- 締切済み
※ ChatGPTを利用し、要約された質問です(原文:リボン材の穴明けバリ)
リボン材の穴明けバリの原因と対策
このQ&Aのポイント
- 0.6tのリボン材に5×16の小判穴を2ヶ所明ける金型を作りましたが、その一部にバリが出て困っています。不思議なことは、出たり出なかったりするのです。クリアランスは、0.06です。可動ストリッパーで、押さえ力は、SPC材よりやや強め。もちろん金型に欠けはありません。プレススピードは50RPMから100RPMの間で試しました。2つの穴のうち、1つは問題無く、もう1つの穴の0.5mmぐらいで、毎回同じ箇所です。
- リボン材の穴明けバリの問題について、原因と対策を考えています。0.6tのリボン材に5×16の小判穴を2ヶ所明ける金型を作成しましたが、一部にバリが出てしまいます。不思議なことは、バリが出たり出なかったりすることです。クリアランスは0.06で、可動ストリッパーで押さえ力はSPC材よりもやや強めです。金型に欠けはなく、プレススピードは50RPMから100RPMの間で試しています。2つの穴のうち、1つは問題なく作成できますが、もう1つの穴の0.5mm付近で毎回同じ箇所でバリが出ます。
- リボン材の穴明けバリに関する問題があります。0.6tのリボン材に5×16の小判穴を2ヶ所明ける金型を作成しましたが、一部にバリが出てしまいます。不思議なことは、バリが出たり出なかったりすることです。クリアランスは0.06で、可動ストリッパーで押さえ力はSPC材よりもやや強めに設定しています。金型には欠けはありませんし、プレススピードも50RPMから100RPMの間で試しています。2つの穴のうち、1つは問題なく作成できますが、もう1つの穴の0.5mm付近で毎回同じ箇所でバリが出ます。
- みんなの回答 (1)
- 専門家の回答
みんなの回答
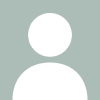
noname#230359
回答No.1
0.6tのSPCC材ならばクリアランスは0.06mmは範囲内ですが、私ならば0.04~0.05mmにします。 二つの穴のうち1つだけバリが出るのは、両方の型が条件が違うと推測します。出たり出なかったりとのことから推測すると、ダイの形状と位置は変わらないので、パンチが何かの条件で動いているかもしれません。 2つのパンチの形状の違いと平行度とバッキングプレ-トの変形とを調べた方がいいかもしれません。 文書から推測すると可動ストッパ-の押さえ力が小さい様に感じます。押さえ力強くて困ることは無いと思います。押さえ力が弱いと抜く瞬間に材料がテコの原理で浮き上がります。バリが出やすくなり、ストリッパ-の穴とパンチ位置の関係でストリッパ-が動いてパンチ横に押す力が働く場合があります。 包丁で野菜切るとき速く切った方が綺麗の様に、プレスのせん断加工も同じです。電子部品に使用する薄板リ-ドフレ-ム加工は3.000rpm 以上のプレスが多いのは、生産効率と高品質(バリ、ダレが小さい)の為です。 参考: バリとダレの少ない綺麗な穴又は抜きブランク造る型構造 抜き穴にバネ又はウレタンゴムで昇降する受けパッド機構にする。外は可動ストリッパ-で押さえ、パンチと受けパッドで挟まれてブランクが抜かれて、パンチが上昇するとカスが元の穴に押し戻す。 何ステ-ジ後に抜き落下させます。綺麗な製品が出来ます。 少し参考に成れば幸いです。
- 参考URL:
- http://fac9999.web.fc2.com/
お礼
回答ありがとうございます。 今まで多くの抜き型を作ってきましたが、このような現象は始めてです。 リボン材という高硬度材も初めてです。 ご指摘された”パンチが何かの条件で動いている” ”バッキングプレ-トの変形”という初歩的な点かも。と思いました。 再度点検してみます。ありがとうがざいました。 とりあえず、ガイドピンを太くし、ストリッパー圧力をさらに強くしたところ、連続100個バリは出ませんでしたが、本当の原因はわかりません。 いろいろな要因があったのかもしれません。 ありがとうございました。