- 締切済み
ポストユニットがスムーズに入らないためのリーマ位置の誤差
- リーマの位置がどれくらい違うと、ポストユニットがスムーズに入らないのかについて教えてください。
- ガイドポストに双葉のMGD25を使用しており、マシニングでリーマ加工を行い、上ダキ板と下ダキ板を組み付けましたが、動きが非常に硬いです。
- リーマの位置が上型と下型でどれくらい以上の誤差があると、スムーズに動かなくなると思われますか?また、心もみにはOSGのNC-LDS130度を使用していますが、この工具の場合、心もみをどのくらいのZ指令で行っていますか?
- みんなの回答 (4)
- 専門家の回答
みんなの回答
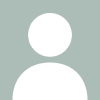
ガイドポストは自分では使った事がありませんので参考程度に。 実際には平面度が悪いと倒れの問題も考えられるとは思うが 普通に加工で大丈夫でしょう。 何よりスムーズに動くように組立調整をしてからポンチングでは 私は機械の組み上げが多いが 調整が終わってからピン穴を加工します。 上下通しなら重ねて加工とかも出来ませんか 別々に加工した物を組み合わせても 公差が 0 の部品なら何の問題はないが そんなの ムリ
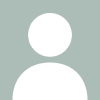
1ミクロンでも 干渉すれば動作不可能 スキマバメ の 範囲ならば 動作可能 各部品の公差範囲内で干渉が 無い状態 統計公差の問題は出さないでね
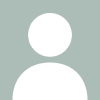
ピッチ長さにもよりますが、一般的には±0.02や±0.03、±0.05の公差を設計は使用します。 経験ですが、ガイドポストのピッチより、平行度や直角度の幾何公差的な問題も 大きいのではないでしょうか? ガイドポストの軸方向の動作力から、ガイドポストのピッチ方向に楔力が働くため、 ガイドポスト・ピッチ方向の多少弾性域も使用できるので、上述の公差にしております。 すべりのガイドよりは、転がり(ボール)のガイドの方が、摩擦係数や弾性域使用で有利なので、 転がり(ボール)ガイドを選択します。 それなりの機械で加工すれば、上述の公差での加工は可能と推測しますので、例えばガイド ポストの座面が傾いている(直角度が出ていない)のようなことが要因となっていると考えます。 昔、転がり(ボール)ガイドが非常に高価で、すべりガイドしか使用できない時代は、全てを インロー組み合わせで、加工精度に頼った組み合わせはしないで、設計(組付け)を工夫し、 ガイドポストの一方はインローで、もう片方は“倣わして”位置精度を決める構造として、 組立調整時に“倣わし”ピッチ精度を出し、その後ねじ増し締めしてノックピンを立てる ようにしておりました。<ノックピン立ては、再現性確保目的で、インローの代用です> 穴と軸又は凸凹の公差が、H7とh6のようになっていることです。 そして、ガイドポスト等のピッチは、加工精度によって左右される手法のことです。 穴と軸の寸法を、1~2mm差を設けガタにして、ガイドブッシュ機構のピッチに倣わせ、 増し締めしてノックピンを打つ等を昔はしておりました。
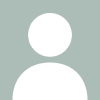
>どれくらい以上の誤差があるともう スムーズには動かないと思われますか? というより、ピッチズレが○○であったとの測定が先です。 3次元測定機を使える環境になくとも、加工したマシニングで測ることは出来ます。それが確かな測定なのかはさておき。 タッチセンサーなら4方向で中心出し。XでYの仮中心へ、更にYXとやるから6回当てることになります。 よりもテコ式ダイヤルゲージを回転させて芯を出し座標を記録していくのが正確。 http://www.mokkin.jp/tool/Lathe/mill.htm 加工物の芯出し(芯あわせ) 手で主軸を廻して、針の振れの変化が最小になるよう スライド・テーブルのX軸、Y軸を調整します。ダイアル・ケージが 反対側になってしまうときは手鏡に写して見ました(笑) 扉閉めないと動かない機械は面倒だけど仕方ない。 