- ベストアンサー
切削部品のダコン、キズの良否判定について
- 自動旋盤で切削加工された部品を回収する際、製品にダコンやキズが発生することがある。ダコンやキズの合否判定は表面粗さ以下で行われるが、検査基準は提示されていないため、どのように決めているのか疑問とする。
- 現在加工中の部品では先端部分の表面仕上げが中心平均粗さでRa1.6と図面指示されている。しかし、ほとんどの製品にダコンかキズが確認されるため、これがすべてNG品とされるのかについても疑問がある。
- 一般的には、検査基準は製品の用途や顧客の要求によって決められることが多い。ダコンやキズの程度や位置、影響度などが考慮され、必要な品質基準が設定される。ただし、具体的な基準が提示されていない場合は、製造者や顧客との相談が必要となる。
- みんなの回答 (3)
- 専門家の回答
質問者が選んだベストアンサー
- ベストアンサー
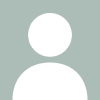
JIS B0633 製品の幾何特性仕様 (GPS)-表面性状:輪郭曲線方式-表面性状評価の方式及び手順 6.パラメータの評価 6.1 一般事項 表面性状パラメータは、表面欠陥の記述に用いることはできない。 そのためにスクラッチ、空孔などの表面欠陥は、表面性状の評価の対象としてはならない。 なので、ダコンやキズは表面粗さでは除外して測るもので、これとは別してダコンやキズの<検査基準>を取決めなければならず、発注先に状況報告、ご相談を 使用目的から考えるに ・空圧、油圧部品 凹は漏れなるからダメ。凸は摺合えば均せるから許容。イヤその微細屑も困るからダメ ・はめあい 凹は認める、凸はゲージGOなら可 ・電子部品 面粗さでは全体の表面積を注視するから局部的凸凹は可 様々です。その目的に叶った取り決め方も様々です。漏れの機能検査とかも有り得ます。 東京精密・規格解説 http://www.accretech.jp/pdf/measuring/sfexplain_1.pdf 粗さとうねりの違い。カットオフ値より大きいダコンはうねりと見なされ、粗さ数値では顕れない。 <JIS規格を手打コピーした蛇足> 5.測定値と許容限界値との比較ルール 5.1 対象面の測定領域 対象面上の表面性状には、均一とみなされる場合、又は場所によって異なっている場合がある。 この違いは、表面の視覚的な検査によって見分けることができる。表面性状が均一とみなされる 場合には、対象面全体にわたって求めたパラメータの値を、図面または製品技術情報に指示 された要求値と比較する。 表面粗さというのは、視覚的な検査・・・あいまいなものに頼る部分もある 自動盤屋さんの業界用語 Day何個落とすの? 落としてはダメ、しっかり受止めてやらないとNGなものが増えているでしょうね・・・
その他の回答 (2)
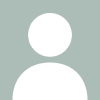
他の回答者さん(小生は、回答2さんのと略同じ)と同様です。 そして、良判定内であっても、“打痕や疵”は極力付かない手法で加工しましょう。 理由は、 ? 良判定内である確認が必要 ? 貴社工場内の状態を反映しているとみなされる 等々の?が、今の経済状態では致命傷になる恐れがあるため。
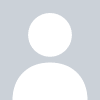
お礼
ご回答ありがとうございます。
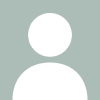
昔で言う ▽▽▽ Rz 6.3z =6.3μm の凸凹 =0.0063mm 今は書いてないかもしれないが 問い合わせれば まあ、図面の隅に有害な打痕 傷 なきことになって すべてNGになると思う
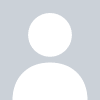
お礼
早速のご回答ありがとうございます。
お礼
なるほど、そうだったんですか。もう少しでとんでもない失敗をしでかすところでした。本当にありがとうございます。