- 締切済み
※ ChatGPTを利用し、要約された質問です(原文:穴ピッチの変更)
穴ピッチの変更で金型部品加工時間を短縮する方法はあるか
このQ&Aのポイント
- 初めて投稿します。
- 穴の大きさは変わらないのですが、間隔の変更が多くあります。その都度、金型の部品を加工しならなくなり、時間もかかります。
- 穴の大きさは、8mm20mm、間隔は100mmですが、間隔の変更は10mmの間で、0.2mmの間隔で変わります。精度はプラスマイナス0.05、です。
- みんなの回答 (1)
- 専門家の回答
みんなの回答
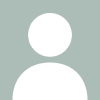
noname#230359
回答No.1
穴ピッチを変更する手として考えられるのは 偏芯ブッシュです。