- 締切済み
焼き入れ後のエンドミル加工のヒントを教えてください
- 焼き入れ後のエンドミル加工について、ワークの天面を研磨ではなくフラットエンドミルで綺麗に仕上げたいと考えています。現在は焼き前に加工し、焼き後にエンドミルで削って仕上げていますが、面が途中からきたなくなる問題があります。
- 加工条件は回転と送りをNAK80より50%落としています。中仕上げ加工についても同様の問題があり、刃がすぐになくなってしまいます。ピンカドの刃を使えばもっと刃がもつのでしょうか?ボールでの中仕上げも行っていますが、立壁などが絡むとフラットエンドミルで行いたいと考えています。
- 良いヒントやアドバイスがあれば教えてください。
- みんなの回答 (5)
- 専門家の回答
みんなの回答
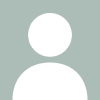
毎度。 三菱マテリアルから出ている「インパクトミラクル」エンドミルを試してみてはどうですか。 一応高硬度用とうたっていますので。 以上
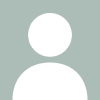
はじめまして。 参考になるかどうかわかりませんがCBNはどうでしょうか? 以前、R1のボールで、材質はSTAVAX(HRC53)を切削しました。 加工面は良好でした。工具寿命もかなりいいです。 フラットにあてはまるかどうかわかりませんが・・・ あと、OSGのラジアスエンドミルです。加工面はNAKとまでいきませんがHRC60でも直彫りが可能なので加工時間は短縮できると思います。
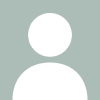
ミラカットはむくです。ちなみにうちでは25Φ以下はむくの通常エンドミルです。サーメットは各メーカーから出てます。ミラカットは確かosgだったと思います。高硬度材は刃物の材種を硬度の高いものにしてそれなりの速度で加工しないとかえってきれません。以前も書きましたが高速で刃先温度を上げて材料の軟化温度以上にして加工する為。
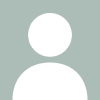
焼き入れ後の底面加工、いやな条件ですね。サーメットは試されましたかミラカットとかいおいろなメーカーからでてます。底刃専用を謳ったものもあります。あと新品のピン角をダイヤモンド砥石でちょっとC面をつけるように殺すともちがよくなります。
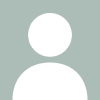
はじめまして。 あまり、高硬度ワークは加工しないのですが、刃もちの件については、最新の超硬EMとコーティングの物を選ばれたらいいと思います。 使用工具がφ10と指定されているみたいですが、もし、加工上φ12の刃物が使用可なら、超硬チップも検討されてはいかがでしょうか。ノーズRは0.5~0.8となりますが。 あと、切削油の濃度や種類によって圧倒的に差が出る時があるみたいです。 このような内容でヒントにならば、いいのですが・・・。
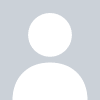
お礼
さっそくアドバイス有難うございます。 工具とコートは、それなりに新しいものを使ってるのですが、 なかなか・・・。 とくに底面仕上げなんかは、思うようにならなくて。 切削油は油性を使ってます。 有難う御座いました。
お礼
有難うございます。 どちらかと言うと、工具径が2や4が多いので、チップはほとんど 使った事がありません。 底刃専用というのは、やはりチップですか?。 ちなみにチップは最小何パイまであるのですか?。 チップだと、綺麗にいきますか?。