- 締切済み
フィードバック方式(位置決め)について
- 加工機の位置決めには、エンコーダ・スケールが用いられています。
- スケール方式は、バックラッシュによる誤差を小さくするためには良い選択肢です。
- スケール方式での位置決めの設定・順序については、詳細が不明です。
- みんなの回答 (2)
- 専門家の回答
みんなの回答
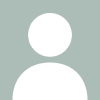
機械の位置決めというのは 標準的な機械であればサーボモータに内蔵されているパルスコーダからの情報で行っています。従って実際の加工物や工具のの位置というのは サーボとメカの結合の状態によっては バックラッシュや減速機やボールネジの精度やピッチ誤差 熱による金属膨張(熱変位)により 必ず誤差を生じます。そこでNC装置にはピッチ誤差補正やバックラッシュ補正、熱変位補正といった機能を持たせて 出来る限り誤差を無くす機能が備わっています。しかし これらの機能をもってしても温度変化、経年変化には対応しきれないものです。そこで位置決め精度が必要な部分(加工物や工具のすぐ近く)に 別置型のスケールを取り付け 実際の位置情報をスケールで読み取るという手法を取り入れる場合があります。これによりバックラッシュやピッチ誤差の影響がかなり少なくなります。もちろんスケールを付けたからといって 誤差がゼロになるわけではないので機械メーカでは調整は行います。 スケールを搭載するかどうかは、エンドユーザーの希望によるところが大きいですが 傾向としては精度の必要な軸と回転軸には 大体採用されるようです。特に回転軸は テーブルの径が大きくなると外周付近での角度誤差が大きくなるのでロータリースケールを搭載するケースが多いです。 取り付ける場所としては 直線軸はボールネジ等の駆動部付近、回転軸は回転中心です。できるだけ位置決め精度の必要な所の近くに取り付けるのが理想ですが クーラントや潤滑油、切粉や埃の影響を受けない所を選定します。
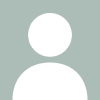
一般論(特殊な機械では異なるかもしれません)としてサーボ系はサーボモーターの回転軸の回転角や速度などを検出してます。ですから信号としてはあくまで回転角度でありその先ギヤやボール螺子のことはしらんぷりです。ですから制御機にはピッチ誤差補正やバックラッシュ補正などがあります。そこでさらに精度を上げるべくスケールフィードバックが付けられました。一般にマグネスケールやフタバやハイデンハイのガラススケールなどが使われますがこれらはテーブルの材質と同じ熱膨張率に調整されて、テーブルなどに付けられテーブルの移動正味が計測されてサーボ回路に返されます。スケールの構造は各社自社が一番と言ってますが基本的に差はないと思います。媒体がガラスか鉄線かの違いぐらいですから、 ガラスのほうがエッチングで精度が出るようにいわれますが光学露光の精度がききますよね。鉄線はレザー測長器の信号から書き込み信号を作ってるのでHPの精度と同じといいますが?でも案外制御機のソフトがききます。 単純な位置帰還だと収束が遅いとか振動して収束が遅いとか、職人が汎用機でハンドルで追い込むときの操作を真似るとか、いろいろ工夫してます。 基本的には普通のプラスチックの物差しのようにガラス板に目盛り線が書かれてるのを光センサで数えるので電源オンからの積算しか計測できません。原理的には。 でも各社色々工夫をしてます。 光も単に透過光を測るだけではなくモアレを使うとか。 アブソリュートデータを書き込むとか。
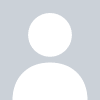
補足
お礼が遅くなってしまいまして、申し訳ありません。ガラスを使用する場合は、ガラスに光りを当て反射光を読み取ったりしているのでしょうか? ガラスに対してテーブルにつけている読み取り装置は、どのようにして自分の位置、動き量を測定しているのでしょうか? もし、分かりましたらご教授お願い致します。
補足
お礼が遅くなってしまいまして、申し訳ありません。ガラスを使用する場合は、ガラスに光りを当て反射光を読み取ったりしているのでしょうか? ガラスに対してテーブルにつけている読み取り装置は、どのようにして自分の位置、動き量を測定しているのでしょうか? もし、分かりましたらご教授お願い致します。