- 締切済み
粉砕材の計量時間を安定化させる方法とは?
- アクリペットVHの粉砕材を使っているが、計量時間がばらついてしまう
- スクリュークリーニングや温度調整、背圧調整など試したが問題は解決しない
- スクリューのサイズや計量時間の設定を調整して安定化を図りたい
- みんなの回答 (2)
- 専門家の回答
みんなの回答
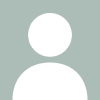
粉砕材は篩分けして、3分割してますか?過大品は再粉砕にリターン、微粉は樹脂ヤケの原因になるので廃棄。手抜きせずキメ細かい作業が大事です。 計量ばらつきのトラブルはスクリューの溝深さとペレット、粉砕品の大きさの関係でよく経験しました。 大型成形品全盛の昔は、メーカー出荷のペレットの大きさはφ3mm、L=3mmでしたが、成形品の小型化、小径スクリュー、時代の流れで、ペレットの大きさはφともにL=2.7mm→2.5mm→2.2mm→とミニペレットの要請が大きくなりつつあります。φ32mmスクリューの溝の深さ、適した大きさは? 例えば、3mm角の粉砕品では、対角の長さは4.2mm、5.2mmとなり、斜めに落下すると喰い込まずに踊ることになります。
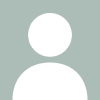
計量時間のバラつきの要因を把握する必要があります。『スクリューに食い 込んで』とありますが,粉砕材の噛み込みが原因ですか?それとも成形機の 送りの問題ですか?前者の場合は粉砕材の供給量に問題があるかもしれませ ん。供給速度を遅らせる(または供給量を制限する)と解決できる場合もあり ます。いずれにしろ,実験して改善策を方向付けするのが早道だと思います。 スクリューの動力モーターがトルクダウンしてませんか?モーターの特性を チェックする必要があるように思います。さもなければスクリュー軸のどこ かで焼き付き等を起こして回転抵抗が増えているかもしれません。 一度モーターの電流値を測って,定格以下かどうか確認してみてはどうでしょ う。過電流であればモーターまたはスクリュー軸の焼き付きを疑う必要があ ります。
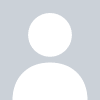
お礼
アドバイス有難う御座います。 供給量も調整しましたが噛み込んで 行かない状況です、粉砕材の大きさ も粉砕回数を増やして調整してみましたが ばらつきは変わらずでした。
お礼
ご指導有難う御座います。 やはりペレットの大きさは多いに 関係しますよね、低速粉砕機に3回 入れたら少し改善されましたがまだ 時折噛み込みが悪く空転してしまいます。 同じアクリペットもIRのグレードは 噛み込みが良いですが・・・。 噛み込みの良いスクリュや スリップ剤なども考えていますが どの様な物があるか分からず 悩んでいます。 取り合えず初回はPCへ 変更ししのぎますがVHの粉砕が 大量に出てくる状態です。 本当は再ペレにしたいのですが 再ペレ代が回収出来ないので、 粉砕のみでの使用を行いたいです。