- 締切済み
リーマ等の芯高について
- リーマみたいなイメージの段付ザグリカッター(特注)を使用しているが、チップブレーカーを追加工でつけた場合の切削性の影響はあるのか疑問。
- 芯下がり仕様の工具(リーマ)も存在するが、先輩からは中心からの引き出し線を下げれば芯高ゼロの考えと変わらないと言われている。
- 刃具メーカーの設計担当者との打ち合わせで、中心線からずれたブレーカー形成は切れ味が向上する方向になると判定された。
- みんなの回答 (2)
- 専門家の回答
みんなの回答
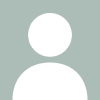
旋削でもボール盤でもフライスでも同じで センターで加工する刃物なら芯高は関係ない 先輩の意見が正しい >先端部にチップブレーカー・・・・ 多分、刃物は「バニシングリーマ」では? メーカーによっては 刃先の断面がフラットのポジ形状でもネガ形状でも製作できる。 切れをもっと良くしたいので すくい角を付ける為のブレーカーでしょうか? 通常ブレーカーは切粉のせん断が目的 切粉処理が関係なければ 単なるすくいでしょう。 >量産加工の食いつきで不快な音が出てしまう事象が発生しており 新品と数十個加工した状態も同じでしょうか? 仮に新品時の状態が良くないのなら 先端部の形状をもっとミクロ的に考察してホーニング量の確認も必要 場合によってはネガ形状にした方が良い場合もある。 ※バニシングツールはガイド部がある為に形状的にフラットな刃先が一般的ですね。
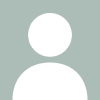
>旋削刃具ではないので芯が下がる様な感じにしても中心からの引き出し線を下がった部位に 引けば、芯高ゼロの考えと変わらない。 の先輩が正しいです。 旋盤でもバイトが斜めに動くことが多いが、フライス刃では芯高のコトバを使わないほうが良いと思う。拘るなら刃先を水平位置に回転して考える。 >ブレーカーをつける場合 あくまでも刃先を水平位置に回転して考える。 90°回った真上でも何処でも法線(中心からの引き出し線)と接線で考えるのは難しくなく慣れだけでしょう。
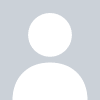
お礼
岩魚内 様 お世話になります。アドバイス感謝いたします。 芯の話は誤解を招くので今後は使わない様にしたいと思います。 (図面を描いた時に中心からずれて描く・・といった表現の方が良いのかもしれませんね) 回転工具なのに図面は固定してある状態で表現しているので 間違いやすいですね。CADで描くと判りやすいですね。 恐らく図面を描く時には中心線から描く事が殆どでしょうから、刃の位置が中心からずれて描くといった場合に切削性に関しての理屈は無いから当然わからないと言った考えなのかもですね。ネガ、ポジという感じでは理解できますけど・・。 会社の先輩がアドバイスしてくれた内容に対し、理解しましたとはその場でいえなかったのですが、皆さんに良いアドバイスをいただきましたのでまだまだ全部とは言えませんがお伝えしたいと考えております。 ありがとうございます。 もし、差し支えなければまた色々アドバイスをお願いします。 進捗も記入していきたいと思います。
お礼
mytec 様 お世話になります。アドバイス感謝いたします。 私も後にCADで刃具図面を描いて考えてみました。 要するに刃具図面上で描いた状態からそれてもそれが”芯から下がる”と言う表現ではないのですね。 ただ、今回の困り事事象にはその状態が直結するかどうかはまだ判らない部分ですので、刃先状態の仕様を少し変えたりして切削テストを行なう考えです。 ちなみに、バニシングリーマという解釈で良いですが後工程でダイヤリーマで仕上げている事もあって工具メーカーとはザグリカッターと言う様に分けています。なのでおっしゃる通り一般的にはリーマで良いと思います。 不快な音に関しては、毎回でなくある程度加工数をこなした刃具でも発生してますので、恐らく新品時でのビビリ(Tスロでよくある話)という解釈には今回捉えずらいと今は考えております。 リーマ形状でのネガ、ポジの件は私も知っていて刃先チッピングによる内径維持トラブルを回避するために、ネガ仕様の工具を作って効果を得た経験があります。なので今回の事象に関してその経験が生かせるかどうかは当然考えておりましたので今回のアドバイスを基にもう一度考察したいと考えております。 添付していただいたHPも参考に努めますので、もしその他のアドバイスや情報があれば宜しくお願いします。 ありがとうございます。