- ベストアンサー
旋削加工中のワークの浮きについて
- 旋削加工中に製品が浮く現象について詳細を説明し、対策方法を教えてください。
- 旋削加工中のワークの浮きについての物理現象について説明し、対策方法を教えてください。
- 旋削加工中にワークが浮く原因と対策方法について詳しく教えてください。
- みんなの回答 (8)
- 専門家の回答
質問者が選んだベストアンサー
- ベストアンサー
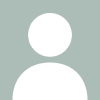
解釈するに、Z方向の当てつけに製品をあてて締めているにも関わらず、加工が終わるとその当てつけと製品に隙間が出来ているという事でしょうか?。 もしそうなら「みそすり運動」が考えられます。 つまりコレットの入口が切削抵抗で弾性変形するため、動的半径がワーククランプ部の半径より大きくなる。その差が原因で1回転ごとにわずかづつ製品が抜けるような動きをする。 エンドミルを浅く銜えて加工するとエンドミルが抜けてくるのと同じ現象だと思われます。 tokuhonさん、ページの紹介ありがとうございます。 >エンドミルの変形が少なくなって抜けにくくなるのか、弾性変形するのは変わりないので変化しないのか。 変形量はコレット側が多いと思って下さい。。 コレットの端面に当たるようにエンドミル側にツバがあるなら、エンドミルが曲がり難いようにふんばってくれると思います。でも一定以上の負荷がかかるとその力は抜ける方向にも働くと思います。 >もし、エンドミル終端を何かで受けてチャックした場合その引き込み力分はどう考えんますか? 例えばφ20を銜えられるチャックを使い、同じトルクでナットを締めると、ストッパー無い場合とある場合では、ストッパーある方が無い場合より0.15程度手前で締め付けナットが止まります。 これはテーパ6度のスプリングコレットで計算して直径にすると0.015程度になり、それだけ実際のエンドミルのシャンク外形の締め付け力がストッパー無い場合に比べて不足していることになります。 つまり引き込み力(押し付け力)は同じだけど、締め付け力は端面が浮いている場合に比べてだいぶ弱い事になります。 参考 http://www.natuo.com/imeges102/123456789.jpg
その他の回答 (7)
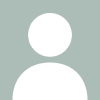
この森からのアドバイスを受けるのと併行して、コレットチャックメーカーにも相談して みてください。 今回のワークや切削条件も含めた仕様と、参考にした以前の仕様も含めてです。 コレットチャックの詳細なタイプも解らないので、餅屋は餅屋で確認です。
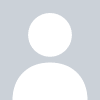
お礼
回答有り難うございます。 お礼が遅くなりすいません。 はい。現在メーカーにも問い合わせております。 今のところ仕様は問題ないとの見解なのですが、細かいデータがない(設備能力は把握できているが、チャックを含めた能力までは見たことがない)状況なのでなんとも言えないところです。 その辺も含めて確認していきます。
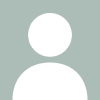
把握径がφ100で加工径がφ230ですか。 把握長やワーク長にもよるでしょうけど、 経験的に容易に浮き上がりそうな気がします。 回答(6)さんが案内されていないのでURLは記しませんが、 「エンドミル 抜け」でググってみて下さい。 回答(6)さんのホームページ内の説明がヒットするはずです。 浮き上がる量はごくわずかでしょうから確認できるかどうか分かりませんが、 本現象により浮き上がる場合は回転方向にもスリップし、 そのスリップ方向は切削力によるスリップ方向と逆方向になるので、 あらかじめワークとチャックにマーキングしておけば、 検証できるかもしれません。
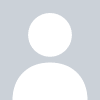
お礼
回答有り難うございます。 お礼が遅くなりすいません。 >浮き上がりそうな気がします。 と言われる方からの回答はちょっと心強いです。 アドバイスありがとうございます。 回答(6)さんのホームページ内の説明を伺いましたが...なるほどですね。 全く気にしてなかった部分ですが、コレットの掴みと力関係にそんなことがあるとは知りませんでした。 早速検証してみたいと思います。
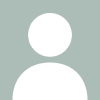
