- ベストアンサー
材料の加工方法
金属部品(金属だけではないかと思いますが)、『ゼロカット加工』って言葉を聞きましたが、何のことなのかわかりません。ご存知の方教えてください。お願いいたします。
- みんなの回答 (2)
- 専門家の回答
質問者が選んだベストアンサー
- ベストアンサー
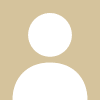
noname#58790
回答No.2
マシニングや研磨機、ワイヤーカットその他で もう一度同じ寸法で行う加工などです。 通常、 5.09の目盛りで加工を行えば、 理論的には同じ寸法で加工すれば削れるはずはありません。 所が、実際には長いエンドミルを押すので斜めに逃げています。 もう一度送ると正しい寸法で仕上がると言う事です。 但し、精密な機械の場合です。 セカンドカット、仕上げ加工とも言います。
その他の回答 (1)
- sanori
- ベストアンサー率48% (5664/11798)
回答No.1
「ゼロカット」は、登録商標、 商品としては意匠登録されているようです。 http://www.zerocut-watanabe.co.jp/contents/f-tech00.html http://gakusei.enjapan.com/2008/company_view/5148 特許電子図書館でも調べましたが、上記以上の情報は見つかりませんでした。