- 締切済み
※ ChatGPTを利用し、要約された質問です(原文:電機子(コンミテータ)の切削加工について)
電機子(コンミテータ)の切削加工について
このQ&Aのポイント
- 電機子の切削加工に関する要点と方法をまとめました。
- 外径22mm・内径8mm・全長25mmの電機子の製作方法について解説します。
- 内・外径のバラつきや真円度、円筒度、面粗度が安定しない問題の解決方法についてお知らせください。
- みんなの回答 (1)
- 専門家の回答
みんなの回答
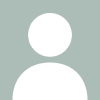
noname#230359
回答No.1
お困りの >内・外径共に径のバラつきや真円度、円筒度、面粗度が安定しません は、刃物よりも、ワークのクランプに問題があるように読み取れます。 内径・外径の加工共に、すくいがポジのインサート(チップ) を使われているでょうが、先ずはより切削抵抗の低い超硬 インサートで試してみては如何でしょうか。 (寿命の問題はひとまず棚上げにして) 内径加工もカタログ標準品(三菱,京セラ,住友,タンガロイ) で対応できるので、お会社でよく使われているメーカの工具を 探してみて下さい。
お礼
回答、有難うございます.ご指摘の件ですが 切削抵抗により、主軸の振れやクランプ時の振れが悪さかと 思い、時間毎、ロット毎等で初期の精度を調べてみましたが 特に周期的な変動もみられませんでした. お手数ですが宜しくお願いいたします.