- 締切済み
コレットチャックの着座センサーについて
- コレットチャックの着座センサーについて教えてください。
- コレットチャックの着座センサーはエアーでの着座確認ができるセンサーで、鍛造品には向かないとされています。
- メーカーや種類、使用する上での注意点について教えてください。コストは掛かるかもしれませんが、ご教授いただけると幸いです。
- みんなの回答 (7)
- 専門家の回答
みんなの回答
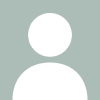
状況が観えないので、簡単に記述しますが、 コレットチャックとストッパーの構造が悪いのでは?? 良く切粉が詰まるコレットチャック&ストッパー構造では?? 的な発想の改善はできませんか?
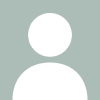
回答(3)の者です。以前、客先で同様の内容を以下の様に検討しました。 ? 物理的(はけ等)に、コレットチャック面を清掃して、 不良率が幾ら低減できるか、サイクルタイムが幾らアップするか、等で コストパフォーマンスが……。 ? よく不良が出る確率が高い切粉サイズを含めた寸法を、多目に加工寸法 として、次工程でその分を加工する。 不良が出る切粉サイズは、統計を取ると*.*mm以下が9*.**%となり、 次工程以降に、その加工を分担すると、殆どサイクルタイムに影響が なく、不良率が著しく低下する ? エア等のアクチュエータをモジュールで取付、その先端にセンサを取付 外部モジュールから着座確認をする。例えば、距離確認センサ等を使用 して。チャックをスロー回転させると、全周確認ができ、旋盤回転軸上 に調整すれば、隙間代が調整できます。後は、切粉のパターンと鍛造 ワークのパターンを認識できれば、確認できます。 キーエンスさん等のセンサ屋さんに、一度相談してみて下さい。 等々検討してみました。 何れも、現状の不良パターン分析が必要でした。 そして、?が有効で、ワークの脱着時間で清掃、加工時間ではけの清掃 をシステム化した経験があります。 以上を参考までにアドバイスします。
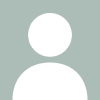
かなりバラツキが大きいですね センサーもそうですが これだけバラツキが大きいと チャック側のストッパー部の改善・チャック内部からのOILブロー・エアーブロー等を先にやるべきと思います、ストッパー形状は べた当たりではなく なるべく点当たりにし 切粉による害を避ける、ワーク脱着時に主軸内部からのOIL・エアーブローを追加し(断続ブロー効果的) 尚且つ 放射状にOIL等を出す様にする 加工中の切粉の流れをよく観察し チャック内部に切粉が行かなくなる様な OILのかけかたにする等です、又L寸が2mmとは ローダーのチャッキングミスの可能性も捨てきれませんね よ~く機械内部を観察していれば ヒントが見つかると思います 頑張ってください。
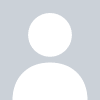
お礼
ご回答ありがとうございます。 2mmほどの物は滅多に出ないのですが、やはり0.05~0.2くらいの物は 一万個に1~2個発生してしまいます。 質問なのですが クーラントを放射状というのは具体的にどういう事でしょうか? ちなみに現時点で弊社設備は主軸内からはエアーしか出ないのと 刃物側とクーラントホースから強圧にてエアーを掛けております。
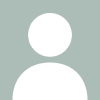
補足要求させて下さい L寸(全長)を選別していて NGとなる部品は規格からどの位外れているのか 又 傾いており 例えば 片側はOKだが180度回転させると規格外になるのか 詳細が欲しいです。
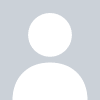
補足
製品にもよりますが(切子、ゴミの大きさにもよる) 交差が±0.05の物に対しまして NGになる製品は0.05~2.0くらいL寸法交差が外れてしまいます。 かなりバラつきが激しいです。
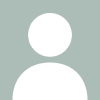
・エアーでの着座確認・鍛造品には向かないの意味は、 着座確認センサ取付で、鍛造品がメインの取扱 エアの着座確認は、着座部分が鍛造部分なので 背圧が上がらなく、確認が取れないでしょうか? 切粉が挟まって、寸法不足なら、その切粉を検知してOKを出します。 切粉と鍛造物をセンサで見分けなければいけませんから。 それなら、やはりエアセンサで検知です。 コレット着座面に何箇所か設置すれば、エアブローの代わりにも使用 できますよ。(穴1個に、1センサで、数か所設置) そして、全部背圧上昇が無い場合か、それに近い場合NGにて、検討 下さい。エアブローで取れない不具合を発生させる切粉の大きさは、 おおよそ特定されているのでしょう。その大きさと、穴径、着座面の 大きさで、エアセンサ(圧力センサ)の使用を決めて下さい。 <SMCさん等の営業マンに確認すると良いでしょう> 気になる事が一つ、コレット動作に切粉は影響を及ぼさないのでしょうか?
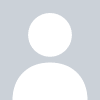
補足
回答ありがとうございます。 〉着座部分が鍛造部分なので背圧が上がらなく、確認が取れないでしょうか? そうです、私の知っている限りでは鍛造品の場合、直角度が出ていない為 着座面が密接に当たらないという事です。 直角度が出る様に機械加工していれば問題ないのですが… コレットの動作に関しては今のところ問題にはなっておりません。 検討させて頂きます。ありがとうございました
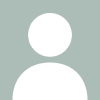
・エアーでの着座確認・鍛造品には向かないの意味は、 着座確認センサ取付で、鍛造品がメインの取扱 エアの着座確認は、着座部分が鍛造部分なので 背圧が上がらなく、確認が取れないでしょうか? 切粉が挟まって、寸法不足なら、その切粉を検知してOKを出します。 切粉と鍛造物をセンサで見分けなければいけませんから。 それなら、やはりエアセンサで検知です。 コレット着座面に何箇所か設置すれば、エアブローの代わりにも使用 できますよ。(穴1個に、1センサで、数か所設置) そして、全部背圧上昇が無い場合か、それに近い場合NGにて、検討 下さい。エアブローで取れない不具合を発生させる切粉の大きさは、 おおよそ特定されているのでしょう。その大きさと、穴径、着座面の 大きさで、エアセンサ(圧力センサ)の使用を決めて下さい。 <SMCさん等の営業マンに確認すると良いでしょう> 気になる事が一つ、コレット動作に切粉は影響を及ぼさないのでしょうか?
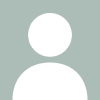
ホームページアドレスを添付しました 参考にしてみては如何でしょうか。
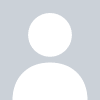
お礼
回答ありがとうございます。 検討させて頂きます。
お礼
非常に興味あるご回答有難うございます。 そこでですが、何点か気になる点があります。 ?ハケによるチャック面の掃除 これは例えばチャック端面であればハケを使う事は容易だと想像出来ますが ストッパー(基準)がコレットの中にある場合どういったやり方で行うのでしょうか? ?の場合ですと加工は2チャッキング以上の加工工程が必要な物と考えてよろしいでしょうか? 弊社は鍛造物を1チャックで加工してしまう物が多い為、もし上記の事でしたら難しいかもしれませんね。 質問ばかりで申し訳ありませんが宜しくお願い致します。