- ベストアンサー
JIS G3131 SPHCの定数と実測値の誤差を検証する際に考えられる原因
- JIS G3131 SPHCの定数を入力してシュミレーション結果と実測値の誤差を検証する際、原因としてヤング係数の違い、現物とモデルの整合性、技術的な問題が考えられる。
- ヤング係数が異なる場合や精度が悪い素材に対応する定数がない場合、現物とモデルの整合性が取れていない場合、技術的な問題がある場合に誤差が生じる可能性がある。
- これらの要因が組み合わさり、実測値と仮想値の誤差が発生することがあり、5割程度の合致では基準外とされる。しかし、全てが原因ではない場合や影響がほとんどない場合も考えられる。
- みんなの回答 (10)
- 専門家の回答
質問者が選んだベストアンサー
- ベストアンサー
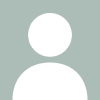
注意喚起のため再出させていただきます。 リアル(と思われる)3Dモデルを作って、時間をかけて解析するのは ナンセンスだと思います。 現実と同じモデルなんて絶対に作れません。 質問者様が求められているのは何ですか? 大きなたわみが発生することの裏づけをすることですか? おそらく違っていると思います。 研究者でもなければそこまでのことは不要でしょうから。 求められているのはたわみを減らす方法ではないですか? 現状の解析は早く終わらせて改善案の解析を進めるべきでは? 結果の表示方法の見せ方で十分説得できる物になると思います。 カラーマッピングのレンジを補強前と補強後を同じ範囲にして 当初赤色になっていたところが黄色や緑になることを比較する など、数値にこだわらせない工夫ができると思います。 結果報告ではなく、補強案のプレゼン資料と思って作って みてはどうでしょうか?
その他の回答 (9)
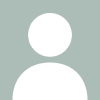
再出です。 やっと、質問内容が理解できました。 > 定数を入力しシュミレーションして出た結果ですが、実測値と仮想値が5割程度しか > 合致しませんでした。 は、例えば 扉の枚数10枚中、5枚が実測値と仮想値が合致していると思える範囲におさまる と感じていたので、実測では5mm沈んだ箇所を、解析でシミュレーションしたら2.273mm沈む となり、2.273mm/5mm≒0.5=50%=5割とは思いませんでした。 失礼しました。 さて、解析には、コの字の補強の溶接位置等は正確に反映されていますか? そして、扉本体の折り返し部分の形状や溶接方法も、正確に反映されていますか? > 弾性係数が210000N/mm^2の時真ん中付近が2.273mm沈む、弾性係数が105000N/mm^2の時真ん中 > 付近が4.545mm沈むというシュミレーション結果になりました。 と同様に、溶接条件を極端に変更してや、実際に近付けて、沈み量が2.273mmから大きく変化 するや5mmに近付くなら、その可能性があります。 <どうせ、実物の溶接仕様詳細確認は、できないのだからね。> メッシュサイズを極端に変更して、沈み量が2.273mmから大きく変化するや5mmに近付くなら、 その解析ソフトの特性なので、原因の一つとなります。 <PCが高性能になった最近でも、そんな傾向があるのかが、疑問ではありますがね> 何れにしろ、確認して消去法で原因を見つける必要があります。 只、弾性係数が210000N/mm^2 ⇒ 弾性係数が105000N/mm^2ってことはありませんし、 板厚の差やSPHCとSPCCの差でもないように思います。 別で、3D-CAD解析をしてもらい、3D-CAD解析時に溶接条件を色々変えて、確認してみれば と考えています。 溶接の仕様でのシミュレーションができないなら、 ? 溶接接合あり、なし、にてのシミュレーションする ? 補強と同じ重さの中央集中荷重換算した物を置く、にて代用シミュレーションする ? 補強なしの外板のみでシミュレーションする にて、沈み量を算出し、経験が必要ですが妥当性を確認するかです。 補 ヒンジ取付部なので ↓強 ↓折り返しが長い _ _ __ │____________________|______│ ▲ ▲ │←─── ****mm ───→│ │←─── 1950mm ───→│ の仕様であれば、寸法を明確化すれば、簡易的な沈み量計算は可能です。 補足で仕様を明確化する手法での確認法が良いと思います。
