- 締切済み
※ ChatGPTを利用し、要約された質問です(原文:超硬部品の割れについて)
超硬部品が割れる原因とは?
このQ&Aのポイント
- 超硬を用いた部品がクラック入りして割れてしまった場合、疲労破壊以外の原因が考えられます。
- 加工上の問題はなさそうであり、クラックの入った場所が繰り返し応力を受ける部分であったことから、他の原因が疑われます。
- 超硬は金属材料とは異なりますが、それでも疲労する可能性があるため、原因を特定するためには詳細な検証が必要です。
- みんなの回答 (2)
- 専門家の回答
みんなの回答
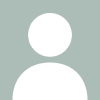
noname#230359
回答No.2
ほとんど、回答1に書かれているようですが あと熱衝撃にも弱いです ガラスを暖めて 急に冷やしたときに割れると同じ現象 急冷時にたとえ、持ったとしても表面の応力が引っ張り方向だと 時間がたつと割れてきます 高硬度のものは、耐摩耗性が高いですが曲げにはめっきり弱い (有る程度の力までは、生材よりも強いが、一気に折れるので) 繰り返し応力のかかるようなところでは、 一瞬超えた場合でも、ひびが入ります
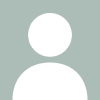
noname#230359
回答No.1
部品形状が不明のため、一般的な回答しかできませんが 超硬合金は焼結金属で、何らかの微細なクラックが発生すると、容易に破壊します。形状的な要因では、内角部、段差部が小さいRになっていると小さい外部応力で簡単にクラックが発生します。加工方法では放電加工による微細な放電痕、研削加工時の研削痕、研削方向と応力の方向の関係等がクラックの要因になります。 超硬合金は鋼に比べ曲げ強度は大ですが、伸びは少ないので、クラックが発生し易く、破損し易いです。