測定結果は待つとして・・・ >双葉のMGD25 ノック穴φ8H7 ピッチ58±0.015 上下ともにノックピン固定。1部品毎のピッチ 58 は回答(3)に近い精度が必要。なので±0.015は甘い。 但しポスト間のピッチ精度は寸法が大きい分だけ板が変形しやすくなって少しは緩和できる。 カタログの書き方は、H7穴は組付け後に共加工すべしと読めて矛盾している。 P.363 全部のねじをしっかりと締付け、最後にMGガイドとホルダに2本づづノックピンを打ちます 用途がプレス金型のダイセットなら、ダメダメ部品の典型例で、一般機械の設計屋が使うだけ。そして精密加工を知らないから[ ±0.02や±0.03、±0.05 ]より小さな公差は怖くて書けない。なのでノックピンは嵌らず、組立担当は使わずネジ締めだけにしておく。それでも使用条件が緩いから殆ど問題なく使える。設計には報告しないから知らぬが仏。。。。実際に起きることです。 ミスミでも双葉のカタログを見ても、これでダイセットを組んだものはありません。 ほぼ全てこの方式。 ガイドポスト:圧入またはネジ固定。その違いは精度穴の長さ。 ガイドブッシュ:ロックタイトまたはデブコンによる組立状態での接着。 しつこいかもしれないが、測ってください。 でないといつまでも原因不明のまま悩むことになるし、上記方法のどれが良いのか一々聞かないと判らない状態が続くし、それでは加工の腕も上がらない。 MGDは使いません! 金型の写真をサイトで公開するところは少ないが、見本市には僅か出てくることもある。出来るだけ努力して他を見てください。 MGDの利点はガイドポストとガイドブッシュが交換可能? それ以前に型ライフが尽きるでしょ。 なのに手に余る加工精度を要求する。規格ピッチ58±0.015では不充分。 ロックタイト/デブコン接着方式はガイドポストを垂直に立てることさえ注意を払えば、穴ピッチ精度は一般機械設計の[ 、、、、±0.05 ]より悪くても使える。 消耗交換は取外しが厄介だが一応可能。型合わせはやり直しだが、それほどの手間でもない。 両者の違いハッキリするでしょ。
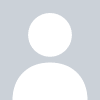
補足
ありがとうございます。 上だき板 下抱き板 の リーマ穴に x軸方向 Y軸方向にわけて タッチセンサーで 光るところまで あてたら 穴の中心にいなくても X方向 Y方向の ピッチは それぞれ 測定できると いう事ですね。 穴の中心に居なくても ピッチは 穴の中心にいた場合と 同じですよね? Φ6のタッチセンサーをつかっていますが、 Φ8のリーマ穴で あまり中心からずれた位置だと問題ありますか? ありがとうございます。 このMGDはあまり使われていないということなのでしょうか? 使っているとしても マシニングで 上だき板 下だき板 に最初から リーマ8をあけて いきなりノックを打って 組んだりはしていない ということなのでしょうか? このリーマ8 を OSGのリーディングドリル NC-LDS130度で 心もみ 深さー0.4 → φ6.9ドリル→φ7.7ドリル→φ8リーマで あけた時は かたくて しゅう動きしませんでしたが、 心もみの深さをー1→φ3のショートドリル(Z-10分) φ6.9ドリル→φ7.7ドリル→φ8リーマで あけた場合は ガイドは上下スムーズにストンと動きました。 何が改善して 原因はどこにあったのだと思われますか? 心もみは深い程 次の工具のピッチ精度がよく出てくれるのでしょうか? それともφ3のショートがきいたのだと思われますか? ありがとうございます。 質問した時点で すでに リーマをさらえ直していたので、 今となっては 測定できませんが、 次回同じ事が怒ったときは どれくらいの ピッチ誤差があるのか 測ってみます。 確かに±0.015 では不十分であれば 古いマシニングでは 難しい 時もあるかと思います。 ロックタイト/デブコン接着方式についても 勉強します。
補足
ありがとうございます。 >全てを >インロー組み合わせで インローとはどういう 意味なのでしょうか? 基本ですいませんが、お願いします。