- ベストアンサー
ベアリングのハメアイ公差についての実際
- ベアリングの内輪に対する軸のハメアイは、ベアリングのカタログに推奨値が表示してあるようです。
- ベアリングのハメアイ公差は機械の条件によって異なることがあります。
- ベアリングのハメアイ公差は衝撃荷重や重荷重を受ける軸などの過酷な条件に適用されるべきです。
- みんなの回答 (10)
- 専門家の回答
質問者が選んだベストアンサー
- ベストアンサー
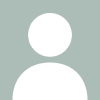
私の勤める会社では大半h7を使っています。 もっと精度が要求される部分ではきつくしたりするようにしています。 使用条件と経済性の折り合いをつけながら決めれば いいのかなと思っております。
その他の回答 (9)
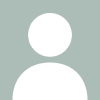
はめあい部のルーズ(ガタ)はそのまま軸の振れやガタツキ,振動になる可能性がある点を理解した上で使用するならば,h7でも良いと思います. ただし,はめあいをゆるくすればするほど急加減速や振動や衝撃荷重など,使用条件によっては,はめあい部にフレッチングコロージョン(2点間の微細なズレによる摩耗・その磨耗粉の錆状の酸化固着)や,クリープ(はめあい部のズレ,それによる鏡面摩耗)といった問題が発生する可能性が高くなります. みなさんが書かれている通り,h7でも良いが,はめあいがゆるいことによる問題が出るようであればタイトに変更するという形でよいのではないでしょうか. カタログや推奨値は安全を十分に見た値しか書けないものであり,あくまでも「推奨値」なのです. また,使用条件を添えて問合せをすればメーカーははめあいとすきまの検討をしてくれますよ. 小径・ミニアチュア玉軸受や工作機械主軸様軸受,その他,標準カタログに記載以外の推奨はめあい値を持っているものもありますし,すべての機械に適用すべきというものではないと思います.
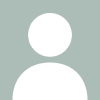
工作機のBT50相当のスピンドルのベアリング組み立てから ベルトテンション用ローラーのベアリング組までの経験があります ベアリングと軸、又はハウジング(穴)が一体になることが ベアリング組では理想だと思いますが、多くの回答者が記載しているように 使用目的を第一に組み立て、分解、加工などのし易さから、公差を決めていると思います 一般的に内輪が回転する場合は軸とベアリング内輪は圧入(程度は有ります)、穴とベアリング外輪は隙間(程度はあります)の関係に 外輪が回転する場合は穴とベアリング外輪が圧入(程度は有ります)、軸とベアリング内輪は隙間(程度はあります)の関係ににします 又、軸方向の固定はナットや、フランジで固定する場合や、Eリング等で抜け止め程度の場合もあります 簡単な部品(交換を丸ごと行えるもの)はh7でも良いと思います ただし、機械の主力部分に使われる場合は、組み立てやすさや、安価だからといってh6、h7の軸では心配がありますのでお奨めできません 圧入代とは少し違いますが、ベアリング組み立てで 当方での失敗例を記載します スピンドルの場合 アンギュラーベアリングの外輪を軸方向にハウジングで固定したのですが スピンドル回転の真円度が振れで0.003mm以下になりません あらゆる原因調査の結果、回転方向のボルト位置でベアリング外輪が内側にひずみがある事が分かりました ハウジングでの押さえがボルト4本と 押さえ代が過大(安くしようとして押さえ代を一定にする現合を行わず)だったことが分かり ボルト本数を増やし(ボルトサイズもおとしました)、軸方向の押さえ代を現合(押さえ代を0.02mmになるように関係部品を測定しハウジングを追加工)したところ 回転精度が0.001以下になりました ベルトテンションの場合 簡単に考え軸はh7、ローラーはH7で深溝ベアリングをEリング止めにしたのですが、 ローラーとベアリング間の磨耗とベアリング自身の磨耗で交換時期が 異常に早く来ました ベルトの走るスピードでベアリングの回転スピードに計算したところベアリングの許容値を超えていることとベアリングの外輪がローラーとの間ですべっていたことが分かり 許容回転数のベアリングを使用できるようにとベアリング外輪を圧入に なるように設計変更しました 直接質問の回答でなくてすみません
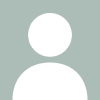
