- 締切済み
平面の加工粗さについて
平面加工に悩んでいます。研磨は出来ないポケットの平面加工です。 材質はS50Cです。 色々とカッターを試してはいるのですがどうしてもカッターとカッターのつなぎ目に膨らみがでます。新品のエンドミル0.003 二度目と三度目使用すると最大で0.02は膨らみがでます。チップ式カッターなどのものでもやはり同じ様な結果です。 仕上げ加工は一度で駄目になる物なのでしょうか? 皆様はどのように仕上げ加工はしていますか? すばらしいカッターがあるのなら紹介下さい。 ご返答ありがとうございます。パスも色々試してみました。大幅なピッチ細かいピッチでそれでも上手くいきません。 φ16で幅7ミリ間隔で加工。10ミリ間隔で加工同じ結果です。 サーメットでは減りが早くて平面が出ないと聞きます。幅広い加工だと問題にならないとか聞きます。もし良きサーメットをご存知ならお聞かせください。 縦横とは行っていません。平面加工となると縦横となるのが常識なのですか。 今一度ご返答お願いします。
- みんなの回答 (7)
- 専門家の回答
みんなの回答
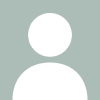
エンドミルの減りも早い場合は、油性切削油、サーチングカットFS-36がS-50C、S-45Cには刃持ちの向上に貢献できると思われます。 エアーカットを加えて加工頂けば、0.02よりは、かなり向上すると思われます。
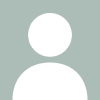
工具材質でサーメットにこだわる必要はありますか? 超硬、ハイスで試したらどうでしょうか。 S50Cの生材に高価なサーメットを使用する意図が分かりません。 色々な条件で加工して良い結果が得られないのであれば 工具メーカ、工作機械メーカに相談するのが早いと思います。 うちでは、超硬でエアーブローもしくはハイスで油性切削油で加工して 問題ありません。 あとは機械精度でX,Yの切り替え(象限切り替え)もしくは Z軸の上がり下がりが多いと段差はできます。 ただ今回はカッターのつなぎ目での問題なのでやはり工具、 切削条件を見直し、試す方法が良いと思います。
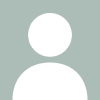
>サーメットでは減りが早くて平面が出ないと聞きます. >チップ式カッターなどのものでもやはり同じ様な結果です。 チップは値段の高いメーカーのを使うと長持ちしたことがあります。 回転数を少し落とすと2倍ぐらい長持ちしたことがあります 仕上げ代は最低でも0.1だと。 少なすぎるときれいにならないです OSGの超硬コーティングエンドミルの方が長持ちするかもしれません。 NACHIのX'sミル多刃がいいかも。 コーナーにRが付いていていいならWXスーパーラジアスエンドミルかと。 あまり自信ないけど。
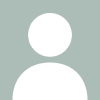
こんばんは 加工面の模様ですが「あやめ」になっていませんか?。 もしそうなら参考URLの4.参考資料にありますが、パスのさかいは段 差がつきます。刃先が切れなくなってくると削るから押される傾向になる ので境目が盛り上げるようになります。 段差(かえり等)を抑える場合は、パスをカッターノーズRを引い た直径にマイナス0.2前後で通すようにすればいいと思います。 >た直径にマイナス0.2前後で通すようにすればいいと思います。 1パス2パス目の交差幅を0.2位にすればよいと言う意味です。
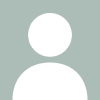
パスの幅(ピッチ)が大きすぎるのでは? 仕上げ1回目に縦方向に・2回目に横方向にパスを変えてもダメですか? S50Cはチップ式ならサーメットでなければ綺麗にはなりませんし、チップ自体に逃がしなどは当然あるので、その範囲内でのピッチでパスしていますか?
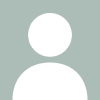
継ぎ目の段差が最小で3/1000最大で20/1000ということですね? #1さんに追加するなら 1.工具長は最小限にする 2.サーメット底仕上げ用のエンドミルにする。 3.回転数によっては主軸の熱膨張を最小にするために準備運動が必要。 4.ポケットの回る順序を巧くすると段差は少なくなる 5.工具の膨張を押さえるためにクーラントを使用する。 >1。工具長は最小であると思いますワークから5ミリの間隔です。 >2。サーメットでは減りが早くて300角くらいになると最終では一回の加工で0.01は減ると聞きます。 他の方もおっしゃってますがS50Cですとサーメットで十分対応出来るはずです。(諸条件がありますので言い切れませんが) 被削材との親和性も低いですし硬度も高い方なので減りが早い?と言うのが 分かりません。 超硬などより脆い材質なので振動がでれば摩耗が早まる可能性はあるかも・・・? 取り敢えずトライされてはどうですか?お勧めはOSGですね、型式はお調べください。 >4。ちょっと意味が分かりません・ パスの仕方でで段差が目立たないようにならないかと言うことです。 >5。色々と試しました。ミストやクーラント他の問題のよう気がします。 そうですか?うちでは結構効果あると思っていますが・・・ ハイスの場合はドバッと掛けてください。
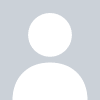
補足
ご返答ありがとうございます。 1。工具長は最小であると思いますワークから5ミリの間隔です。 2。サーメットでは減りが早くて300角くらいになると最終では一回の加工で0.01は減ると聞きます。 3。常に機械は動いている状態で暖機は出来てます。 4。ちょっと意味が分かりません・ 5。色々と試しました。ミストやクーラント他の問題のよう気がします。
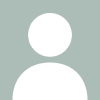
エンドミル0.003の意味がわからんが つなぎ目に段差が出来るばあい、 1.取り代がおおすぎる 2.パス間ピッチが広すぎる(取り残しってやつ)ふつう、径の70~80% 3。送りが早すぎる など、考えられます
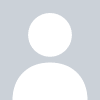
お礼
送りと回転には考えて見ました。 削り代には0.1から0.01まで試しました。 新品では回転を大きくすると新品では絶大な平面度がでました。 しかし2回目3回目となると全然だめです。 ピッチは色々と試しました。 ははは様は平面加工は完璧ですか?
お礼
ご返答ありがとうございます。 パスピッチには色々とためしています。 サーメットは広い幅になると減ると聞きます。ピカピカになるけどパスの終わりの頃はチップが減って結局平面が出ない。 縦方向と横方向でCAMでパスを出すとするとかなりの手間となるのですが。 私が思うにチップの先端が減ってこの様な現象が起こるのではないのではないかと、試した事はないのですが、縦と横とでパスを出したとしても、答えは変わらないのでは、縦加工でチップは消耗し減る。その後横加工に入る。たぶん横加工は削る事が出来ないと思う。S.N様は平面仕上げでは縦と横でパスを出していらっしゃるのですか? オススメのサーメットをご紹介願います。