- 締切済み
工具交換の回数を減らす方法
- ファナック制御のマシニングにおいて、工具交換の回数を減らす方法について考えます。
- 工具交換のために時間を浪費することは生産性を低下させます。そのため、工具を持ったままで終了する方法は効果的です。
- 特定の工具を持ったままで加工を終了し、次回も同じ工具で加工を行うことで、工具交換の回数を減らすことができます。
- みんなの回答 (6)
- 専門家の回答
みんなの回答
- hahaha8635
- ベストアンサー率22% (801/3611)
固定番地/メモリーランダム方式/ATC高速化 ツール交換はエアーカット時間に含まれ量産時ネックになります それを最小限に考えられたのがメモリーランダム方式です 加工後ツールは番号順に並びませんが シーク時間が短くなります メーカによってより ユーザーのオプションになります メモリーSW で 変更できるものもありますが できないものもあります メーカに聞くしかないです メモリーランダム方式も場合隣り合う工具の番号が都度変わるので ATC内での工具の干渉の危険性があります また段取り時のヒューマンエラーも発生する可能性が高くなります 量産でも固定番地方式を選ぶ場合もあります 貴社のプログラムで 加工後T0番と交換するのは メモリーランダム方式でもツール番号をきれいに並ばせるソート技術(裏技)です エアーカットが気になるのならすべてのT0と高速化できます 機械購入時(特に中古)に確認しましょう 最新のマシンではATCの速度自体を高速化したモデルもあります
- HikaruSai-2018
- ベストアンサー率46% (214/461)
小型はその考え方ですが マガジンナンバーとツールナンバーは変えないと言うのも有りますのでやはり機械メーカーの機種次第ですね 試して答え聞かしてください
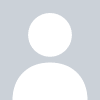
お礼
回答ありがとうございます 機械メーカー次第となると危険な気もしてきましたが 取りあえずは試してみたいと思います
- hahaha8635
- ベストアンサー率22% (801/3611)
固定番地 なのか メモリーランダム方式 なのかでちょっと挙動が違う と言っても加工上 は 何の影響もない 単に段取り時に番地がぐちゃぐちゃになってるだけ https://www.kousakukikaisekkei.com/tech/26/
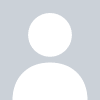
お礼
回答ありがとうございます >固定番地 なのか メモリーランダム方式なのか マシニングが数台あり混在しているようです 加工上で問題ないなら大丈夫だと思いますが マシニングスタッフの思い込みとかあるといけないので 一度、試してみたいと思います
- HikaruSai-2018
- ベストアンサー率46% (214/461)
機械メーカーの考え方で違うと思います 機械取説かメーカ確認も手ですね
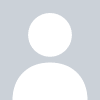
お礼
回答ありがとうございます 何気に気になっているのが 『T22を返してT23を取る』 T23の入っていたポットにT22を返すんですよね たぶん ポット番号とT番号の関係が崩れるけどトラブらないのかな? その辺りも気になるので実際に 一度 試してみたいと思います。
- morikousuke
- ベストアンサー率66% (41/62)
M6を消せば主軸に工具を保持したまま終了出来ますよ。 T00M6も主軸の工具をツールマガジンに返しているだけではなく選択しているT00の工具と交換してる動きです。 T00を主軸に保持して終了しているわけです。 T22を持ったままで加工が終了すれば 次回 T22M06を読んだときは交換無しで加工 違う工具 T23M06を読んだときはT22を返してT23を取る などの動きになるのでしょうか? ーーそうなります。
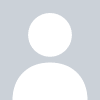
お礼
回答 返したのじゃなくてT00を掴んだと思えばいいんですね! ありがとうございました。 一度 試してみます。
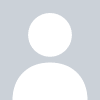
補足
回答ありがとうございます っと最初に書きたかったのですが すみません お礼が消えていました
- HikaruSai-2018
- ベストアンサー率46% (214/461)
ファナックじゃなく機械メーカーの話では無いですか?
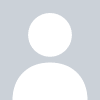
お礼
回答ありがとうございます あれ? そうなんですか! マシニングは、、色んなメーカーの色んな種類が混在しています。 やってみなきゃ分からないと言う事になるのでしょうか。
お礼
回答ありがとうございます >固定番地/メモリーランダム方式 この両方のマシニングが混在しています >メモリーSW で 変更できるものもありますが できないものもあります できないタイプでした。 >ATC内での工具の干渉の危険性があります ヒューマンエラーはともかく工具の干渉の可能性があるのでしょうか? それぐらいはうまい事やってくれると信じていました。 >加工後T0番と交換するのは >メモリーランダム方式でもツール番号をきれいに並ばせるソート技術(裏技)です T0番と交換すれば元の位置に返すと言う事でしょうか? ご存じでしたら教えてください。