質問者さんの意図とは違うのかもしれないが、、 発生メカニズム(原因)不明の場合は、 事実(現象)確認を丁寧に進めていくことが結局は近道。 対策試行錯誤でもよいが、 原因=>対策 を忘れてはいけない。 メカニズム/理屈の説明は後付でよいと思う。 すでに、類似の加工の実績があり、 今回のワークのみで、異常が発生する。 製作のコレットチャックである。 当然、専用コレットである。 という前提で、考えて見ました。 素朴なところから、 発生頻度はどうか? どのタイミングで発生するか? 浮きの発生時の部品精度はどうか? 可能性を順番に、 密着確認の方式がわかりませんが、 部品精度への影響が確認できないようなら、 単にセンシングエラーの可能性もあります。 (文面からは読み取れなかった。) 部品精度への影響、浮き量の現実的確認ができたなら、 チャッキング系に原因を求める。 まず、油圧。 引き込み機構。および量。 ボディの形状、精度。 コレットの形状、精度。 (ワーク<=>コレットはOKとする。) ここまで、すべて問題なければ、 機械を疑うことになるが。 (既出の回答者さんとの重複があります。ご容赦を。)
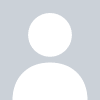
お礼
回答有り難うございます。 お礼が遅くなりすいません。 確かにおっしゃるとおり発生現状を把握することが大切なのは分かっており、原因追求と並行して、発生品を保留し問題ないか確認しているところです。 密着確認はエアによる差圧方式でこちらに問題がないことはマスターで確認しております。 もちろん、設備は新しいですが最終的には設備まで確認することは考えております。(昔に、油圧ポンプの動作圧変動でチャック推力が変化するなんて事例もあったので) ありがとうございました。
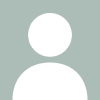
再出です。(各部から文章をコピーし易いため等で、) > 製品のクランプは外径クランプで径の公差は±50μmで仕上げられてきます。が、 > コレット側は自動搬送の兼ね合いもあり、製品径からΦ0.1~0.3程度の隙間が存在する > 状況です。 の製品径からΦ0.1~0.3程度の隙間が存在する状況ですは、 類似加工品のチャック構造を真似た物も、同様にΦ0.1~0.3程度の隙間があるのですか? コレットチャック類を最後に設計し、30年少々で記憶が定かでないのですが、隙間が大きい 気がしています。 Max0.3mmの隙間があった場合、大きな外力が加わった場合にその隙間の間で捻じれ又は 拗れが発生し、元に戻らない危険がある構造となっています。 クランプ径Φ100mmのH7公差はレンジで35μm、H6公差はレンジで22μm、クランプは外径 クランプで径の公差は±50μm(レンジで100μm)で仕上げられてきますは、少し大きいと 感じています。 そして、コレットチャックのクランプ部内径?もΦ100mmなので、公差はレンジで35μm程度。 絶対隙間を0.1mm(100μm)と設定しても、ワークがΦ100mm(0,-0.035)とクランプがΦ100mm (+0.035)なら、隙間は0.1~0.17mmとなる筈です。~0.3mmは大きいと感じました。 それと、コレットチャックの機構とクランプしている箇所が気になります。 ┏━━━━━━━━━━━━━━━┓───── ┃ ┃ ↑ ┃ ┃ │ ┃ ┃ │ ┃ ┃ │ ┃ ┃ │ ┃ ┃ │ ┃ ┃ │ ────┏━━━━━┫ ┃ │ ↑ ┃ ┃ ┃ │ ┃ ┃ ┃ M φ│ ┃ ┃ ┃ a 1│ ┃ ┃ ┃ x 0│ ─╂─・───╂───・──────・────╂─ 0│ ┃ ┃ ┃ φ │ ┃ ┃ ┃ 2 ク│ ┃ ┃ ┃ 3 ラ↓ ┃ ┃ ┃ 0 プ────┗━━━━━┫ ┃ 径 │ ┃ ┃ │ │ ┃ ┃ │ │ ┃ ┃ │ │ ┃ ┃ │ │ ┃ ┃ │ │ ┃ ┃ │ │ ┃ ┃ ↓ │ ┗━━━━━━━━━━━━━━━┛───── │ │ │ │ │ │ │ A │ B │ │←───→│←─────────────→│ 概略形状で、クランプ径φ100mmをA寸法全寸コレットチャックでクランプすることは、 コレットチャックの構造上難しいと想像します。 そして、Bの右端を加工する時、(1/2×A):(A+B)の梃子の原理で力が働き、 A寸法=50mm、B寸法=100mmならば、(1/2×50mm):(50mm+100mm)計算で25mm:150mmの 1:6となり、6倍の力(切削抵抗力)が加わることになる。 (コレットチャックの構造上で、A寸法全寸がクランプできなければ、実際にクランプ できる寸法の1/2になり、更に厳しくなる) 今回、類似加工物と異なるのは、 ア)取り代が多いことによる切削抵抗の増加はないか? イ)コレットチャック力は、切削抵抗?の2倍の内容は、前述の梃子の原理を考慮か? 又は、類似加工物との比較を梃子の原理でみているか? ウ)隙間は、0.1~0.3mmと同じであるか? エ)軸に対しての直角の倒れ止め機能が、同等性能か? φ120mmに対しφ230mmの軸方向の送り切削抵抗は、φ120mmに対しφ130mmの軸方向の 送り切削抵抗とは、加工物への捻じれ又は拗れ作用は大きく異なるので要注意。 となります。 判り難ければ、形紙等で2Dのダミーを製作して確認ください。 隙間は適当に大きく取り、梃子の原理がどのように作用し、増幅するかは確認できます。 (昔のアナログ確認方法ですがね。)
