- 締切済み
サーメットリーマ不具合に対する対策
- サーメットリーマの加工条件と品質について問題が発生しています。
- 穴径寸法が不安定で、使用後の磨耗も早いため、不具合の原因を解明する必要があります。
- 切削条件や面粗度の要件を満たせれば、他の加工法や工具を検討する余地もあります。
- みんなの回答 (5)
- 専門家の回答
みんなの回答
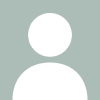
サーメットリーマ自体を見たことがないので全く自信がないのですが、先の方が提案されたようにコーティングを施すというのはダメなのでしょうか? 先日、日立ツールの営業の方が弊社にこられ、突き加工用の工具の新商品のPRをして帰りました。 まだHPには記載されていないようですが、その工具は底面仕上げも可能なスローアウェイ工具で、インサートの材種にサーメットのものがありました。 しかも、そのサーメットにTHコーティング相当をしてあるようです。 コーティングをしてあるため、サーメットと全く同じ面粗度とはいかないようですが、超硬インサートより良好な仕上り面になるとのことです。 工具タイプが全く異なるので参考になるかわかりませんが、とりあえず情報としてお伝えしておきます。
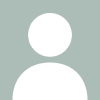
穴径分かりませんが・・・ 穴径寿命対策 ・リーマは特注ならプラス一杯に造ってもらう。 例 穴径0+0.02なら+0.014+0.017 (JISのm5だと+0.008+0.017) ・切削速度を1割位下げる この手のリーマで50は速いと思います。1割下げれば寿命は2割り のびるといわれます。 ・コーティングする。 下穴 超硬ドリル使用していますが、切れ刃とかマージン部の管理はなされて いますか。切れ味が悪かったり、先端部マージンが摩耗すると正テーパに なり、いっそう加工表面が加工硬化で固くなります。正常な場合でも加工 硬化はハイスの倍位ありますから、リーマ代を0.3或いは0.4程度に してみてはいかがでしょうか。ただしリーマの溝がせまいと切粉が悪戯す る場合、また食いつき部の角度等がそろっていないと穴径が大きくなりま すので注意してください。 下穴精度を調べたようですが、寸法精度より加工面の状態のほうが分かり やすいと思います。切削面ならいいのですが、バニシングされたような綺 麗な肌なら加工硬化(固くなっている)がおきていると思います。 こんばんは >それと 回答の本文中にサーメットリーマの切削速度は50m/minでは速すぎるとご指摘受けましたが、製作メーカーでは 100m/minでも問題ないはずであると言っていました。この不具合の解決にあたり メーカーとして考える最適切削条件の提示をお願いしていますが 今のところ回答がありません。 種類がちがうかもしれませんが、ここ(http://www.fptools.com/image/products/cs.pdf)では40メートル前後になっています。 リーマは穴を高精度に加工する工具ですから、摩耗がしにくいように条件設定したほうがいいと思います。 ※ハイスリーマは10mくらいで超硬リーマは15から20m程度だと思います。勿論速くも出来ますが、寿命が縮まります。 >切削送りとして今の条件を下回ることは ラインの設計上厳しいところがありますが、どの程度の切削条件が妥当か?聞かせていただけませんか? その辺は考慮して切削速度だけ書いたつもりです。送りは現状の1回転送りをそのまま毎分にして行えば(1刃当たりの送りが速くなりますが)加工時間は変わりません。 ※サーメットのリーマ使ったことありませんが超硬に比べて仕上げ面が綺麗になると思います、しかし摩耗しやすいし欠けやすいとも思います。 出来たら安定性のある超硬リーマを寸法指定で造られたほうがよいかと。 こんばんは リーマって http://www.asahikougu.co.jp/asahi-hp/gijyutu/jyouken-rm/ の一番上にあるようなタイプですよね。 >現在φ21リーマで回転数750rpm、送り350mm/minとしています。(0.47mm/rev)無理な切削条件でしょうか? むりじゃないけど一般的には速いと思います。 >3.2s以下の面粗度と 単位時間当たり送り300mm/minをクリアできるならば 超硬でも ハイスコーティングでもいいのですが・・・目標が高すぎたのでしょうか? 3.2Sをリーマで出すのは一般的に難しいと思います。刃具メーカさ んがサーメッを候補に上げるもの分かる気がします。 >刃付けの研磨時のバックテーパーがきちんとストレートになっているかをチェックして製造したのでもう一度試して欲しいということでした。 バックテーパは回転トルク軽減のためにも必要だと思いますが、ストレ ートのリーマってどうなんでしょう。 http://www.natuo.com/sirilyousituhure-mu2kakou32kougunobakkute-pa.htm 棒状工具のバックテーパ参考資料 >加工径が10本で10ミクロンもマイナスしても リグラインドすると最初は又 元の径に戻るといのは どういうメカニズムなのでしょうか? 切れ刃が鋭利過ぎると微妙に振動(ビビリ)し、穴が拡大傾向になります。 通常はこれを防ぐためにハンドラッパなどで切れ刃をこすり目潰し(ホー ニング)を行います。加工数が増えると穴径が縮小するのは、刃先が摩耗し てビビリが押さえられたためと考えられます。 >リーマの切れ味が悪くなってワークに熱を与え膨張させたまま加工して それが冷えると小さくなると無理な説明をされましたが、納得がいきません。 通常もありえることですが、これが今回の穴縮小原因なのかどうかはわ かりません。一度加工直後の製品温度を測られたらいかがでしょうか。 ところで 穴の許容差はいくつでしょうか? それからリーマの製作寸法と公差を教えていただければ何かいい案が浮か ぶかもしれません。
