- ベストアンサー
シャフト加工の研削部保護方法についての質問
- シャフト加工における外径研削後の保護方法について相談です。
- 通常は薄い銅板を使用していますが、より簡単で精度の高い保護方法はありますか?
- 経験豊富な皆様のお知恵をお借りしたいです。
- みんなの回答 (5)
- 専門家の回答
質問者が選んだベストアンサー
- ベストアンサー
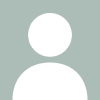
日研あたりで出している、ストレートコレットチャックなら安くて良いですよ。
その他の回答 (4)
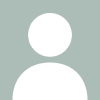
使った事は無いので、有効なのかはわかりませんが。 爪をソフトジョーに変えてみると言うのはどうでしょう。
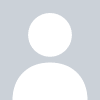
お礼
ご回答ありがとうございます。
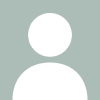
被加工材にもよりますが、うちでやるときは(2)さんの言われるようなコレットを作りワークをつかみます。(寸法により自作) ※ちょうどフライスのミーリングチャックに使っているもののようなもの。
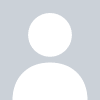
お礼
早々にご回答ありがとうございます。 寸法により自作というのがウチでは難点かもです。 貴重な情報ありがとうございました。
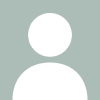
アルミか生材でコレット状のスリーブを作っておく
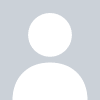
お礼
早々にご回答ありがとうございます。 やはり何か道具を用意するものなんですね。 これも一つの技ですよね。 貴重な情報ありがとうございました。
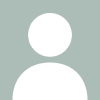
1.NC旋盤などで使っている生爪を使用する、欠点 把握径毎に必要 2.真鍮、アルミなどでリングを作り一カ所カットしソレを介してシャフトを掴む、欠点 把握径毎に必要 3. 2.のリングに外周にOリング溝をいれた後に45度くらいに分割する シャフトにOリングを付け更に三カ所上記の部品を入れていく (把握までの間に落ちないようにするため) チャックはその部分を把握する 欠点 有る程度径の違いには対応出来るがやはりいくつかの種類は必要 取り付けが少し手間、慣れれば問題ないようです。 私は有る程度径のある物を想像しておりました 径はいくらなのでしょう? それとエンドミルのコレットで把握する場合は注意しないと 傷が入ります。 エンドミルのコレットはスリットの内径側をエアーツールなどでRを付けた方が良いですよ
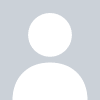
お礼
早々にご回答いただきありがとうございます。 外径は、Φ20~Φ50くらいです。 エンドミルのコレットっていいかもですね。 ありがとうございました。
お礼
早々にご回答ありがとうございます。 目からウロコです。 なるほど、それだったら転用できますね。 早速、使ってみます。 貴重な情報ありがとうございました。