- ベストアンサー
※ ChatGPTを利用し、要約された質問です(原文:φ2ピアス加工)
φ2ピアス加工の留意点とアドバイス
このQ&Aのポイント
- 板材SUS、t=0.5 幅5mm及びSS400相当材t=1.5~2 幅約4mmにφ2~2.2のピアス加工を予定してます。この加工をする際の留意点をアドバイスお願いできませんか。
- パンチ材質、長さ、パンチの固定方法、ストリッパーとのクリアランス、ダイ材質、厚み、熱処理硬度、クリアランス、プレス加工時の回転速度など、φ2ピアス加工の際に留意するべきポイントは多々あります。
- φ3のピアスはt=0.1,0.2,0.5で実績済みですが、厚さが厚い場合にはパンチ先端が振れる可能性があります。ピアス穴の表面状態も不均一になることがあります。
- みんなの回答 (1)
- 専門家の回答
質問者が選んだベストアンサー
- ベストアンサー
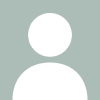
noname#230359
回答No.1
SUS304(仮) 板厚=2mm φ2.2穴であれば特に難しい加工では無いと思います。 弊社では時計バンド自動組付け金型で板厚より細い穴及びスリット加工は普通に問題無く行っています。 経験上パンチが折れる原因数例書きます。 1、プレスの回転数が低い 2、プレスの精度が良くない(出来れば口開きするC型以外のプレスが望ましい) 3、プレスのパワ-不足 4、金型の構造(ダイセットとガイドの精度)が良くない 5、金型の磨耗及びカス詰まりによるパンチへの負荷が増す 6、金型の精度が悪い為にパンチが振れて、偏荷重でパンチが折れる 形状がシンプルなのでパンチとダイは市販の規格品の方がコスト的にも、 サイズ変更作業も楽だと思います。 生産量は不明ですが、 例:パンチ(ミスミ) 材質V30(HIP)超鋼 硬度88~89HRA ダイ(ミスミ)カス上がり対策付 材質V40(HIP)超鋼 硬度87~88HRA 上記の板厚とパンチ径の条件に対して ストリッパ-のクリアランス: 0.01mm~0.015 ダイのクリアランス: 0.16mm(8%/t) プレスの回転速度は速い方が良いですが、現実問題としてこの製品用に高価な高速プレス(2000SPM以上)を購入するのは難しいと思いますので、貴社にある比較的精度が良く、高回転プレスに変えれ良いと思います。 ダイセットと金型のガイド精度と金型精度を上げる。 参考までに、宜しくお願い致します。
- 参考URL:
- http://fac9999.web.fc2.com/
お礼
具体的な回答有難うございました。ほぼ受注が決まっている加工ですので非常に助かります。 甘えるわけでは有りませんが、今後ともに助言のほどお願いします。