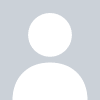
お礼
ご回答いただきありがとうございます。 実測値に関しては1枚の検査結果なので、違う扉を調べたら設置する格好ですでにたわんでいるなどということもあると思います。(それは完全な不良品ですが・・・。) 溶接を入れることはできるんですが、実際に溶接までシュミレーションに反映されているのかといったら不透明なところがあります。さらにいろいろな情報を加えれば加えるほど動きが鈍くなるので、今のところは最低限の情報で逃げて結果がでやすいようにしています。 このやり方も限界を感じるので、ちゃんとした情報をいれこんでたとえ時間がかかってもやらないといけないと思っています。
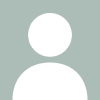
解析素人なので的外れでしたら御免なさい。 誤差要因としては要素(メッシュ)が不適切と考えられます。 基本的に板厚が薄い場合にはソリッド要素だと精度が悪化し 本来よりも硬い解が得られやすいです。 ですのでソリッドシェル要素にするとか、一次要素よりも 二次要素にした方が良いでしょう。 ところでSolidworksはSimulation Xpressか何かでしょうか? その場合、扱える要素が限られていたかと思いますので 上記のようには出来ないかも知れません。 そうなるとあとは板厚方向にも十分な分割数となるように ひたすらメッシュサイズを細かくするしか無さそうな気がします。 メッシュサイズを変えて解が大きく変わるなら、 解析精度が十分でないです。 そんな時にはメッシュのサイズを変えながら、解に収束傾向が 見られるまで何度もトライしてみるしか無いでしょう。 Premiumでしたらこの辺を参考にシェルメッシュで解析してみたらどうでしょうか。 http://help.solidworks.com/2012/Japanese/SolidWorks/cworks/ID_Shell_Mesh.html ちなみにこのヘルプでも以下のことが書いてありました。 > 固体モデルには、四面体固体要素を使用してメッシュ分割ができます。 > しかし、薄いモデルに固体要素を使用してメッシュ分割すると、要素 > サイズを小さくしなければならないため、非常に多数の要素を作るこ > とになります。サイズの大きい要素を使用することにより、メッシュ > および解析結果の精度の低下をまねきます。板金モデルや薄板モデル > では、シェル要素を選択することが自然であるといえます。また、 > サーフェスモデルは、常にシェル要素でモデル化されます。 「板金」機能を使ってモデリングされていれば自動でシェル要素になるようです。 それ以外のソリッドモデルからは、サーフェスのオフセットコマンドや 中間サーフェスのコマンドを使って中立面を作成すれば良いそうです。 http://help.solidworks.com/2012/Japanese/SolidWorks/cworks/ID_How_to_Model_Shell_Problems.html Solidworksは地元の工業センターで使う程度なのでこれ以上はよく分かりません。 一般的な事はこれが結構参考になるかと思います。 http://monoist.atmarkit.co.jp/mn/kw/fem.html
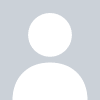
お礼
ご回答いただきありがとうございます。 >ところでSolidworksはSimulation Xpressか何かでしょうか? その場合、扱える要素が限られていたかと思いますので 上記のようには出来ないかも知れません。 そうなるとあとは板厚方向にも十分な分割数となるように ひたすらメッシュサイズを細かくするしか無さそうな気がします。 使っているのはプレミアムに入っているシュミレーションです。 ただ機能はシュミレーションだけに特化したソフトより限られています。 >メッシュサイズを変えて解が大きく変わるなら、 解析精度が十分でないです。 そんな時にはメッシュのサイズを変えながら、解に収束傾向が 見られるまで何度もトライしてみるしか無いでしょう。 