- 締切済み
成形品の重量管理におけるその許容範囲は?
新年おめでとうございます。 初めて質問を投稿させて頂きます。ご指導宜しくお願い致します。 【質問】 成形品の品質管理には、成形条件管理・外観管理・寸法精度管理・重量管理・他 要求特性に合わせた方法があると思いますが、ここでは重量管理についてご教授 をお願いします。 下記条件において成形ロット間の重量バラツキは一般的にどのくらいまで管理可 能なものでしょうか? ...1500±(?)g <条件> 材料:PC-GF30 成形機:650ton 成形品重量:1500g 要求特性:寸法精度(フレーム)
- みんなの回答 (2)
- 専門家の回答
みんなの回答
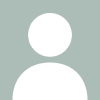
以前の実験した経験から投稿します。 重量は、連続生産中,ロット,機種変更などにおいてかなりばらつきます。 連続生産でも、10ショットも取れば0.3%くらいは十分ばらつきます。 また、測定時の環境や成形後の時間経過などばらつかせる要因も様々です。 (重量は、寸法よりも数値変化が大きいようです。) 長期間のデータを十分蓄積して、参考管理としていくことには支障がありませんが、数回のトライから管理値にしようとすることは困難と思われます。
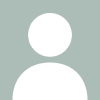
射出成形は、射出⇒保圧⇒冷却⇒型開き⇒取りだし という工程で行われています。この時の保圧の工程で時間が短すぎると、品質のバラツキが大きくなります。この品質とは何でしょうか?寸法精度や強度・表面粗度など色々考えられますが、重量は品質でしょうか?何グラムのものを作ってくれと言うい依頼は、聞いたことがありません。したがって、重量は管理するものではないということです。 それでは、何に使えるのでしょうか。保圧工程は何のためにあるかというと、充填された樹脂が逆流しないように圧力をかけている時間です。製品のゲート部分が固まれば成形機の圧力を抜いても、樹脂は逆流しません。しかし、ゲートが固まる前に圧力を抜いてしまうと、樹脂が逆流します。それによってヒケが大きくなったり、ボイドができたり、変形したりして、寸法や強度・外観などに不良が発生します。すなわち、重量でその他の不良を知ることができるわけです。 保圧時間を変化させて成形し、製品を取ってみて下さい。保圧時間を横軸に、成形品重量を縦軸にしてグラフを作成します。ある保圧時間以上になると成形品の重量が変化しないことが分かります。 それでもある程度は重量がばらつきますが、このバラツキが問題になるようならば、その製品はその樹脂であるいは、その成形機で、その条件では使用できないと言うことになります。 私は、PCについてはどの程度ばらつくか知りませんが、重量を管理する目的を考えた方が良いと思います。
お礼
大変貴重なご意見ありがとうございました。とても参考になりました。