- 締切済み
切屑を小さくする方法とは?
- マシニングセンタを使って穴加工をしている際に切屑が交差してしまった場合、手作業で取るのは困難です。そこで、切屑を小さくして排出する方法を考えましょう。
- 切屑を小さくするためには、ドリルの送りや回転数を適切に調整する必要があります。具体的な調整方法については詳しく解説します。
- 送り(F)を遅くすることで、切削する時間を長くすることができます。その結果、切屑のサイズを小さくすることができます。回転数(S)はそのままにすることで、効率的な加工を行うことができます。
- みんなの回答 (6)
- 専門家の回答
みんなの回答
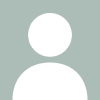
数ヶ月の新人、ということで、なかなか詳しい情報もわからないのが現状と思いますので、文面より簡単なアドバイスをしますね。 ⇒切り屑がつまった 穴径よりも大きな切粉が出た。切粉が重なり合った、または、穴が互い違いの部分で細長い切粉が出、それがつまった、といった所でしょうか。手作業で取るのは大変との事ですので、穴径が細いのでしょう。 分断されて詰まってるのならサイクル等は入っているのでしょう。 ということは、切粉を小さくすれば良いので、より小さく分断をさせる、抜け際の当たりで片刃切削をなるべくさせない、主穴より、副穴を先行して加工する等、刃先の形状(シンニング)の考慮等を考える、条件を調整する、などの結論に至ります。 また、それぞれにはまた課題もありますが。 単品モノで時間があるのなら、機外作業や機内でもう一度同じ穴へ互いのドリルを通しても良いでしょうね。送りは速めにして。ガンドリル穴だったらしないほうが無難です。 その場合は刃部が擦れてキズや磨耗する可能性はありますが、どうしても詰まる、という会社ではそうしていました。ただ、時間を気にするのであれば下記回答者様の回答にあるように色々考えなくてはいけません。 かけだしの方ですから、これから直面する課題は自分の糧となってくると思います。頑張ってください。
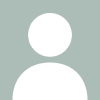
回答(1)(2)(3)(4)すべて正鵠を射ています。 何と言っても、 ・ワーク材質 ・ドリル材質(ハイスor超硬)、 ・両方の穴径 ・後から加工する穴の深さ ・穴の中心を交差するか否か ・加工方法(ステップ/ノンステップ、外部/内部給油) を明示して下さらないと、何とも回答できません。 とは言っても、様々な事例のすべてに対し回答することも不可能ですので アプローチについてヒントを申し上げます。 ・交差穴部の食いつき時は送りを下げる→穴精度維持、ドリル折損防止 ・食いついたら送りを上げる→切りくずを細かくする ・ワーク材質に適した超硬ドリルを用いる→適性な切りくずに分断 ・内部給油が可能であれば超硬ドリルでノンステップで加工 ・ 〃 が不可能でも切りくず排出性に優れた超硬ドリルで 交差穴より先はできるだけQを大きくする (ステップ動作回数を減らしドリル自身の能力により切り屑を排出) 最終的には試行錯誤の上、各々のケースに応じた最適な工具と切削条件 を選定することが、切削加工エンジニアである質問者さんのノウハウに なりますので、頑張ってください。
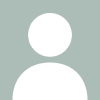
回答(2)にあるようにQを小さくすると細切れにはなります。 しかし細切れは改善な場合もあるが万全ではなく根絶は無理かも。逆に交差穴へ流れ込みやすくもなる。 交差穴も等径、直交、食違い無から、異径、食違いあり、角度、、と難易度は様々。 http://www.tungaloy.co.jp/ttj/products/pdf/solid_drill_manual.pdf P.66 交差穴の加工 その前後頁のイレギュラーな穴加工への対処法も役立つ
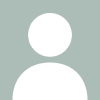
昔、エンジンのシリンダブロックの“冷却水”や“潤滑油”用の小さく長い穴を明ける 試作工程で苦労をした事を思い出します。 繊維機械メーカーの方に、大変お世話になったことも、思い出します。 それで、まだまだ飯が喰える位のニッチジャンルです。 確か、公差している付近は、送りも工夫が必要だったと、記憶があります。
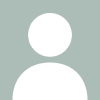
固定サイクルぐらい書けと http://nc-program.s-projects.net/fixed-cycle.html Qを小さくする >>なんとなく送り(F)を遅くし回転数(S)はそのままで 薄く長くなる
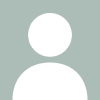
とりあえず加工材料と加工寸法 工具の種類くらいは記載すべきなのでは? 全てのケースについて 回答者さんに個別に答えて貰おうというお気持ちなのでしょうか?