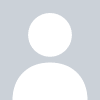
お礼
回答有り難うございます。 お礼が遅くなりすいません。 図まで書いて頂き、アドバイスありがとうございます。 おっしゃる通り、チャック径と加工径の差で切削抵抗が大きくなるのは理解しており、実際はΦ230の外周に補助チャックを設けております。(遠心力で作動するタイプ) また、軸方向の力を受けるのはチャック径の根本で基準金を設けており、加工径の裏側は製品特性上支えを付けることができない状況です。 コレットの隙間0.3は大きいですか...。 一度その辺も、従来の概念を捨てて検証してみます。 ありがとうございました。
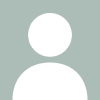
形状がいまいちわからないが 加工径はΦ230だとすると 端面と円筒面の直角がでてなく(あまい)噛んでる状態 セット時は着座にそって噛みこんでクランプ 切削抵抗とクランプ力で噛みこみがクリアされて浮く というのがありうる とりあえず 浮いたものを サンプルとして抜き取り 何が起こってるのか見るのが一番最初
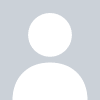
お礼
回答有り難うございます。 クランプの径と端面は前工程で仕上げており、直角度「0」とはいきませんが精度はある程度出ておりますので、弾性変形の範囲内と思っておりますが、その弾性変形がおっしゃるとおりに切削抵抗でクリアされるのかもしれません。 とりあえず、何が起こっているのか調べてみます。
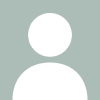
他の回答者さんの記述の如く、旋盤の老朽化等によるガタで発生する場合があります。 その他に、コレットチャックが弱くて発生する場合があります。 ? コレットチャック自体の剛性が弱い ? コレットチャック作動時のチャック力が弱い ? 加工物のコレットチャック部の寸法設定や公差設定が大きく、コレットチャックの性能が 充分に発揮できない状態である ? 加工物とコレットチャックの接触部分が、理にかなった形状でない 等々も考えられ、切削抵抗で加工物が動く現象が出てくると思います。 > ?は前工程の仕上げ径をクランプしており、Cp能力的には問題ないです。 コレットチャックは、市販品を購入ですが? それとも、オーダー製作ですか? ご存知の通り、コレットチャックは弾性変形を利用して、チャックしています。 円筒形状の内径をチャックしている場合は、公差を30~50μm位で管理させ、切削物の 円筒形状を挿入する場合は、すきまバメ程度でおこない、コレットチャック時には確実に Cp能力が切削物の円筒形状に働き作用させます。 また、円筒形状の長さ方向に1/4から1/5程度でクランプし、クランプと反対側の端を切削加工 する場合は、梃の原理がクランプ部に働き、コレットチャックが弾性変形を起こし、 切削物の円筒形状が滑る現象が発生する恐れがあります。 (痕跡が残らない滑りと云うより、微量な傾きが摩擦係数で維持されている現象です) (この現象は、ねじがねじ自身の軸力で緩まない原理と同じで、ボールねじ等には不適用) 具体的には、そのようなことが発生する状態になっていないでしょうか? 想像の範疇ですが。
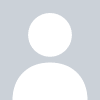
お礼
回答有り難うございます。 ?はチャック剛性は問題ありません。 ?はチャック力は製品を変形させ無いレベルに抑えていますが、切削抵抗に対しては安全率2で耐える数値に設定しております。 ?は前工程の仕上げ径をクランプしており、Cp能力的には問題ないです。 ?は...どういう状態でしょうか? 製品は円筒体でアンバランスとか発生するような状態ではありません。 確かに、切削抵抗で静止状態と加工中は状況が違うのでその差が何かを突き詰める必要はありますね。 はじめはチャック力を疑いましたが、チャックしたものを叩いてみても動く気配はなく、加工中に滑った痕跡も無いので理屈で説明できずで...。 取代が多いので、切削により背分力がマイナスに働く現象が出るのかなんて考えたりもしましたが、さっぱり解明できておりません。 回答有り難うございます。 コレットチャックは完全オーダー製作ですが、類似加工品のチャック構造を真似たリピート物で製作メーカーも同じです。 (類似加工品では、取代が少ないためか発生しておりません) 製品のクランプは外径クランプで径の公差は±50μmで仕上げられてきます。 が、コレット側は自動搬送の兼ね合いもあり、製品径からΦ0.1~0.3程度の隙間が存在する状況です。 テコの原理が働いて、コレットチャックが弾性変形し製品が滑る...ですか。 すいません、どの辺が弾性変形を起こし(コレット?ボディ?)滑るに至るのかを具体的にお願いできると助かります。
