- 締切済み
MCでA2017Sにφ1.5x51Lの深穴加工や
- 初めての投稿になります。
- マシニングセンタにてA2017角物にφ1.5x51Lのエア穴を開けようと思っているのですが、内部給油が無いせいか30Lを越えた辺りでカス詰まりによる折損に悩んでいます。
- 現状はNACHIのDLCPLSDで試行錯誤していますが、何かお勧めの工具があればご教授下さい。宜しくお願いします。
- みんなの回答 (4)
- 専門家の回答
みんなの回答
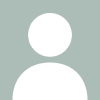
ソディックの細穴加工機 http://www.sodick.co.jp/product/tool/drilling/k1c.html じゃないと無理な加工だと思います トンボで加工するか 30以降付きっきりで キリコの処理&切り込みを減らしてください
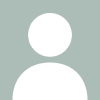
素人のタワゴトです。 エア穴あって剛体を通す訳ではないんですよね? トンネルを掘るように表裏から27Lずつ穴あけしてはダメでしょうか 30Lまで実績あるならできそうに思うのですが 0.1~0,2mm位のアライメントズレなら3mmオーバーラップすれば 余程の流速でなければ圧力損失は無視できるとは思います。 もしかするとカス残りを確実に排出するために ブラシ貫通工程が追加で必要になるかも知れません。
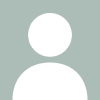
φ1.5の穴径は変更できないと思いますが、設計的にφ1.5を保ったままで 51Lが必須でしょうか? 例えば、内面に接する側をφ1.5x10Lとして、その外側をφ3程度で逃がす ことが可能であれば、加工の難易度を大幅に低減できそうに思います。
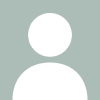
2000番系ですか、軟らかくて切りくずが溶着しやすいのかもしれません 工具としては現在ご使用のドリルはDLCコーティングが施されており 最高の選択だと思われます 加工のポイント ・3-5mm深さの下穴をシッカリあける ・ドリルの振れをできるだけ小さくする(0.03以内) ・3mmぐらいのステップで加工、ステップごとにドリルを穴の入り口の 際まで引き上げる(R点をマイナスにして穴から出さない) ・クーラントは切りくずの排出を妨げないようにノズルを絞って適度な 吐出量にする カタログの推奨条件は、20,000min-1、0.035mm/revぐらいですが、現在の 加工条件は如何ほどでしょうか 回転速度や送り速度が遅すぎると切りくずが溶着しやすくなり、速すぎる と切りくずが詰まります
補足
情報不足で申し訳ありません。 板厚89で表から52mmのところにφ6.0の横穴が通っているのです。 つまり表からφ1.5x51L、裏からφ1.5x38Lの加工を考えていました。 なのでトンボ加工の片側が51mm必要なんです。 ただし、はははさんの「ソディックの細穴」っていうアドバイスのおかげで、 ウチの会社に有る西部電機のワイヤー付属の「穴開け太郎」がφ1.0だったのを思い出して、客先の了解を貰って無事に納めることが出来ました。 大変助かりました。 ありがとうございました。