- 締切済み
小径エンドミルでの深溝加工の課題
- SS400に幅6mm、深さ25mm、長さ18mmの溝加工を行っていますが、エンドミルが折れたり加工面がガタガタになる課題があります。
- 幅の交差は0~+0.1mmで、回転は600rpm、送りは手送りでジワジワ送っています。
- ベテランの方からのご指導をお願いします。
- みんなの回答 (6)
- 専門家の回答
みんなの回答
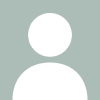
幅6mm 深さ25mmということは すでにエンドミル加工の領域ではないような気がするのですが 溝なのでワイヤーで切ってもらうか、 放電で突っついてもらった方が絶対に早いです、 フライスでやるとしたら 4から5mm位のドリルで穴をグズグズにします それから、5mmの再研検済みのエンドミルで溝をつなげます 横面をならします それから中仕上げでエンドミルを交換し4mmのエンドミルで側面肩肉を0.5位まで仕上げます それから、5mmのエンドミルで公差ないまで仕上げます ワイヤーなら、1時間ぐらい?←目をつむっていてもできる公差 フライスでは・・・ORZ
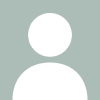
こんにちは。 まず、超硬の4枚刃を使う。 周速は50メーターとして、3000回転。 刃長は、26ミリ位の深さぎりぎりの物。 切り込み、1ミリ。送り一刃当り0.02として240ミリ。 これで、荒引き。25回。 仕上げは、一回の切り込み5ミリで、径補正は、少なくとも3回。 一回目は2.8、2回目は2.6、3回目は2.48~2.45。 アプローチは2.9。 送りは、300位。 ヘリカルが有れば、それを使っても良いかも。
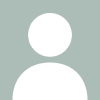
Φ5で25mmはきついですよ。ましてやそこかた横に寄せるのはもっと大変です。いっそのことはじめから往復で寄せた寸法で広げて切削してしまうほうが、あと工具ですが当然超硬ですよね、 まさかハイスなんかつかってないですよね。エンドミル加工は折ったぶんだけ経験です、社長や上司がなんといっても気にせずどんどん折ましょう。そのぶん上達します。 工具代は出世払いだ、付けとけ!ぐらい言ってやりましょう。
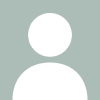
エンドミルはコレットチャックからの突き出し量が2倍になると 強度は8分の1になると感じています 内径パイ32のホルダーでパイ6のコレットを使うのでなく、 外径の小さいチャックで、突き出し量を27~28ミリぐらいに して加工するといいと思います 最初エンドミル進行方向にに対して右に0.3ほどずらして加工して います。エンドミルが倒れるので。
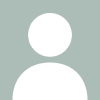
こんばんわ。 回転数が遅すぎます。最低でも倍以上にしましょう。 ハイスでも1200~1500rpm/minはあげられます。 超硬ならさらに倍以上あげても良いでしょう。 切削油や機械が不明なのであれですが、切り込みは3mm~6mm程度で加工出来ます。 トロコイド(扇状)にマクロを組めば超硬で深さ2D(12mm)は十分加工可能です。回転も6000rpm/min程度で送りもF2000は大丈夫です。 もちろん、高速加工ならエアブローかミストが必要です。 手動でエアガンで吹き付けてもすぐに終わります。 止まりのキー溝ならドリルで片方に下穴をあければ早く加工できます。 両方ならダルマを回避できるでしょう。 切り込みが少ないと、刃先が無くなりますのでお勧めしません。 トロコイドが一番ベストかと思います。 後、エンドミルは切粉の排出性の良いものを使ってください。 3枚刃のハイヘリでも良いと思います。 でわでわ
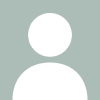
初心者に毛が生えたものですいません。 まず、それだけ細く深いと少し条件が厳しい加工ですね。 切削油はかけていますか? いくらSSだとしてもかけてあげたほうがもちがよさそうです。 で、送りが怖いとの事ですが実は逆なんです。 といいますのも、手送りですと素材自身にも分子レベルで硬い柔らかい等がありますので(熱処理済みなら別ですが)刃物はどうしても柔らかい方向に食い込んでいく傾向があります。とすると、手で送るとどうしてもガガッっとくいこんだりしたりするときがあったりなかったり。 はじめは一番送りをおとしてあげて、順に速くしていけばいいかなと思います。 あと、加工精度もあ0.1ありますので私なら刃物を荒用と仕上げ用の2本で挑みますね。 荒用で片側0.2~0.3くらい残しといてあとはさらっと仕上げます。 手間でしたら6.1のエンドミルを用意してもいいかもわからないですね。 参考になればいいのですが。筆不精ですいませんでした。