- 締切済み
※ ChatGPTを利用し、要約された質問です(原文:ハンチング防止対策について)
ハンチング防止対策について
このQ&Aのポイント
- 厚さが40mm~50mmのワークをパンチ形状で加工した際、ハンチングが原因と思われる縦にスジがワークについてしまいます。
- 工作機械はソディックAQ550L、ワイヤー線径φ0.2加工条件は取り扱い説明書の条件を使用しております。
- 色々加工条件などを変えてみましたがなかなか上手くいきません。何か防止策がありましたら教えて下さい。
- みんなの回答 (1)
- 専門家の回答
みんなの回答
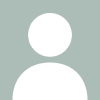
noname#230359
回答No.1
厚みが40から50mmと言う事は一定のワーク厚ではないと言う事ですか? ハンチング現象は加工ON・OFFが繰り返しが縦スジに現れたと理解して 良いでしょうか?(加工が安定せず、一定の状態のスパーク出ていない状態) どの箇所で出ているのか?カット数やどの条件(何回目)がポイントになりますが・・・ 複数カットされている場合は 各条件の寄せ量を狭く調整してみてるのが効果的 縦筋の位置が-Y軸で必ず出るなら、ヘッドのオジギも原因の時があります 他に考えられる原因では、 板厚が変化している時は加工液(上下)の圧力バランスを変えてみる 水圧によってワイヤー線がビビルような状況もあります。 縦筋が全体に一定の周期(ピッチ)で出ている場合は 主にワイヤー線のボビンの巻状態が悪かったり、ワイヤー経路でのプーリー等 に引っ掛かりや、溝が出来ていたりしている事もあります ワイヤーの送りの状態をみて、特にワークに近い所でワイヤー線がブレていないか、スムースか見てみるのもいいと思います。 一部分に発生してしまう場合は ワークの加工歪みによる縦筋もあります この場合はスタート穴のバランス(数・位置)切り残し位置や距離など、検討して変更するほうが良いですね。 機械のメンテに問題なかったり、癖さえ把握していれば、 私の経験では、ワークの歪み等で発生する事が多いですね 加工条件や補正値の入力に謝りが無ければ、 全周に発生する場合はおそらく機械的な問題を疑ったほうが良いですね 縦筋に周期的な現象(たとえば、10mmおきに出ている)は無いですか? 給電ダイスのチェックや、経路、ワイヤー線調べたほうがいいかも。 全ての条件で発生するのはおかしいです。
お礼
加工条件や補正値は良いと思います、御指摘にあった給電ダイス、ワイヤー経路などに異常はありませんでしたので、メーカーに問い合わせしてみたいと思います。アドバイスありがとうございます。
補足
ご回答ありがとうございます。厚みは一定の物で、ワークの厚さにかかわらず ワーク全周に縦スジが発生してしまいます。カット回数は4回カットで加工条件は全ての条件で発生し、どのタイミングでスジが発生しているかは不明です それと、ハンチングと記入しましたが取り扱い説明書を参孝に原因と思われる との推測ですのでハッキリとした原因はわかっておりません。