- 締切済み
切削速度のポイントと目安、難削材の加工方法について
- 自動盤での切削加工において、切削速度や主軸回転数、送り速度の決め方について教えてください。
- 特に材質や材料径に対する切削速度や送り速度の目安の決め方について詳しく知りたいです。
- また、難削材を加工する場合の初めの切削速度やバイトの選定についてもアドバイスをいただきたいです。
- みんなの回答 (5)
- 専門家の回答
みんなの回答
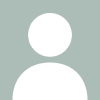
経験の無い材料を加工する場合の周速の設定は刃物メーカーの推奨範囲の真ん中からスタートします。 推奨範囲の真ん中であれば大きく外さないだろうとの考えからです。
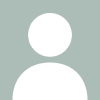
数値の件、今お持ちの機械は主軸移動型のため給材機との兼ね合いがあります、現状の材料は難削材で加工中に表面効果が発生するので周速を下げております。 素材径の件、φ2.5?は周速は40mで、φ16?は 周速は20m30mが良いでしょう。 切削条件としてはあまり動かさず、まずは良品を作ることが先決です。
- 参考URL:
- http://www.grandroyal.co.jp
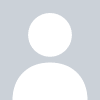
お礼
度々の質問に対する回答を頂き本当にありがとうございました。 材質、素材径によって周速を決めるのはなかなか難しいですね。これからは実績をデータとして残していき、よりよい切削条件を探していきます。また何かあった時はよろしくお願いします。 ありがとうございました。
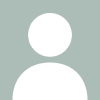
とりあえずそのスピードで加工始めて下さい。 ただし境界摩耗、逃げ面摩耗、等刃先の観察をしてデーターを蓄積する必要があります。
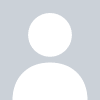
お礼
何回も教えて頂きありがとうございます。 大変恐縮しています。 私は素人なのでよく解らないのですがV50m/minはどのようにして出てきた数値なのですか?経験でしょうか?経験の無い材料を加工する場合の周速の設定方法のコツがあれば教えていただけませんか?何回も質問して大変申し訳有りませんがよろしかったら教えて下さい。よろしくお願いします。
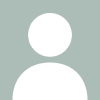
まずは、被削材に対して超硬ロウ付バイトの選択が必要です。 自動盤(一次加工機)は毎回転送りの為、被削材の径に合わせて回転数と送りを設定します。 質問のSUS316及びSUS420J2は難削材とされております。 超硬材質によりますが一般的に周速は20m70mを薦めております。 初めて加工するのでしたら周速は40mから行ってください。
- 参考URL:
- http://www.grandroyal.co.jp
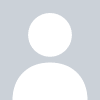
お礼
アドバイスありがとうございます。 よろしければ教えてください。 >超硬材質によりますが一般的に周速は20m70mを薦めております。 >初めて加工するのでしたら周速は40mから行ってください。 と教えていただきましたがこの具体的な数値はどこから出てきたのでしょうか?またφ2.5でもφ16.0でも周速40mからスタートし、段々上げていけばいいということでしょうか? どうかよろしくお願いします。
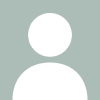
ロー付けという事は超硬ノンコートですね SUS316はJIS M30あたりでV50m/min前後 SUJ2は硬度HRC60くらいでしょうか、それですとJIS K01でV15m/min前後 送りは刃形状、切り込み、で違うので何とも言いようがないです。 Vは逃げ面摩耗幅、寿命時間に基準を設け調整すればいいと思います。 追伸:ロー付けバイトで迷うのならとりあえずスロアウエイバイト、(チップ材種はロー付けに合わせる)を使ってみれば条件の目安が見えてくると思います。
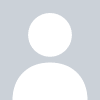
お礼
アドバイスありがとうございました。 例えばSUS316でφ16.0とφ2.5の場合両方ともVは50m/min前後でいいのでしょうか? よろしかったら教えて下さい。
お礼
回答ありがとうございます。 刃物の推奨範囲の真ん中だと大きく外しませんよね。 グランドローヤルは推奨条件が見つかりましたがハイカットの方は見つからなかったもので。 これからはハイカットに問い合わせたりしてみます。 度々のアドバイス、本当にありがとうございました。また何かあった時はよろしくお願いします。