- 締切済み
アルミダイカストのシール部腐食対策について
- Alダイカスト(ADC12)の筐体を使用した防水構造を検討中ですが、塩水噴霧試験において腐食によるシール破壊が問題となります。
- シール性(耐塩害性)の改善方法や、腐食進行のメカニズムについての情報を求めています。
- 接着とO-ringのどちらが塩害に対して有利か、そしてレベルアップのためにどのような方法があるか知りたいです。
- みんなの回答 (6)
- 専門家の回答
みんなの回答
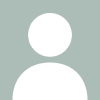
3ミクロンで効果が出ますが企画に外れますか?
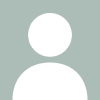
oリングの材質の選択、シリコーン系ゴムとともに、ADC12に比較して腐食はないはずでアルミの腐食によるシール漏れかと思いますが間違っていますか?アルミとシール材の界面に限って改善するにはフッ素系処理法タフラムなどいかがでしょうか?寸法変異数ミクロンはあります。コストは高くなりますが! 見当違いでしたらごめんなさい。
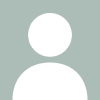
まずOリングは当然、断面は○型のものを使用する事ですが、あとは、アルミシール部(O-リングが組み付けられる溝部)表面粗さの精度を上げる事です。もし、いつも同じ場所から腐食が確認される様であれば、シール面全体の平面度も見直してみる必要があるかも知れませんね。 あと一つ重要なのは、O-リングが圧縮されて歪んでいる状態での実効シール面積ですね。要は、アルミ側の適切な溝の加工寸法とそれに合ったOリング断面外形を選択する事です。 無論、信頼できるOリングメーカーの、そこが推奨するものを使うのが前提ですが。
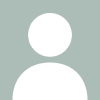
溶射は如何ですか。
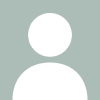
padiさんのご意見の通りです。アロジン処理が一般的でしょう。ダイキャスト品の加工品をそのまま塩水噴霧はちと無理かと。内部品質の良いダイキャストを素材のまま使うと多少良いのですが、それでも塩水は条件によっては難しいと思います。以前水溶性のアクリル系コーティングをしている部品がありましたがどのような条件を想定していたかはわかりません。
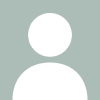
ダイキャストの要求精度にもよりますが、 アルマイトが施せないなら、化学皮膜処理(アロジン#1200)を施すことで塩水噴霧による耐腐食性は著しく向上します。膜厚は1ミクロン程度です。衝撃によるキズや摩擦には弱いですが・・・参考までに。
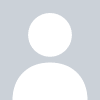
補足
早速の回答ありがとうございます。 アロジンも検討いたしましたが、今ひとつ効果がないことと、加工部分の面粗度5-10Zが確実に確保出来ないことから断念しました。。。 他にもアイデアがありましたら、またお願いします。
お礼
回答ありがとうございます。 ダイカストADC12での耐塩害性が低いということですね。他部分への弊害が数多い為、極力D/Cへの変更は入れたくないのですが。。。 シール材料の変更、あるいは構造の小変更(例えばO-ring重点率を上げるなど)で改善するアイデアはないでしょうか?