- ベストアンサー
※ ChatGPTを利用し、要約された質問です(原文:生材の研磨加工は なぜ 難しいの?)
生材の研磨加工の難しさとメカニズム
このQ&Aのポイント
- 生材の研磨加工はなぜ難しいのか?
- どうして生材の研磨がやりにくいのか、そのメカニズムを解説します。
- 熱処理が入ったワークを主に加工している弊社にとって、生材の研磨は未経験の作業であり課題となっています。
- みんなの回答 (2)
- 専門家の回答
質問者が選んだベストアンサー
- ベストアンサー
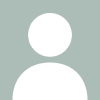
noname#230359
回答No.1
生材にマッチした砥石があまり出まわっていない ため、焼入れ材用の砥石で研磨すると目詰まりを 起こしやすく、その目詰まりした研磨カスでワーク をキズつけてしまう。(ドレス頻度増大) 結果、あらさ規格を満足するのが困難となります。
その他の回答 (1)
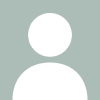
noname#230359
回答No.2
従来の金属加工油・研削油と言えば,洗浄効果から(組成上から)ソリューブルタイプと決め付けて、鋳物ならケミカルタイプ、最近ではシンセティックでとの固定的な考え方が浸透していて、潤滑性からエマルジョンは良いが砥石の目詰まりから駄目と決め付けていたようです。油の粒径が細かい為に潤滑性/浸透性が良く、かつ、目詰まりが無い製品がスイスから世界に販売されている製品が有ります。静岡県浜松市のセンターレス機器メーカーでは長期間の評価テスト結果を踏まえて推奨しておるようです。
- 参考URL:
- http://www.yukawacut.jp
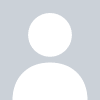
質問者
お礼
回答いただきありがとうございました。 適正なといし・油を選定しやれば加工可能とのことですよね。 適切なアドバイスありがとうございました。
お礼
回答してくださりありがとうございました。目詰まりが原因なんですね。スクラッチの問題もでてきそうですね。 初心者の私にもよくわかりました。