- ベストアンサー
POM変形時の円盤加工方法についての専門家の意見
- POM変形時における円盤加工での材料の反りをなくす方法について、専門家の意見を求めています。
- 円盤形状のギーアの加工において、直径40cm、厚み8mmの円盤の平面度の変形を0.3mm以内にする方法について専門家のアドバイスを探しています。
- POM変形時における円盤加工での材料の反りをなくす方法について、専門家のご意見をお教えください。円盤の形状は直径40cm、厚み8mmで、平面度の変形は0.3mm以内にする必要があります。
- みんなの回答 (3)
- 専門家の回答
質問者が選んだベストアンサー
- ベストアンサー
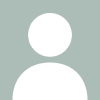
精密な加工で精度を維持するには、多様で細かなノウハウが必要です。 a)先ずは、アニール処理です。 URLで示す内容や“樹脂加工 アニール”で検索しますと、色々確認できます。 “POM アニール”でもかな。 b)POM材の材料選定です。 例えば、POMの端材と中央に近い芯材とでは、同じ加工をしても反りが異なります。 端材は反りが大きい、芯材は反りが小さい傾向にあります。 ですから、選択が可能であれば芯材に近い方を選択する。 等々ですかね。
その他の回答 (2)
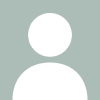
変形の要因を特定する必要があると思います。材料そのものの異方性が原因か 材料支持による力によるのか、熱変形なのかなど。原因によって対処方法が異 なると思います。ギヤということなので、フライスやホブ盤加工でしょうか? 必ず同じように変形が出るのであれば、材料支持の方法で改善できるのでは ないでしょうか。提示の程度の変形ならアニール処理で是正できるかもしれま せんが。
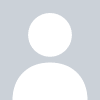
お礼
回答有難うございました。
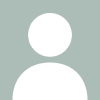
サイズそのほか抜けている事柄が多いから、答えもヘンな当てずっぽうになってしまっている。追記をしてください。 円盤の大きさが10、100、1000のどれに近いか? 素材は板なのか丸棒から削るのか? 板なら厚さは1ミリなのか10ミリなのか100ミリなのか? それにおおよそどのような加工をしたいのか? 反りは何ミリ以下にしたいのか? あなたは目の前に素材があり、以上の ? について当然知っているが、他の人はこの質問を見ても判りません。 極端な話、厚さ1大きさ1000で反り1以下にしたいと望んでも、方法は無し。 >円盤形状のギーア、サイズは直径40cm、厚み8mm、平面度の変形は0.3mm以内に ギアの形状はホブ盤でやるとして、歯形状については柔軟性あるPOMなのでうるさくは言わないハズ。 ギアの用途から、直径40cmの全面に平面度が必要なことはなく、歯部とボスの周りだけの平面度だけで充分なはず(ホブ切りで重ねるために平面と平行が必要?) つまり中間部は0.5~1ぐらい荒取りして凹ませてしまい、残る凸部分を仕上げ削りする。 そうすると材料を削っただけで顕れる反りがほぼ無くなり更に精度を上げることも出来る。 削る工具はひたすら鋭いこと。 ダイヤモンドが最上で次いでハイス。超硬は鋼用として強度が必要なためわざと鈍らせており適さない。 削るときの固定方法も重要。ここで反りを作り出してしまうことも起こりえる。ボス部分を金属で固定するのが基本でしょう。
お礼
早速回答いただいて本当に感謝いたしました、続いて活躍よう心から祈っています!