- ベストアンサー
薄肉リング加工の注意点と旋盤選定について
- 薄肉リング加工において注意すべきポイントや旋盤選定について検討しています。
- 類似品加工の実績から、扇状形状の爪を製作しパイプの変形がないようにする必要があります。
- パイプ素材の残留応力や焼鈍の影響、材料取りやチャッキングに問題がないかを考慮しています。
- みんなの回答 (2)
- 専門家の回答
質問者が選んだベストアンサー
- ベストアンサー
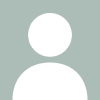
その他の回答 (1)
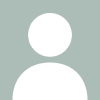
関連するQ&A
- ステンレスの薄肉パイプ加工について
いつもお世話になります。 今回、薄肉のステンレスパイプにエグリ加工をすることになりました。 直径が40mmぐらいで、板厚が1?無いぐらいなのでそのままの加工は難しいらしく、中に鉛を詰めた状態で加工するそうです 薄肉のパイプをエンドミルで加工した時に剥がれたり破れたりしないかが心配ですが、加工に対してのアドバイスをいただきたいです また、エグリの形状が歪なのでマシニングにて加工しようと思いますが、切削液(水溶性)に鉛が溶けたりして害になることはありませんか?
- ベストアンサー
- 切削
- 旋盤でφ38厚み3.5mmの端面加工の平面度が出…
旋盤でφ38厚み3.5mmの端面加工の平面度が出ない!!! 旋削加工でφ38厚み3.5mmのワークを三爪チャックでクランプし端面加工すると、端面の平面度が良くありません。三爪なので3点当りになると考えていたのですが、真円度計で平面度を取ると、楕円形状になっていました。 チャック圧を最低に設定したり、粗仕上げに加工を分けたり、爪当りを変えたりと色々やって見ましたが、なかなか5μ以下に改善する事が出来ませんでした。 薄肉のワークの歪が出ないような加工方法のアドバイスを頂けないでしょうか。よろしくお願いします。
- ベストアンサー
- 旋盤
- 精密薄肉パイプ加工
STKM12Aパイプ材Φ219.5内径203.0 長さ90MMを 外形217.4内径208.0 長さ88mmに仕上げます。 t4.5mmの公差は、±0.1mm 今は、外形に特殊な爪っを作り加工していますが、どうしてもひずみが、出てしまいます。 内径もひずみが出てしまいます。 加工に、なにかいい手立てはないですか 今は、最初に外形加工ほぼ外形がすっぽり隠れてしまうチャック爪製作し加工をしています。外形加工後 寸法±0.4ぐらい 内径も前面が当たるように爪を作り制作しています。 加工後±0.4ぐらい もっと精密に加工がしたい、簡単な加工方法が、もしあれば教えてください。
- ベストアンサー
- 旋盤
- 内径加工時、キズがついてしまいます。
いつもお世話になっております。 STKM400のパイプ材(φ50×φ35×135)をボーリングバーでφ45まで広げていきます。(L=39) 面粗度はうるさくないので、荒、仕上げは一本で加工しております。 この加工中におきる仕上げ面のキズに困っております。 加工後、φ45 0.+0.039の栓ゲージにて検査をするのですが、少しでもキズあるとゲージが入りません。 キズの種類はムシれたり、白くなったりします。 条件はV=200~250 F=0.2~0.25 チップは住友のTPMTのSUブレーカーです。 加工後、キリコはぱらぱらになるのですが、ワークの中にかるく詰まってる感じです。 6インチの旋盤なのですがワークが奥まで入らないので、高爪を加工し、ストッパーになるような形状にしております。 キズの原因はキリコだと思うのですが、どなたかキズが減るような良いアドバイスをよろしくお願い致します。 今の爪の形状ですと、キリコが奥から出にくいので、ストッパー径の部分の径を広げようと思っております。
- 締切済み
- 旋盤
- 材質ADC12形状Dφ87dφ83L120の内径…
材質ADC12形状Dφ87dφ83L120の内径加工真円度問題 タイトルにある筒形状のアルミダイカスト品の片側8mm程度を旋盤三爪チャックでクランプ(ワークL120mmで爪掴み代8mm)し、反対側からL95mm程度内径加工をしているのですが、真円度要求が15μ以内と厳しく、公差をクリア出来ません。 調査を行っているのですが、チャックに近い部分は三爪のおむすび形状の歪が出て、チャック圧の改善や爪当りの改善でクリア出来たのですが、爪から離れるに連れて真円度形状が楕円になり大きくなっていて、公差を越えてしまいます。 突き出しが長いと思うのですが、チャッキング代を変える事が出来ません。加工の面から保持方法でよい方法が無いでしょうか。 また、ワーク全長が短いL50mm程度のワークでも同様の不具合が出る事があります。素材の前工程やアニール処理にも問題があるのではと考えています。当社では鋳造→アニール(250℃2H)→ショット→塗装→加工とになっているのですが、工程やアニール条件等おかしい所はありませんでしょうか。アドバイスお願いします。
- ベストアンサー
- 金属
- SUS316Lの薄肉切削
17角で高さ6.5のSUS316Lのブロックに外径φ13内径φ5のリング溝を深さ6.1 まで削り、反対から深さ0.2削った形状のものを作りたいと考えています。 旋盤で加工していくと薄肉部が0.2のため、バイトの刃先でたわんでしまいます。 なんとか切削加工で作りたいのですがどうしたらよいでしょうか?
- 締切済み
- 切削
- アンドロイドのスマホとブラザー製のDCP-J525Nプリンターを同じ無線LANに接続しているにも関わらず、スマホからの印刷ができません。通信エラーが発生しています。
- 問題の製品はブラザー製のDCP-J525Nプリンターです。アンドロイドのスマホと同じ無線LANに接続していますが、印刷ができません。通信エラーが表示されます。
- スマホからDCP-J525Nプリンターへの印刷ができません。スマホとプリンターは同じ無線LANに接続していますが、通信エラーが発生しています。
お礼
丁寧なご回答ありがとうございます。 突っ切りの影響、荒加工後ひずみを抜くために2日放置というのは 参考になりました。 やはり、別工程が必要なようですね、問題はチャッキングの方法…