えられます。 切削加工方法は「正解」があってないようなものなので、あくまでも ご参考となれば幸いです。