メッシュも最大に粗くすればメッシュ自体がかからない、最大に細くすると時間がかかりやすくなって尚且つ結果が正確か怪しいなどということがあります。 数値を変えることでのシュミレーションくらいしかやっていないので、数値は正としてシュミレーションモデルを見直そうと思います。 ご回答いただきありがとうございます。 完全に理解できたかわかりませんが、普通の押しだしや回転などで作るのではなくてサーフェスでモデリングしないといけないということでしょうか? 追記ありがとうございます。 見た目にこだわるあまりに普通のモデリングをしていたのでシェル要素になっていませんでした。 板金でやり直してみようと思います。
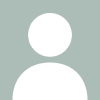
回答(2)さんのお礼にある >検査するものは1.6tで製作された制御盤などの扉で、変位及びたわみを調べようとしています。 からすると制御盤の材質は一般的にはSPCCを使います SPHCの方が鉄板自体の価格は安価ではあるが 黒皮剥ぎ下地処理が増えて塗装工程が高価となって 鉄板の価格差はぶっ飛ぶ <塗装工程は人件費の方が多いので なので SPHCの定数でシミュレーションした結果と SPCCの実測値とで比べているのではなかろうか? 因みに 図面にSPHCと記載してあったとしても板金屋さんはSPCCを使うと思う 分電盤を主要生産してる板金屋さんなら標準在庫してるのはSPCC なので仔細構わずSPCCを使う <塗装してしまったら判別不能 わざわざ塗装を剥ぎ取って黒皮を確認する事など誰もやらないし
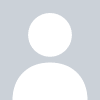
お礼
ご回答いただきありがとうございます。 >因みに 図面にSPHCと記載してあったとしても板金屋さんはSPCCを使うと思う 分電盤を主要生産してる板金屋さんなら標準在庫してるのはSPCC なので仔細構わずSPCCを使う <塗装してしまったら判別不能 わざわざ塗装を剥ぎ取って黒皮を確認する事など誰もやらないし 鋼材検査証明書を資料として受け取っているのですが、そこの規格にJIS G 3131 SPHC (PICKLED)だったり、SPHCとだけの記載があります。もしそうだとしてもSPCC材を使うのでしょうか?
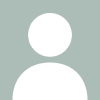
平板のたわみ解析には、微小たわみ理論と大たわみ理論がありその区分けは、 板厚の半分よりたわみが多いかどうかによるのですが、↓URLには、そのことに て書かれているので、貴殿にも興味深いところではないだろうか その中では、誤差が10%以内であれば良好な解析結果と考えているようす 戻ってウラ面補強材の有無で簡略化して考え個々の問題を潰すのが良いかと 「原因だとしても影響は少ないはずで50%は解析の問題では」と私は思います (私自身は、CAEに関してはその環境にも無く素人なので宛になりません)
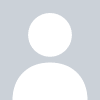
お礼
ご回答いただきありがとうございます。 参考のURLありがとうございます。 こっち方面の知識が乏しいので理解するのに苦労しそうですが、せっかくのご好意を無駄にしないよう参考に出来るよう解いていこうと思います。
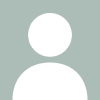
>シュミレーションの結果が、実測値と仮想値が5割程度しか合致しません 前のご質問を参考にすると、SPHC t1.6を使った分電盤の扉のような品物を 水平に置いた場合に、中央部がどの程度沈む(撓む)かを計算したという ことでしょうか。その際、実物では5mm沈んだのに対して、シミュレーション では2.5mmだった。このような数値関係を5割程度の合致と仰っているのでし ょうか。 前置きはこの程度にして、 剛性は板厚の3乗に比例しますから、板厚がシミュレーションに入力した値 の90%としたら、0.9^3=0.729 実際の沈み量は、シミュレーションに比べ 1/0.729=1.37倍程度になるものと予想します。 また、周囲の支持条件をどのようにモデル化するかで、沈み量は大きく変化 するものと想像します。シミュレーションに使ったモデルは、現物の構造を 正しく再現しているでしょうか? ヤング率等の物性値を疑うよりも、上記のような事項を検討なさることを お勧めしたいと思います。
