- 締切済み
※ ChatGPTを利用し、要約された質問です(原文:鋳物の焼なまし)
鋳物の焼なましで硬度を下げる方法と機械的性質について
このQ&Aのポイント
- FCD450で手配した部品の硬度がFCD600となってしまった場合、鋳物の焼なましによって硬度を下げることは可能でしょうか?焼なまし以外の方法もありますか?
- 焼なましによって鋳物の部品の硬度を下げることは可能ですか?FCD450で手配した部品がFCD600の硬さで納入されてしまったため、再手配する時間がない場合にどうにかして硬度を下げたいと考えています。
- 鋳物の焼なましによって部品の硬度を下げる方法はありますか?FCD450で手配した部品の硬度がFCD600になってしまったため、再手配する時間がない場合に焼なましを利用して硬度を下げたいと思っています。焼なまし以外の方法もあれば教えてください。
- みんなの回答 (1)
- 専門家の回答
みんなの回答
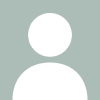
noname#230359
回答No.1
ご希望のお答えに沿いかねるのですが、硬さの数値はお分かりでないでしょうか。材質は間違いなくFCDでしょうか?また、FCD600材として納入されたものでしょうか。先ず、ここを明確にしないことには始まりません。 FCD600材として納入されてしまった場合は、そのまま流用することの許可を関係機関に提案することです。機械的性質はFCD450とFCD600では雲泥の差がありますが、450の代替に600を利用することはコスト以外にはデメリットはありません。 次期手配部品よりFCD450を利用することを条件に一時的にFCD600を生かす申請をするべきです。(独断で流用はしてはいけません) FCD600でない場合は作り直すことです。FCD450材は強度面でシビアな個所に利用されるため、焼きなましで硬度を下げての利用は、より大きな信用の失墜につながるし、事故が生じた場合、想像もつかない程の経済的損失を被ることをご承知ください。 (人身事故の補償とかに繋がります)