- 締切済み
※ ChatGPTを利用し、要約された質問です(原文:成型品の製作方法について)
成型品の製作方法について
このQ&Aのポイント
- 成型品の製作方法と素材選定について相談です。
- 面状発熱体を用いたハムスター用暖房器具(130×150mm)の製造開発を計画していますが、成型品の製造方法や適切な素材について詳しく教えてください。
- 成型品関連の業界でお詳しい方、初期費用や製造コストが低い成型方法や素材についてアドバイスをいただきたいです。
- みんなの回答 (1)
- 専門家の回答
みんなの回答
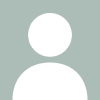
noname#230359
回答No.1
こんにちは。 私どもはゴムの金型屋ですので、成型関連はあまり詳しくはありませんが、ご紹介は可能です。 素材に詳しい方も居り、中国・上海に生産拠点を持つ会社なので、量産段階でのコストダウンも可能かと思います。 私どもへご連絡いただければ、仲介します。 以下のアドレスまでメールを下さい。 yamazaki_sk@nifty.com ご連絡お持ちします。