- 締切済み
SECC t=1.2 プロジェクション溶接
SECC-C20/20 t=1.2を2点プロジェクション溶接していますが、ナゲットがばらつき安定した生産ができません。溶接条件を変えてTRYを試してみたのですが条件が厳しく、電極のもちが悪いです。その条件もたまにつかなくなってしまったりして困っています。 プロジェクションの形状が悪いのでしょうか? 以下、諸条件です。 プロジェクション形状 高さ:0.9? 球R2.2 深さ:0.7? 球R3.2 溶接条件 溶接電流:20000A 通電時間:20サイクル 加圧力 :2.0kgf/cm2 初期加圧:60サイクル 私は金型担当なので溶接は詳しくないので、質問の要領を得てないかもしれませんがよろしくお願いします。
- みんなの回答 (3)
- 専門家の回答
みんなの回答
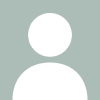
二点プロジェクションでしたら、素材に3点の突起を前加工で出しておいて電極はフラットな状態で押付け通電するという方法もあります。チリや凹みが発生しないように反対の面はセラミック板で受ける、という方式です。二点間で通電、溶接する方式です。 参考まで。
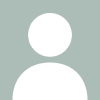
電極の凹みが問題であれば、高温硬さがあるタングステン系電極が有効かもしれません。亜鉛めっき鋼板ではありませんが、SPCC鋼板のプロジェクション溶接において、電極の凹み対策として実績があります。下記URLを参照していただき、ご検討いただければ幸いです。
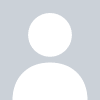
お礼
確かに電極はすぐにへこんでしまうので、試してみる価値はありそうですね。 今は溶接治具の見直しを行いゲージ(鉄)による分流を調べています。上下のワークの端がそろっているところに、両方の位置を同時に決めるゲージが入ってるのでそこで分流が悪さをしているかもしれないので。ゲージを電気の通らない材質に変更してみるつもりです。
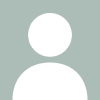
電極が新品時や再研磨後は安定しているならば、プロジェクションの形状がわるいのではなく、電極の亜鉛との反応を抑える工夫がいるかもしれません。 亜鉛めっき鋼板なので、クロム銅電極をお使いならば、亜鉛と銅が反応し、電極表面が汚れて、所定の形状(先端R)や抵抗値が変化し、ナゲットの不安定になっていると思います。溶接条件によれば、アルミナ分散強化銅に変えると寿命が延びた事例もあるようです。自動車メーカーなど、亜鉛めっき鋼板を溶接しているところは、溶接回数を決めてドレッシング(電極再研磨)を行いながら品質を安定させているようです。 ちなみに溶接回数と不安定発生、電極寿命はどういう関係でしょうか。
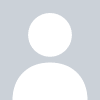
お礼
ご回答ありがとうございました。 電極の再研磨は通常、弊社では3000shotで行ってますが、今回質問した内容のものは300shotほどで電極のへこみ、亜鉛の溶着が発生してしまうときがあります。弊社での他製品の条件に比べるとずいぶん厳しい溶接条件に設定してあるので電極の消耗が激しいと思われます。ご指摘のとおり現在の電極材質はクロム銅ですが、今までも亜鉛メッキ鋼板の溶接は実績があるのでちょっとわかりません。
お礼
アドバイスありがとうございます。 ただ、3点の突起を作る為にワークの金型を改造しなければならないので(順送金型)大掛かりな工事になってしまいそうです。溶接設備のほうにも手を加えなければならないので、弊社の現状では厳しいかもしれません。