- ベストアンサー
※ ChatGPTを利用し、要約された質問です(原文:手磨きで得られる表面粗さについて)
手磨きで得られる表面粗さについて
このQ&Aのポイント
- 射出成形金型のキャビティ加工において手磨きを行う際、適切な番手の砥石を使用することで所定の面粗さを達成できます。
- 手磨きにはWA(白色アルミナ)のスティック砥石とピカールペースト剤を使用しています。
- 材質がエルマックスの場合、磨き作業の結果としてRz=0.5ミクロンの面粗さを目指すことができます。
- みんなの回答 (4)
- 専門家の回答
質問者が選んだベストアンサー
- ベストアンサー
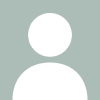
noname#230359
回答No.3
焼入れした硬さにはピカールは歯がたたないでしょう。 WAのスティック砥石で磨けるならそれでよいが、ダイヤモンドが鋭い。 スティック砥石 http://jp.misumi-ec.com/vona2/detail/110600283040/ フィルム状のもの。 http://jp.misumi-ec.com/vona2/detail/110600286970/ #1,000ぐらいまで 仕上げはダイヤモンドペースト。上記のものとおなじ#でも面粗さは細かくなる(固定砥粒と遊離砥粒の違い) http://www.tk-j.co.jp/service/tools/amplex.html Rz=0.5ミクロン は鏡面とはいえず。#1,800で到達出来ると思います。
その他の回答 (3)
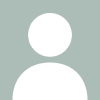
noname#230359
回答No.4
http://www.kanagatafan.jp/tech_info/20091101_000000.html 上記URLのような内容を参考になさっては如何でしょうか。
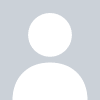
質問者
お礼
ありがとうございました。 磨きの方法について詳しく書かれていたので とても参考になりました。
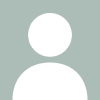
noname#230359
回答No.2
ムラを含む手作業で目安ありますかねー。Raではなく、Rzで0.5μですよね。
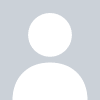
質問者
お礼
ありがとうございます。 実際に手作業で必要な分得られるか試してみたいと思います。
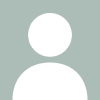
noname#230359
回答No.1
鏡面 面粗さ(Ra)で数~数十ナノメートル(ナノは10億分の1)
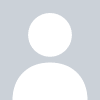
質問者
お礼
ありがとうございます。 おそらく鏡面まで必要なので目標値はもう少し高く設定したいと思います。
お礼
ありがとうございました。 今までの方法で充分に磨けていない可能性あるので、 工具材質の検討を充分に行ないたいと思います。 Rzはもう少し細かい値を目指すべきかもしれませんね。