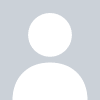
お礼
ご回答ありがとうございます。 >前のご質問を参考にすると、SPHC t1.6を使った分電盤の扉のような品物を 水平に置いた場合に、中央部がどの程度沈む(撓む)かを計算したという ことでしょうか。その際、実物では5mm沈んだのに対して、シミュレーション では2.5mmだった。このような数値関係を5割程度の合致と仰っているのでし ょうか。 ほぼそのとおりなのですが、平均台のような架台に水平に置いたという説明が不足しておりました。申し訳ありません。 合致に関しては仰るとおりの解釈で差し支えありません。 >また、周囲の支持条件をどのようにモデル化するかで、沈み量は大きく変化 するものと想像します。シミュレーションに使ったモデルは、現物の構造を 正しく再現しているでしょうか? ここが今ネックになっている部分なので、もう少しここをつめていこうと思います。
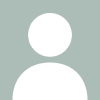
失礼な内容になるかもしれません。容赦ください。 何のためのSPHCの定数の投稿でしょうか。 まず、板厚公差ですが日本では板厚の±10%で、日本製は殆どマイナス公差です。 SPHCの製造メーカーは日本ですか。中国等々でも製造してますよ。 私の知っている限りではSPHCが一番安く、性能等々を要求されない材料と思います。日本ではミルシートを入手しにくい(出来ない)材料です。 ミルシートがほしい場合は15Tons以上の注文で契約しないと入手できないとおもいます。 SPHCでは具合の悪い使用箇所、たとえば板厚精度だけを要求する場合はSPCC、強度を要求する場合、廉価材はSS400、若干コストアップを認めた場合は自動車用鋼板SAPH440(SPH440)等々を使用してます。 要約すると安くてどうでも良い材料がSPHCではないでないでしょうか。 この投稿で得られた内容でメーカーに質問を投げかけたらいかがか。多分期待する答えはないと思います。 宜しく。
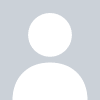
お礼
ご回答いただきありがとうございます。 >失礼な内容になるかもしれません。容赦ください。 何のためのSPHCの定数の投稿でしょうか。 SolidWorksで板金物の強度解析をする際に定数が必要なのですが、その際に材質を入れる項目がありそこにはSPHCの項目がありませんでした。(探しきれてないだけかも知れませんが。) >まず、板厚公差ですが日本では板厚の±10%で、日本製は殆どマイナス公差です。 SPHCの製造メーカーは日本ですか。中国等々でも製造してますよ。 私の知っている限りではSPHCが一番安く、性能等々を要求されない材料と思います。日本ではミルシートを入手しにくい(出来ない)材料です。 違う回答者様のお礼にも書かせていただいたのですが、1.6tで発注したのに1.55tで納品されたということがあったようです。 中身を設計することはできるが、外まで設計できないというのが現状のようです。なので全体的な値段で材質を決定して、外見だけの指示であとは板金屋丸投げになっているんじゃないかと思ってます。(実際には外まで設計できるのかも知れないが、三角法の図面が読めない・製図が雑といったことが見受けられるので到底外まで設計できる人達だと思わない。) ご回答にもあるようにどうでも良い材料にやっきになっているのが現状です。 メーカーになんで1.6tで発注したのに1.55tしかないんだ!とクレームを言っても、逆に無知をさらすだけ・笑われるだけですね。 過去にやっていた原子力関係の仕事では誤差は命取りでしたが・・・。
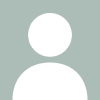
