- 締切済み
※ ChatGPTを利用し、要約された質問です(原文:マザトロールの バー材段取りのしかたについて)
マザトロールのバー材段取り方法について
このQ&Aのポイント
- マザトロール(90年前半製)タレット型NC旋盤のバー材の段取り方法について質問です。
- 現在はバー材をチャックから突っ込んで加工しておりますが、他の方法があるのでしょうか?
- マザトロール(EIAなし)対話ではツール旋回位置か原点しか選べなかったので、手法をご存知の方がいらっしゃれば教えていただきたいです。
- みんなの回答 (1)
- 専門家の回答
みんなの回答
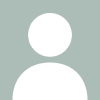
noname#230359
回答No.1
sinobiさんこんにちは。 バー材をタレット側に取り付けた丸棒で位置決めするのは、ウチでもよく使う手法です。 ですが、ウチのマザトロール機は中実チャックのみなので、マザトロール機ではやったことがありません。 もしやるならSGL単動プロセスを使います。 PNo. モード ギヤ 工具 1 SGL 8 SEQ G データ1 データ2 データ3 半径R/増減量 回転 送り M 補正 1 0 X0. Z1. 9 2 0(←ここで材料を引き出す。そしてスタートボタン) 3 0 Z10. 8 このようなプロセスを最初に置いておいて、MOで停止中にバー材を引き出します。 プログラムエンドは、“連続”にしておきます。 呼び出す工具には、回転指令を入れないでおきます。 ああっ! やはり、予想通りスペースの位置がムチャクチャで、わけわからん説明になってしまいました。 早い話が、SGLモードでバー材を当てる工具を呼び出して、SEQ1で希望の位置まで近づける。 SEQ2にM0を入れて、停止している間にバー材を引き出して、CYCLESTARTボタンを押す。 SEQ3でちょっと離す。 ということをするのです。 もしSGL機能が付いてないとしたら、ごめんなさい。
お礼
jiroさん ご親切な説明をありがとうございました。SGLタンドウは当方のマシンにもついております。マザトロールt-32です。 しかし・・・ですね シーケンス1で希望の位置まで近づけ シーケンス2でM0(これはわかります)シーケンス3でちょこっと 離す・・・ってのも 恐れ入りますがご教授ついでに具体例でちょっと教えていただけないでしょうか と申しますのも 当方ではタンドウは一度も使ったことがないのであります。ですから タンドウってどんな風に使えばいいのかさえ わからないんです(汗) 例えばチャックの爪先端から 100ミリ 40φの棒をだしたところで 位置決めするってことで。 加工は 端面を0.5ミリ削ったところをZ0になるように 位置決めのところに0.5ミリ端面をでっぱるような設定ってことで あとは外形を加工して突っ切るってプロセスで・・・ お忙しいところ恐縮ですが 教えていただけますか 先ほどの回答のところは今 プリントいたしました。 しのび