- ベストアンサー
※ ChatGPTを利用し、要約された質問です(原文:コンパウンド(スタンプ)抜き型の異常について)
コンパウンド(スタンプ)抜き型の異常について
このQ&Aのポイント
- コンパウンド(スタンプ)抜き型でバリが発生しております。相反する現象が発生しております。
- 材質はSPC270C、厚さ1.2mm。クリアランスは片側0.07mm(約6%)です。
- 発生原因、また修正の方法などご存知でしたら、よろしくお願いいたします。
- みんなの回答 (1)
- 専門家の回答
質問者が選んだベストアンサー
- ベストアンサー
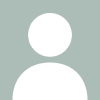
noname#230359
回答No.1
三角パンチのL寸をダイより0.5~0.6短くしては、どうでしょうか。 タイミングをずらして外形をほぼ抜いてから穴を明ける。
お礼
結局原因わからぬまま、ダレを無視してクリアランスを広くとることに落ち着きました。 今後は落し(ストリッパ)にバネ荷重を掛けて、ワークを押えてから抜くとか、回答いただいたように、パンチをタイミングずらして抜く等の方法を試してみたいと思ってます。 ありがとうございました。