過去の質問内容と、この質問内容から推測しますと、各回答者さんの記載は、全く逆の内容で、 回答しているのではないかと想像します。 さて、過去の質問内容から、 > 現在制御盤や配電盤の扉の構造解析・強度計算をしています。 > H1950 W800 D30 1.6t (材質:AISI1010鋼)の扉で地面に直置きした際に中心部が自重で5mm > 沈んだという結果が出ているのですが、実際にそのくらい沈み込むものなのでしょうか? での確認とします。 そして、 > 定数を入力しシュミレーションして出た結果ですが、実測値と仮想値が5割程度しか > 合致しませんでした。 となっています。 この合致とは、どれ位の許容差までを“合致”と云うのかが明確ではありません。 例えば、 ?のヤング係数の違いは、 鋼材なら特殊なものを除けばヤング率は206kN/mm^2=2.1×10^4kgf/mm^2とみなして良いにて、 206kN/mm^2を使用することが多いですが、211.4kN/mm^2を使用する場合もあるので、約3%位は 許容差と考えて、たわみ量換算したわみ量許容差にする。 ?の板厚1.6mmの違いは、 日本の鉄板製造技術は、優秀なので板厚はマイナス公差管理をして、その大きさの板厚を 作り材料代を浮かせる製造をしまから、板厚1.6mm±0.16mmの下限値でのたわみ量換算し、 たわみ量許容差にする。 ?と?を合わせた位が、最低の許容差となるので、それを大きく離れる値を合致しないと すべきでしょう。 そして、5割が合致していることなので、シュミレーションの結果は、そこそこの結果と考えて、 許容差を重点に置いて再シュミレーションして、たわみ量での許容差を、明確化することが大切 と考えます。 後は、扉の実際の製造方法(仕様)が、シュミレーションに反映されていなく、5割程度しか Goodとならないのでしょう。 特に、実際の溶接の細かな仕様が、シュミレーションに反映されていなく、たわみ量が 異なっていると思います。 実際の溶接ピッチとビード長さや扉コーナー部分の実際の溶接状態がです。 如何でしょうか? 本当に、板厚の差やヤング率の差だけで、合致するしないの差がでているのだろうか? 実際の合致する差の値の明示が無く、想像だけの考えですが、…。
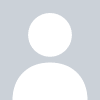
お礼
ご回答いただきありがとうございます。 >過去の質問内容と、この質問内容から推測しますと、各回答者さんの記載は、全く逆の内容で回答しているのではないかと想像します。 毎回質問の趣旨が伝わらなかったり、質問中に二転三転して申し訳ないと思っています。 ここから先は単なる愚痴或いは言い訳として聞き流していただければと思います。 前回と違う材質なのは指示者の失念だったり、具体的な指示も無く作業指示を下したことからきています。じゃあ内容を聞けばいいじゃないかとなりますが、実際に検査しにいった人達の中でも意見が食い違っていたりするので参っています。検査もまだ初期段階なので許せるところもありますが、毎回このような感じならば手をうとうと思います。 駄文失礼しました。 本題に戻って、 >?の板厚1.6mmの違いは、 日本の鉄板製造技術は、優秀なので板厚はマイナス公差管理をして、その大きさの板厚を作り材料代を浮かせる製造をしまから、板厚1.6mm±0.16mmの下限値でのたわみ量換算したわみ量許容差にする。 ということは、1.55tだから不良品であるという判断は間違っているということなのでしょうか?1.6tで発注したのに1.55tで納品されたから、次の発注からは1.6t以上という注記を加えて発注するという案があるようです。 であるならば1.6t以上で発注する案は大して効果がないし、業者もめんどくさがるのかなと思ったりします。 >後は、扉の実際の製造方法(仕様)が、シュミレーションに反映されていなく、5割程度しかGoodとならないのでしょう。 再三申し上げているのですが、板金業者の技術的な問題やシュミレーション自体の問題があるようです。 仮に仕様が全てもりこめるシュミレーションを使って解析しても、それを取引業者クリアできるのかはわかりません。 試作→実物製作→検査→納品の流れを、シュミレーションを使って試作をしないことで試作をやめたいというのが狙いのようです。 今シュミレーションで入力をしている数値を私の質問に追記しますので、お時間ございましたらご確認お願いいたします。
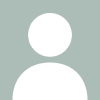
