- 締切済み
箱型成形品の型設計の注意点
- 成形品の型設計において、注意すべきポイントはいくつかあります。例えば、箱型成形品の場合、ヒケの問題が起こることがあります。対策として、型の補正や冷却の工夫が必要です。
- 成形品の型設計では、箱型成形品を設計する際に特に注意が必要です。ヒケの問題が発生する場合があるため、型の補正や冷却による対策が必要です。
- 箱型成形品の型設計において、ヒケの問題が起こることがあります。この問題を解決するためには、型の補正や冷却の工夫が必要です。注意点としては、対辺が内側によって正四角形にならないことがあります。
- みんなの回答 (2)
- 専門家の回答
みんなの回答
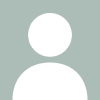
こんにちは、折り紙で折ったような角ばった 弁当箱を想像すればよいのでしょうか? だとすれば、平均肉厚1.5ではヒケよりも 変形による壁の倒れや底面の歪みが問題にな ると思います。壁部の倒れ量は2030mm くらいになるはずです。それを予測し型を湾 曲に製作するのはかなり大変になると思われ 事実上、型で補正は難しいと思います。 既に起工なさっているのなら?手遅れですが 実際にスーパーや量販店などでプラスチック 製の弁当箱をご覧になってみて下さい。 全ての折り角にR2030くらいを設けてあ ります。 あれはデザインでもあり樹脂内応力による強制 倒れなどの変形を回避する目的もあるようです。 更に、端面には縁が付けられ倒れないよう補強 を施してあり、変形防止の理想の形と思います。 打ち合わせの段階でできる限り変形しない形に 製品設計を変更してもらう事の方が理想の対策 かと思われます。 最後に、ゲートの位置は底面中央で樹脂が均等 に充填されるようにするのが理想です。総体積 も多いのでガスベント等の設置も十分に必要で すし、コア・キャビ内の温調回路も十分に検討 し、抜きテーパーも許される限り設けることが 型側でできる対策かと思われます。
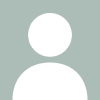
新東工業の安形(アガタ)と言います。 イメージ的には弁当箱の様な物と思いますが、引けで困るようでしたら、通気性金型材料(ポーセラックス?)があり、成形圧を3割位下げても成形出来、引けを押える事が出来ます。以前の事例では引けとか平面部分の歪みが半分位になりました。 また、箱型と言う事で収縮のため離形で困った時も通気性金型材側からエアーを吹き出し、離形性を良くしたケースもあります。詳細が必要でしたら資料を送付いたしますのでご連絡下さい。 TEL:0533-85-0303