- ベストアンサー
※ ChatGPTを利用し、要約された質問です(原文:ポリエチレンチューブの押出成型での偏平について)
ポリエチレンチューブの押出成型での偏平について
このQ&Aのポイント
- ポリエチレンのチューブの押出成型で外径の偏平が発生している現象について調査しています。
- 海外で試作成型したチューブの外径は楕円状になっており、社内での測定結果との差異が生じています。
- 影響要素として、チューブの梱包や輸送、成型パラメータなどが考えられます。真空サイジングでの寸法出しも行っています。
- みんなの回答 (1)
- 専門家の回答
質問者が選んだベストアンサー
- ベストアンサー
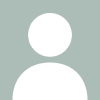
noname#230359
回答No.1
偏平については、業者測定結果を踏まえ、まず成型条件に起因するものではないと思います。 荷姿について触れられておりませんが、束に巻いているのであれば、巻き径の見直しが必要かと思います。 輸送はコンテナでの船便でしょうか? この場合、コンテナ内の温度は高温となり、常温の弾性係数を用いた束径の設計では偏平してしまうかもしれません。 また、直管での輸送でも、積み重ねて梱包しているのであれば、自重や積み重ね分の重量で偏平することも考えられます。
お礼
オルガニックさんアドバイスありがとうございます。 補足になりますが、 最初は荷姿は直径50~60cmのロール状でした。(Sample.A) Sample.Aの外径は偏平しておりました。 後日、業者に実際に測定したチューブを金属缶にいれて 送ってもらいました。(Sample.B) Sample.Bも弊社で測定した結果、偏平しておりました。 また、弊社より真円に近いチューブ(Sample.C)を 業者にダンボールで送って、業者に測定してもらいましたが、 径の変化はほとんどありませんでした。 輸送は航空便です。 質問本文と上述のSample.A-Cの結果から、 「成型条件」もしくは「輸送までの取り扱い」によるものではないかと 考えたのですが、成型条件については恥ずかしながら ほとんど無知で、質問させていただきました。 まずは巻き径の見直しについて検討してみます。 また他に考えられることがあれば、よろしくお願いします。