ヤング率は焼入鋼でも同値で通用する程なので変わりようがないです。 板厚はその通り。規格値±0.16であってもマイナス目が常識になってます。 JIS G3131 から引張強さが28kg/m? 長期許容応力度はその1/2。シュミレーションでは不問。 短期許容応力度は長期の1.5倍 → 引張強さの0.75倍。これを降伏点または耐力とする。 規格値は下限なので鋼材検査証明書から引いた値でよいと思います。 シミュレーション結果と実測値との比較、、 この厚さのものを壊すにはかなりな試験なのと、応力限界は簡易な装置では見にくいので、それより低い時のタワミ量についての比較でしょうか? それはシミュレーションテクニックの問題と思います(知識薄し) 回答(1)さんの追記は興味津々 実物の結果にシミュレーションを合致させるよう、テクを凝らすのが実際だと思います。時には設計便覧の図表引き筆算と対比したりして このような薄板のたわみ計算では数値計算での誤差問題が目立ってきます。メッシュが細かいほど誤差累積します。
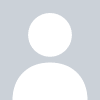
お礼
ご回答ありがとうございます。 弾性係数を半分の数値にすると近似値になったので、弾性係数が原因なのかと思っていました。 弾性係数が原因ではないとなるとシュミレーションのテクニックの問題なのだと思います。 検査するものは1.6tで製作された制御盤などの扉で、変位及びたわみを調べようとしています。 ご回答ありがとうございます。 >このような薄板のたわみ計算では数値計算での誤差問題が目立ってきます。メッシュが細かいほど誤差累積します。 技術的な問題もからんでいるようなので、きっといつまでたっても実測値・手計算値・仮想値が近づくことはないでしょう。 メッシュも最小にしないとメッシュがかからないので、そこも要因のひとつなのだと理解できました。
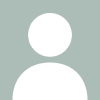
直接の回答でなくて申し訳ありません。 シミュレーションの結果に異常があるとのことですので、 その点についてのアドバイスをさせていただきます。 1.6tの構造物についての解析だとメッシュサイズが 不適正である可能性が高いと思われます。 (すでに検討済みかもしれませんが) 一般的に薄板の解析であれば最小板厚の5倍程度を目安に 平均要素サイズを変更必要があるようです。 (今回の場合でば8mmですね) PCの性能によってメッシュが細かすぎるとメモリが不足し 解析できないこともありますので調整が必要です。 No.40838 箱形状の強度計算? http://mori.nc-net.or.jp/EokpControl?&tid=280796&event=QE0004 こちらの質問に対して私がつけた回答で3.2tの箱を解析しております。 初期状態のメッシュで出た解析結果と、メッシュサイズを調整して 出た解析結果で大きな違いが発生しております。 >SolidWorksは薄板のシュミレーションはあまり得意ではないと捉えて >いいのでしょうか? 有限要素解析自体が薄物の解析が得意でないと認識しております。 また曲面もメッシュを切るときに不安定になりやすいのでできるだけ 曲面の少ない簡略形モデルにて解析をしたほうが実際の結果に近い 状態になることも多いです。 形状は類似形状であれば変位量は、ほぼ同じ結果が得られます。 Rをつけないモデルを使用するのはメッシュの量を減らすテクニック でもあります。 減らせれる分メッシュを細かくして、より詳細な結果を得ることが 可能となります。 私がシミュレーションのやり方で検討しているのは、拘束のつけ方、 荷重のかけ方、メッシュサイズの3点です。 >レンガのような直方体で中身が詰まっているものには有効であるが >、ティッシュの箱みたいな薄い直方体は役に立たないということですね。 全体の大きさに対する板厚が極めて小さい場合は解析が困難と思って 間違い無いです。 その際はいかに近似値の得られるモデルにするかがノウハウになって くるかと思います。 おっとついでにアドバイスを・・・ 参考に上げた質問のように扉の正面の板と補強板だけのモデルにして 正面の板の4辺固定で解析するなど少しでもメッシュの量を減らすと 解析できると思います。 私の実績ではW=2mxL=3mxH=1m程度の角パイプ構造の架台の解析 を行ってそれなりの結果を出したことはあります。 1日がかりの仕事でしたが・・・
