- 締切済み
M00を減らして連続運転時間を延ばす方法とは?
- マシニングを使った部品加工でM00が多用されていることに悩んでいます。
- M00の使用理由として、タップやリーマ加工後の切粉除去や公差測定、押さえ換えが挙げられます。
- M00を減らして連続運転時間を延ばす方法を探しています。
- みんなの回答 (3)
- 専門家の回答
みんなの回答
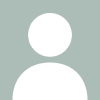
私の場合、CAD CAMから段取り、加工まで全て一人で行なっていますので 割合、その都度工程順序を変更したり、切削条件を見直したりという 事が出来ますが、オペレーターの方がプログラムを受け取り、 実行するだけという場合は、必然的にそうなると思います。 改善策としては回答(1)(2)で大方述べられているので、 敢えて付け加える事はありませんが、 私のプログラムではM00は用いずM01を工具交換毎に入れています。 そして加工機の方はオプショナルストップスイッチを 基本的にONにしておいて、連続で加工できる間を見切る事が 出来る場合のみOFFにします。 加工の内容によっては歪み等の事も有り、リーマー等は 下穴→リーマーへと一気に行きたい場合もありますし、 傾斜面にタップやリーマーを加工するという場合もあるでしょうから、 その点はオペレーターの方と打ち合わせを時事される事が 望ましいかと思います。 その中で「何が余分な作業工程か」「何処を短縮出来るか」等、 これはオペレーターのスキルのレベルも充分に関与してくる問題ですので その話し合いの中から、お互いのレベルアップを目指して、 一つ一つ確実にクリアーして行けば良いのではないでしょうか。 回答にはなっていませんが、私の所感としてお伝え致したく、 申し上げます。 追記:「文字変換ソフト」の件で、申し訳ありませんが、 再度、アドレスを送信して頂くか、掲示板の方で、アドレス欄に 記入して頂けると幸いです。
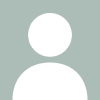
オペレータとしてはとめたいタイミングです M00 でなくてM01 にする、(気休めですが) あとは、回答1と同等です 2は、一度加工したら、飛ばせる項目です 3は、治具を工夫する 1は、タップ折れやリーマー折れが心配なのでとめるわけですが 工程の一番最後にすべてまとめれば、一回の確認ですみます
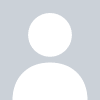
お礼
ご回答ありがとうございます。
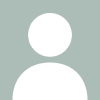
?タップやリーマ加工の下穴を開けたあと、切粉を除去するため。 1.下穴はオイルホールドリルで加工する=>中からクーラントが吹き出すので残らない 2.もしくは下穴加工後再度クーラントを出して各穴を掃除してまわる=>勿論プログラムで 3.オイルホール設備が無い場合=>4.へ ?リーマ加工後、公差通り仕上がっているか測定するため。 4.出来るだけ停めて人が介入するところはまとめ 一度で済ませる 加工の最後か最初 ?切削した場所をクランプしているので、押さえ換えを行なうため。 5.ソリッドバイスなどを利用し押さえ変えをしなくて良いようにする
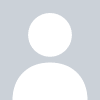
お礼
ご回答ありがとうございます。 やはり工夫の仕方はあるものですね。
お礼
ご回答ありがとうございます。 前回のご回答が消えてしまっていたので連絡することができず、途方に暮れておりました。