- ベストアンサー
長穴加工で長手側寸法がマイナスになる理由とは?
- 長穴加工を行う際、長手側の寸法が常にマイナスとなってしまう問題が発生しています。
- 仕上げ削りを行う前に粗削りをし、0.1mmの取しろを残していますが、それにも関わらず長手側の寸法が正確になりません。
- 幅側も若干マイナスになることがありますが、修正すれば問題ありません。しかし、長手側の問題はR部の送りを調整しても解決しないようです。原因について考えているので、アドバイスをいただけると助かります。
- みんなの回答 (8)
- 専門家の回答
質問者が選んだベストアンサー
- ベストアンサー
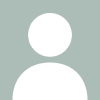
その他の回答 (7)
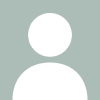
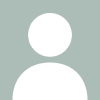
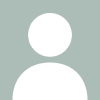
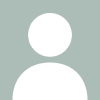
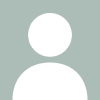
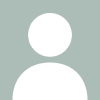
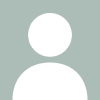
関連するQ&A
- 穴加工の精度がでません。
マシニングセンター初心者です。 最近 マシニングセンター(日立精機のVM40)にて 加工をがんばっています 今までフライスやマシニング経験が、まったくありません。 寸法が200×150 T=10 のプレス加工品(SPCC) のほぼ中心の穴Φ61.5をマシニング加工で Φ62±0.015に仕上げたいのですが ?真円度が全くでない(楕円になります) なぜか アプローチ部分に刃物の後がくっきり残ります。 ?旋盤にて簡単なゲージを作成して ゲージで確認すると エンドミルが逃げているのか 表(品物上方向)から入れるのと 裏から入れるのとではまったく感触が違いますし 横に力をかけると、刃物がにげているのか テーパーになっているみたいです 横から穴を見ると 極端な感じで \ / になってます ?単価が安いので 何枚かをまとめてクランプして仕上げたいのですが 現状では一枚ずつでも加工できません。 現在Φ16のエンドミル(ハイス)で加工しましたが もしエンドミルで 仕上げるなら普通では 考えられないような細さなのでしょうか? 粗加工(仕上げ代0.1)をして仕上げや 回転、送りなども色々試したり 刃物を短く取り付けたりと 素人で考えられることは出来るだけしましたが 状況はかわることはありませんでした。 ネットで調べたら ボーリングヘッドというものがあったのですが マシニングの基本では こういった加工では ボーリングヘッドを 使うのが基本なのでしょうか? エンドミルで十分加工できるし粗加工もいらない一発仕上げレベルの 範囲なのでしょうか? また、ボーリングヘッドを使用するなら エンドミルにて粗加工するべきなのでしょうか? 片側の取りしろが約0.25であれば一回で大丈夫なのでしょうか? ほんとに ど素人ですが 少しのことでもよろしいのでアドバイスいただけたら幸いです よろしくお願いします
- ベストアンサー
- マシニングセンター
- 長穴加工のエンドミル倒れについて
現在、タッピングセンター(ブラザーtc-r2a)でアルミ(A5052)の加工をしており厚み8ミリの材料に長穴(小判型貫通)の加工をしているのですが、交差が4.01~4.03までで表の加工面は4.02に寸法を出しても機械から外し裏面を確認すると4.04位になり倒れてしまいます。 加工手順としては下穴2.5で開けて3.5のエンドミルで突いてから2ミリづつ下げ上下させその後、ギリギリ迄工具を下げ径補正で粗びき、仕上げと2回、回しているのですが倒れてしまいます。工具の本数の都合上2.5のドリルで下穴を開けるしか無いのですが、やはり、3.9で開け、3.9のエンドミルで加工した方が良いのでしょうか?3.5のエンドミルも別部分の加工で使用しており3.5じゃないとだめなんです。使用工具は超硬四枚刃 回転、送りは色々試してますが何分、経験が浅いので熟練工の方ご指導お願いします。 説明文下手くそですがご容赦ください。
- ベストアンサー