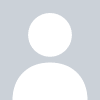
お礼
ご回答いただきありがとうございます。 >1.6tの構造物についての解析だとメッシュサイズが 不適正である可能性が高いと思われます。 (すでに検討済みかもしれませんが) メッシュをかけることが出来て解析できたとしても、出来上がったメッシュが不適正なら結果が違ってくるということでしょうか? SolidWorksは薄板のシュミレーションはあまり得意ではないと捉えていいのでしょうか? シュミレーション自体まだまだはじめたばかりなので、解析結果がでればそれでいいかなという感じになってしまっています。 詳細なご回答ありがとうございます。 度々ここで質問しているのですが、制御盤の扉(1.6t)に補強(1.6t_コの字型)を加えた状態での変位・たわみを測定しようとしています。 sqninさんの回答の中でモノコック構造という言葉が出てきましたが、今解析しようとしているものはまさにそのような形状であると思います。 全体を通してみると問題点は数値的には検査できる情報がそろってはいるものの、シュミレーションするモデル形状ややり方で結果がまったく違っているということでよろしいでしょうか? 今のモデルは現物から見た目が離れないようにRを掛けていたりしているので、検査モデルと現物は別物と考えたほうがいいですね。 >>有限要素解析自体が薄物の解析が得意でないと認識しております。 レンガのような直方体で中身が詰まっているものには有効であるが、ティッシュの箱みたいな薄い直方体は役に立たないということですね。 ご回答いただきありがとうございます。 >私がシミュレーションのやり方で検討しているのは、拘束のつけ方、 荷重のかけ方、メッシュサイズの3点です。 シュミレーションで悩むところはそこですね。漠然とした資料しか出してこないので、どの場所を固定してどこに荷重をかけるとかに悩んでます。 >参考に上げた質問のように扉の正面の板と補強板だけのモデルにして 正面の板の4辺固定で解析するなど少しでもメッシュの量を減らすと 解析できると思います。 ビジュアル的に見せないとピンとこない人が多いようなので本来の形状にこだわっていましたが、今からは必要なのは結果なのでちゃんとした結果が出せるモデルにこだわってみようと思います。 >私の実績ではW=2mxL=3mxH=1m程度の角パイプ構造の架台の解析 を行ってそれなりの結果を出したことはあります。 1日がかりの仕事でしたが・・・ 今の解析作業もそうですが形状が単純なのに結果がよくないので試行錯誤しているのですが、周りから見ればいつも同じ絵をいじって同じ結果なんでは?と見られているんじゃないかと思ったりします。そこが3Dのつらいところなのです・・・。
お礼
ご回答いただきありがとうございます。 >リアル(と思われる)3Dモデルを作って、時間をかけて解析するのは ナンセンスだと思います。 現実と同じモデルなんて絶対に作れません。 いろいろ条件を変えてシュミレーションしていますが、溶接コマンドがあっても溶接は特に考慮されないようですし、板金化したからといって硬さが取れるといったこともあまりないようなので今していることはあまり意義がないものだと思うようになってきました。 薄板の解析に向いていない手法で解析しているのも変な話ですし、現物も作り手によってばらばらであるならばシュミレーションを出す意味もなくなってしまいます。 >求められているのはたわみを減らす方法ではないですか? 現状の解析は早く終わらせて改善案の解析を進めるべきでは? 今の作業にこだわることはやめて、補強無しの状態からどのような補強を入れればたわみが収まるのかというアプローチに変えようと思います。 結局はたわむものですし、3D上で数値が半分になれば効果ありだと思います。 納品先がどのような過程・結果を求めているのかわかりませんが、実使用で強度が保たれるのであればそれで問題ないと思ってます。扉ばかりに強度を求めてしまったら、他の質問でも出てきましたがヒンジ部にも補強をいれないといけない状況になると思います。 3D上でのベストと実物のベストに差は出てくるはずなので、その辺を担当者判断にしていただこうと思います。