ベアリングの交換サイクルはどのくらいでしょうか?ベアリング交換時に軸やハウジングにフレコロ等の摩耗はありませんか? 交換サイクルが短くて、軸やハウジングに摩耗がなければ、分解組立てを考慮し、h7公差でやってみてもいいかもしれませんが、交換サイクルが長く、軸やハウジングに摩耗があるのであれば、h7にすると交換サイクルが短くなるかもしれません。 組立ては焼ばめや冷やしばめをすればいいので、分解しやすい工夫(油圧用の孔、ジャッキボルトなど)をするという方法もあるのではないでしょうか
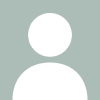
会社ではh7がほとんどです。 理由は組み立てや製作が容易になるからです。 良い製品というのは低コストでメンテナンス性に優れ、利用者が使いやすい物だと思います。 あまり交差のキツイ物だと分解修理が困難になり、その分お客様の支払い金額に上乗せしなくてはいけなく修理費が高くなり、また修理に時間も要することになるので代機があればいいですが、無ければライン停止期間が長くなるので現実的に苦しいと思います。 元々ベアリングは消耗品なので絶対に交換しない部分以外はh7でもいけますよ。 中には自社の製品で+0.025~0.03にしてベアリング自体も磨耗させてから使用する機械も… (高感度製品だとガタガタにしないとデータが出づらいそうです。)
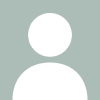
私の場合、軸受で軸を支持していて回れば良い程度の場合や、 製品のグレードや製品付加価値が低くてもよい場合は、一般的に言われている軸受設計基準によらない公差を採用してます。 この場合はh、gも使います。 そうでなければ荷重方向、荷重の大小、熱変位、振動等によって はめあいを決める通常の軸受設計基準ではめあいを決めてます。 GNMWさんの機械は重荷重+衝撃を伴うベアリングにとってはキツイ 負荷条件ですので、ここはメーカカタログ等にある軸受のはめあいの検討を されてみてはどうでしょう。 この計算結果や機械の使用状況、安全性等を考え現場要求のはめあいでも 必要な性能や品質を満足するようでしたら、公差を改めてみては。 検討の結果、現場要求のはめあいを採用できないようでしたら その検討結果を基に説明すれば現場も納得はすると思います。 (渋々かもしれませんが) まずは、設計検討(確認)でしょうか。
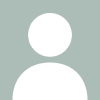
>つまり、h7を使ってはダメですか? これは設計者が判断し決めることであって 人に聞くことではないですよね・・・ ベアリングのハメアイ公差はh7でいい?とかkがいい?とか聞く前に、 何のために軸とベアリングの間のスキマを上級加工してハメアイと呼ばれる スキマ関係にするのか知ることが先の気がします。
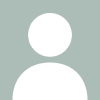
どもども。 私の所属する会社でも、よほど精度が必要とか、高負荷使用でない限りはh7です。割合としては90%以上がh7です。 理由は皆さんと同じく、"加工が安くできる""組立が楽"と言うところです。 主として社内設備を設計しているのですが、圧入が必要な設計にすると、現場のメンテナンスの人から「もっと簡単にならないの?」とクレームが来たりします(^_^;) ベアリングメーカーとしては、軸受に最もいい条件でしか推奨できないでしょうから、使う側が部分部分で、折り合いをつけていくのが大事だと思いますよ。 私も同じ疑問を持ってたので、ちょっと安心しました。
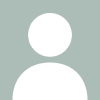
h7を使って実際に問題がなければ、h7でいいです。低速回転であってもフレコロが発生するような場合はしめしろを大きくするケースもあります。当然ベアリングヒーターや油圧プレスで組み付けます。 蛇足ですが、内輪、外輪ともにきつい締まりばめにする場合はベアリングの内部すきまをC3やC4を用います。
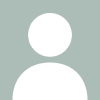
私事ですが、h7交差を使用しています。 業種は板金プレスの自動化設備を主に設計している者です。 組立ても行ないますが、ベアリングの加熱機も使用しておりません h7指定でも、指で押し込める程度の仕上がり穴へ組み付ける事が 大多数ですが、特に問題を感じた事はありませんです。 中には本当にシビアな精度を要求されるような部分が有るのかも しれませんが・・・ま・・・部位に適した仕上げが必要なのでしょうね と言う事で、私の答えは余程の物までh7で問題無しです。