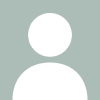
説明を追加してもらったほうが宜しいでしょう。 昔の旋盤の主軸にガタがあり切削力がワークを浮き上げるよう働きガタツクので不安定・・・逆さバイトで押し付ける切削力にして解決するとかもある。 何処から浮いて何の不具合が出ているかを 全くイメージと違ってました・・・・旋盤一般の知識では殆ど通用しない、その機械に特化した機構の問題があるように思います。 >切削速度 360m/min、加工径はΦ230 →回転数500 >クランプ時には密着を確認できておりますが加工中にこのレベルが下がり異常となる(浮いている)状況 停止後にもその状況とすると、 把握力が弱くて切削力に負けている → 切り込みを半減して再現するかを確認、とりあえずのチェック項目でしょうか 加工径Φ230そのまま掴めるコレット? 掴み部が小さければ許容荷重を超えた使いでは。 加工始めではギリギリでエラーにならないのが温度上昇でも影響すると超えてしまうとか。 一般にコレットは精度向きで、力はパワーチャックの方が勝るものと思います。しかしこれは構えが大きいので回転数が増すと遠心力が影響する。 >クランプ径はΦ100で加工径が最大Φ230となります。 決定的要因。加工条件を下げる対策しかないでしょう。 コレットは締付けを強くするほど口開きの傾向になり、それを見込むような形状で解決するのは難しいと思いますがメーカに相談されては。 回答(5)の「みそすり」はその字どおりの擦った痕跡が観察できるはずです。 応力解析の例も見たこと有りますが、 コレットは最も締付力が欲しい端面が本体ホルダ端面と最善でも同ツラ、普通は少し外な位置になってしまう構造だからです。 なので改善するにもかなり無理をすることになろうかと思います。なので大径部分だけ傾斜的に切込みを少なくする方法が早道かと
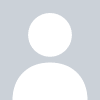
お礼
ありがとうございます。 追記させてもらいましたのでアドバイスよろしくお願いします。 この機械に特化した機構ですか...。 チャックはコレットチャックで油圧で引き込んでクランプしてるだけなので、特別な機構はしてないと思っておりますが。 ですが、停止後にもその状態かは確認しておりません。 (加工後にアンクランプして異常が出るので) その状態を確認する必要はありますね。加工後でもそれが維持されていれば相当な力が働いているでしょうし。 切り込みなどの条件変更はサイクルの関係上あまり出来ないので、とりあえず加工中と加工後の状況を詳しく確認して考えてみたいと思います。 ありがとうございます。 回答有り難うございます。 クランプ径はΦ100で加工径が最大Φ230となります。 すいません、説明が抜けておりました。 ただ、計算上はコレットの許容荷重は超えてはおりません。 おっしゃる通り、最終的に精度が必要なのでコレットを使っております。 熱鍛品とかだと取代大で断続切削となるのでパワーチャック使ったりしますが...。 回答有り難うございます。 お礼が遅くなりすいません。 暫定的には加工条件を下げて対応する予定ですが、最終的にはチャック構造を見直す必要がありそうですね。 結局のところ、コレットチャック自体が切削力に耐え切れてなさそうなのが徐々に見えてきており、その現象さえ解明できれば対策をどう打つかは決まりそうなので。 ありがとうございました。
お礼
回答有り難うございます。 お礼が遅くなりすいません。 回答(7)さんから紹介されてHPを拝見させて頂きました。 とても詳しい説明で、エンドミルの銜え長さと力に対して起きる現象に、今回の案件はとても似ていると感じました。 何らかの形で実証できないか検討してみたいと思います。 ありがとうございます。 2つ質問させてください。 このエンドミルの「みそすり運動」は、例えばですがエンドミルのクランプ根本につばがあって、軸方向の力を受けるものがある場合はどうなりますか? つば自体は厚みがあり剛性があると想定したとすると。 エンドミルの変形が少なくなって抜けにくくなるのか、弾性変形するのは変わりないので変化しないのか。 あと、コレット自体はチャックの際に引き込みの力が働くと思います。 もし、エンドミル終端を何かで受けてチャックした場合その引き込み力分はどう考えんますか? よろしくお願いします。 回答ありがとうございました。 エンドミルの抜けメカニズム「みそすり運動」が今回の製品の浮き事象に当てはまりそうで、とても参考になりました。 早速色々検証して、裏付けを行なってみようと思います。