- マシニングセンター
- H7のとまり穴の加工について
プラ型の加工を行っております。先日、φ8H7深さ10という加工があり、7.7キリ、8エンドミル突き、8エンドミル仕上げ、という手順で行おうと試みましたが、8エンドミル突き終了後、すでに8.3ぐらいに寸法が広がってしまいました。手順から間違っているような気がするのですが、アドバイスありましたらお願いします。(8エンドミルはその時欠けてしまいました)
- 締切済み
- マシニングセンター
- エンドミル加工でのチッピングについて
金属加工についての質問です。 マシニングで、材料はADC12、水溶性の切削油を使用しております。 粗削りをφ10超硬DLCコートエンドミルで円がφ18高さ8mmのボス加工をしています。 仕上に別の刃物、φ10超硬DLCコートのエンドミル(強ねじれ)で円がφ17.95の円加工(CW)で高さ8mmで加工しているのですが、仕上の刃物が100ヶ~1000ヶほどでチッピングしてしまうときがあります。良いときで9000ヶほど加工できるときがあります。 切削条件は回転数1900送り220です。 原因として考えられることがありましたら教えて頂きたいと思っております。
- 締切済み
- 切削
- フライス加工(専門的で長文です)
DTYレベルではないですが、専門家の方が居る様なので気長に回答を待ちたいと思います。 質問は6面加工の手順です 出来上がり寸法を50×80×100mmとした場合 取代は片側2.5mmついているとします50の面だと55です 以下質問になりますが、途中までの手順が間違っていたら、指摘してください。 1 まずバイスにセットは50×100の面をバイスの両面に当てるのが良いのでしょうか? その際のくわえ代は約半分の25mmくらいが良いのでしょうか? 2 上面を適当に削り、50×100の面の上から20~25mmをエンドミルで2面、平行面を作る? 3 反転して最初に上面を削った面を下面にして平行面をバイスに当て上面をフライス加工する? この時厚さ50で仕上げてよいのでしょうか? それとも、もう一度反転して仕上げるのでしょうか? 4 (そもそも、一面づつ荒削りしては仕上げるのか、それとも全面を0.3くらい残して荒削りしてから最後に全部の面を仕上げるのか?) 5 一番広い面をバイスに挟み50×100の面をフライスで上下面仕上げる? 6 加工物を縦にしてスコヤで垂直を出し50×80の面をフライス加工 7 一番分かりにくいのは、対面の2面あるうちの最初に削った面は、最初の時点で荒削り→仕上げして良いのか、それとも、仕上げ代を残しておいて、反対側を削った後もう一度、仕上げるのかです。 以上うろ覚えの作業です。正しい加工の仕方を教えてください。 文章で説明って難しいと思いますが、よろしくお願いします。
- ベストアンサー
- DIY(日曜大工)
- 図面寸法の入れ方と加工順序について
寸法の入れ方と、フライスの加工順序について質問します。 理想通り(公差0)の場合には、全く同じ意味になる寸法でも、寸法をどこに記載するかによって、フライスをかける順番が変わるということを聞いたことがあります。それは本当でしょうか? また、変わるとした場合には、どのように変わるのでしょうか?とりあえず、2つの場合について、以下に私の予想を書いてみました。正しいでしょうか?よろしくお願いします。 また、寸法の入れ方と加工順序の関係について多数例示してある本とかあれば教えてください。 【加工順序(私の予想)】 以下、大文字の寸法は、設計値および設定値、小文字の寸法は、実測値を表すものとし、 寸法の名称は、添付図左側に記載の通りとします。 (イ)寸法として、A0と中心線とC0を指定した場合。 1. エンドミルを、稜線(1)に、右から当接させる。その後カウンタを0にリセットする。 2. エンドミルを稜線(5)に左から当接させる。この時のカウンタの読み値を「値1」とする。 3. カウンタの値が、(値1)/2 になるところまでエンドミルを動かし、再びカウンタを0にリセットする。 4. l2=((C0+φ)/2)+一定値, r2=((C0+φ)/2)+一定値となるまで、左右から切削する。 5. エンドミルを、稜線(2)に当接さたときのカウンタの読み値を、値2とする。 -公差の許容値<|カウンタの読み値(値2)|-(C0/2)<公差の許容値 となるまで切削を続ける。 6. エンドミルを、稜線(4)に当接さたときのカウンタの読み値を、値3とする。 -公差の許容値<|カウンタの読み値(値3)|-(C0/2)<公差の許容値 となるまで切削を続ける。 (但し5と6は並行して実施する。) (ロ)寸法として、A0と、A3とC0を指定した場合。 1. l4=-(A3+(φ/2)+一定値),R0=A1+(φ/2)+一定値となるまで左右から切削する。 2. エンドミルを稜線(2)に当接させたところから、 -公差の許容値<(A3-a3)<公差の許容値 となるまで切削を続ける。 3. エンドミルを稜線(4)に当接させたところから、 -公差の許容値<(a1-A1)<公差の許容値 (但し、2と3は並行して実施する)
- ベストアンサー
- DIY(日曜大工)
- 旋盤/振れについて
普通旋盤を使ってリング状の部品を加工したいのですが長手の寸法にどうしても振れが出てしまいます。 部品の仕上げ寸法はφ55×25 φ27穴あき、材質はS45Cでチャックはスクロールチャックを使っています。 長手の25の寸法を±0.03くらいに入れたいのですが現状では毎回0.1くらい振れてしまいます。チャックの面に当てる治具を作る方法やダイヤルゲージ等で修正する方法も考えたのですが中々うまくいきません。やはりスクロールチャックでは限界があるのでしょうか。 長さが25ということでどうしてもつかみ代が少なくなってしまうことも原因だと思うのですが、なにかいい修正方法はないでしょうか。 よろしくお願いします。
- ベストアンサー
- DIY(日曜大工)
- どうも外径の寸法が決まらない。
NC立旋盤のオペレーターです。立旋盤歴3年、まだまだ解らないことだらけです。小さくても外径がФ1500を越えるワークばかりですが、外径の寸法が決まらずに悩んでます。 ?黒皮をまずXもZも片側1?残しで形状を作る。つまりXは直径で2?残し。 ?仕上げチップで片側0.3?残しで削る。 ?寸法を測り、計測が出来る幅だけ片側0.15?テストカット。 ?仕上げ寸法でけずる。 以上が仕上げの手順です。仕上げは全てオフセットの摩耗調整で数字を調整しています。 内径とZ方向(長手方向)は以上の手順で公差が0,05でも±0.01でも狙い通りの寸法に仕上がります。 しかし外径だけが?の時に毎回狙った寸法より0,04?~0,05?ほど大きく削れます。最後は毎回ハンドル操作で公差に入れてます。 測定ミスでないとすれば原因として何が考えられるでしょう?内径とZ方向はしっかり決まるとなるとNCの不具合ではないですよね?
- 締切済み
- 旋盤
- 切削目の粗さについて
5面加工機で切削した箇所の切削目の少なくなる加工方法を教えてください。 図面指示にあるRa6.3(▽▽)は精度的に出来ています。 しかし、切削目が均一に出ておらず見た目が良くないと顧客に言われ困っています。 段差がある部分の加工のためエンドミルで加工しており又材質はSS41のためか所々「むしり取ったような」箇所があり、フルバックの刃で切削したような面の均一さは出ません。また構造上ビビリが発生しやすくうまく出来ないと加工先から言われております。 加工方法、切削条件を調整する範囲でクリヤーできるものなのでしょうか? 現在の切削条件は(エンドミル) 1.仕上げ加工時:主軸回転数(500RPM)送り速度(200ミリ)削り代0.05 (2回かけている) 2.荒仕上げ :主軸回転数(500RPM)送り速度(300ミリ)削り代0.5から1 3.切削する面の長さ:約2600mm3000? となっています。なお荒削り時の目の粗さが仕上げ時に残っているのでは? との疑問もあります。 何か良い方法があればご指導ください。
- 締切済み
- その他(機械加工)
- 穴径精度が出ません。
材質はSS400 寸法は9T×40×65Lの材料にΦ25H7の寸法を出したいのですが穴径が楕円になってしまい出ません。 現状の加工方法です。 下穴:Φ24.5ドリル(ナチテーパーシャンク) 仕上げ:Φ18超硬エンドミル(OSG:WXL-EMS) 回転:1,600 送り:200 円弧で加工していますが寸法が0.02~0.03シリンダーゲージで計ると差があります。 解決方法等あればご指導お願い致します。
- 締切済み
- マシニングセンター
お礼
返信ありがとうございました。 粗加工後R部をエンドミルで上から突き加工ですか。 これは考えたことがありませんでした。 一度試して見たいと思います。 アドバイスありがとうございました。