- ベストアンサー
シリコンゴムの絶縁破壊とは?原因と手法について
- シリコンゴムの絶縁破壊とは、絶縁材料であるシリコンゴムが電圧によって破壊される現象です。
- 絶縁破壊電圧20KV/mm、絶縁距離は20mm程度ですが、50KVの電圧で絶縁破壊することがあります。
- 絶縁耐圧は厚さに比例しないため、400KVの耐圧は無いと思われますが、50KVに対しては十分なマージンがあるはずです。しかし、部分放電の進行やゴムの硬化不良、クラックなどが原因であり、原因究明のためには適切な手法が必要です。
- みんなの回答 (1)
- 専門家の回答
質問者が選んだベストアンサー
- ベストアンサー
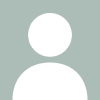
シリコーンゴム中にボイド(気泡)はありませんか? ボイドがあると、その部分の電界強度が高まりコロナ放電が発生することで オゾンが発生して、絶縁物であるシリコーンの劣化を加速します。 シリコーンゴムの注入はどのような方法をとっていらっしゃるのでしょうか。 お問い合わせのような高電圧の仕様では、真空加圧法が必要と思います。 こうすることで、ボイドの発生を抑制できます。 また、厚い(20mm)シリコーン一層ではなく、20mmを何層かに分割して、間に 導電層を挟み、電位分布を均等化することなどが一般的な構造と思います。 >20mmを何層かに分割する 現実には採用難しいのは了解致しました。 シリコーンを充填する空間にシャープエッジはありませんか? シリコーンの厚さができるだけ均等になるように、部品形状を修正できれば 電位分布が均等化して絶縁面では有利になるはずです。 この場合、シリコーンの厚さは20mmよりやや減る方向になると思いますが、 均等化の方を優先すべきと思います。 例えば、内径φ60のパイプ中に□20mmの導体があって、その空間を シリコーンゴムで充填する場合、□20mmの形状をその外接円に相当する φ28に変更するようなイメージです。シャープエッジが解消し、内外 部品間の距離が一定になって電位分布が均等化できます。 ボイドが絶縁破壊の原因と特定できた訳ではありませんが、注入前の2液 混練の際に真空脱泡しておくことが望ましいように思います。 プリント基板をシールドケースに入れ、その外側をシリコーンで充填する 構造がよさそうです。シールドケースの形状は、前の回答に記したとおり シャープエッジがなく、シリコーンの電圧負担が均等化できることが 必要です。シールドケースは、基板上の回路の安定電位に接続してください。
お礼
貴重なアドバイスをいただき、ありがとうございます。 確かに、絶縁破壊が起こっている箇所は基板端のプリントパターンで、パターンの角とか部品のリード端(丸めてはありますが)がエッジといえばエッジで、電界集中が起こる構造ではあります。シリコンゴムで覆っていますので大丈夫と判断しておりましたが、厳しい条件だということですね。 対策として、 (1)高圧部分のエッジ構造の回避(といっても具体的にどうするかは難しいですが) (2)脱泡の徹底 ということですね。 検討してみます。 どうもありがとうございました。 ありがとうございました
補足
ohkawa 様 ご回答ありがとうございました。 確かに、ボイドがあると、部分放電が起こり、徐々に浸食して貫通に至るかもしれませんね。 このシリコンゴムは硬化前は比較的流動性が高いので、普通に重力で流し込んだあと、真空脱泡しながら硬化させていますのでボイドは防止できていたと思っていたのですが、もしかしたら、たまたまボイドの発生が起こっているのかもしれませんね。 20mmを何層かに分割するのが一般的とのことですが、なるほどそういう方法は考えられますね(今回の場所はちょっと複雑な形状をしており、等間隔に導体層をはさむのはちょっと困難です)。 逆に20mmを一気に作ってしまうのは、やはり無理なものでしょうか?