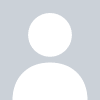
お礼
回答ありがとうございます。下穴ドリルの加工硬化という観点にはきづきませんでした。早速調べてみます。 それと 回答の本文中にサーメットリーマの切削速度は50m/minでは速すぎるとご指摘受けましたが、製作メーカーでは 100m/minでも問題ないはずであると言っていました。この不具合の解決にあたり メーカーとして考える最適切削条件の提示をお願いしていますが 今のところ回答がありません。 切削送りとして今の条件を下回ることは ラインの設計上厳しいところがありますが、どの程度の切削条件が妥当か?聞かせていただけませんか? 本日、製作メーカーと打ち合わせをもちました。結論的に明確な打開策が見つかりません。同じ製造ロットの中に比較的いいものとまったくダメなものがあるという観点から、いいものは造れるはずであると諦めがつきません。切削条件として 単位時間当たりの送り量を 300mm/min以上を狙っています。現在φ21リーマで回転数750rpm、送り350mm/minとしています。(0.47mm/rev)無理な切削条件でしょうか?尚、サーメットに固執しているわけではありません。3.2s以下の面粗度と 単位時間当たり送り300mm/minをクリアできるならば 超硬でも ハイスコーティングでもいいのですが・・・目標が高すぎたのでしょうか? ちなみに本日のメーカーの話を総合すると 刃付けの研磨時のバックテーパーがきちんとストレートになっているかをチェックして製造したのでもう一度試して欲しいということでした。それにしても 加工径が10本で10ミクロンもマイナスしても リグラインドすると最初は又 元の径に戻るといのは どういうメカニズムなのでしょうか?リーマの切れ味が悪くなってワークに熱を与え膨張させたまま加工して それが冷えると小さくなると無理な説明をされましたが、納得がいきません。サーメットチップを母材(SCM)にロウ付けしていますが この部位が悪さしているということなのか?何から何までが理屈で解決できず 困り果てています。 何かアドバイスいただけることは ありませんか?宜しくお願いします。
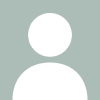
パッと思いつくのが(やりやすそうな順に) 1.取り代 少なく 2.クーラント 濃度を濃くする 銘柄を変更 より重切削重視の物に変更 タップ、ガンドリル可能をうたった物 水溶性を油性に変更 3.工具 初期摩耗が多いことから 刃先のチャンファー、Rなど いわゆる「ころし」 の形状を数値化し最初から処置しておく=>寿命の安定化 超硬リーマのトライの場合
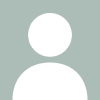
サーメット、寸法マイナス、寿命ばらつく、から想像するに、直近の No.23189 にあるような刃先ホーニングの問題ではないでしょうか? なるべく倍率の高い顕微鏡で刃を観察すると解決策が見えるように思います。
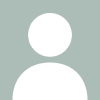
自分が思いついた範囲でですが下穴の径をもう少し拡大してみては如何でしょうか? 現在【-0.2】の径の下穴用超硬ドリルを使用しているのなら、 【-0.1】や【-0.05】の下穴ドリルに変更する事で、リーマへの負担も減るのではないでしょうか? それとリーマも超硬にする事は出来ないのでしょうか? 超硬リーマも各社様々な形状で販売されていますので検討しても良いかもしれませんよ。 それと工具の振れ精度を改善する事で、もしかしたら面白い結果になるかもしれませんね。
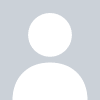
お礼
回答ありがとうございました。下穴径の拡大は考えないこともないのですが、在庫も含めて 特殊な工具をもう一度準備しなければならないという現実的な問題もあります。径小から径大には変更できませんが、径大から径小には修正可能だと思いますので 一度これでドリルを製作してみたいと思います。 又、超硬の採用についてですが、過去の経緯から切磋時間の短縮と加工面の面粗度の向上をMUSTとするところから工具メーカーと仕様打ち合わせをした結果、サーメットでないと面粗度的に規格(3.2s)をクリアできないと言われ、サーメットを採用することを決定しました。サーメットを採用した理由はここにあり、超硬でもOKということであれば問題はありません。何かいいスペックのものがあれば紹介してください。よろしくお願いします。
お礼
回答ありがとうございます。