- 締切済み
ワイヤー仕上加工における取り残しについて
- 大同特殊鋼のDC53材(焼き入れ品:t=20mm)のワイヤーカットを行なっていると、加工が終わってみると取り残しが突起として残ってしまうことがあるのでしょうか?
- プリハードン鋼での加工ではそのような事は確認されてないのですが、材料の違いによって起こり得るものなのでしょうか?
- ワイヤー仕上加工において、取り残しの発生に影響する材料物性のパラメータについて教えていただけますか?
- みんなの回答 (2)
- 専門家の回答
みんなの回答
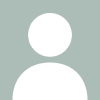
材質が硬い物や、途中にネジ穴が複数あいている場合などに 取り残しのような跡がのこる場合があります。 ↑↑のような跡でしたらオフセットの変更や加工条件の変更で 直ります。 例えば、ファーストカットのオフセットを小さくしたりとか・・・ メーカー指定のオフセット・加工条件が材質と合わない場合、削れなくて? 2set目以降に負荷がかかり上記のような跡が残ります。 >ランダムに取り残し?>について見当違いをしていたらすみません。 サード以降はあくまでも仕上げで、精度を出すためのものであり、 その前の段階で、0.02残し前後まで追い込む必要があります。 (サード以降は電圧が低く加工条件のOFF状態が長い為です。) ちなみに、それぞれのカット時のスピードはどうでしょうか? セカンドカット以降遅くなったりしていませんか? 材料の種類・・・粗さはそんなに変わらないですね。 スジは出ることがありますので、過去の経験で予め条件を変えておきます。
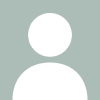
多分、外的影響を受けている可能性が高い 設置場所の基礎の状態は? 近くに振動源があるのでは? 機械本体ではなく、その他の原因が疑われる事は気づいておられますね。 だからこそ材質の問題を疑われたのだと想像します。 メーカーも一番最初にレベルの確認をすると思います。 事実2階に設置された機械で不規則な精度不良を経験しております。 別の事例ですがワイヤーの捻れが原因で精度不良を起こした例もあります。 ワイヤーのメーカーを変えることで改善できました。 色々と設定条件(ワイヤー・材質を含む)を変更して確認の必要があると思われます。 材質の異状による検証は顕微鏡での組織の確認で可能だと思います。
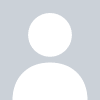
お礼
ご回答ありがとうございました。 基礎状態については、明日から調査してみます。 (具体的に調査すべきパラメータがありましたら、ご教示お願いいたします。) また機械周辺は振動が伝わらないように区切られているため、他の機械からの振動などが伝わるという可能性は低いと考えています(逆に伝わっているとしたら、かなりの数の取り残しが生じているものと思います)。 また、外的影響を受けている可能性が高いというのは、何か根拠がおありなのでしょうか?(何か具体的な事例があるのかなど。)
お礼
ご回答ありがとうございます。 一度、オフセット量や加工条件を変更して実験してみます。 ファーストやセカンドのオフセット量に関してはメーカーの方も言われておりました。 ただ、個人的に気になっているのは、なぜ局所的に発生するのかということでした。たとえば、取り残し部は数ミクロン程度と小さく、ファーストやセカンドの加工ではオフセット量が取り残し量よりも多いため、条件面で追い込むにしてもサード以降のオフセットや条件を調整するべきではないのかとも考えています。 はっきりとした傾向がつかめないため、根本的な原因(材料、機械、条件)が特定しにくい状況ではあるのですが、何とか究明したいと思います。実際の加工が全て狙い通りになっているのかも、気になっているところです。 ちなみに材料の種類が違った場合の仕上げ加工で、表面粗さやスジの残りなどに影響がでたりしたことはありますでしょうか?(鋼材でも、品種の違いによって差が生じるのかなど。)