- ベストアンサー
17Sアルミにφ40の穴をあける際の面相は何が原因なのか?
- 17Sアルミにφ40の穴をあけたいが、目標としている面相が出せず困っている。
- 使用工具はノーズRが0.4の人ダイヤのついたチップを使用し、回転は12000、送りは300、切削は水溶性のものを使用している。
- 面取りは十分にしてあるが、切粉や主軸の振動が原因かどうかわからず、ボーリングで面相が出るのかについても疑問がある。
- みんなの回答 (5)
- 専門家の回答
質問者が選んだベストアンサー
- ベストアンサー
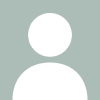
その他の回答 (4)
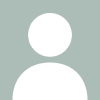
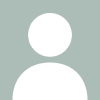
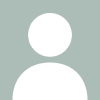
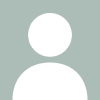
関連するQ&A
- ボーリング 仕上げの切削条件
ボーリング切削において、仕上げをする場合ですが、 カタログなどを見ると、表面が反射しているような、きれいな仕上げ面に 加工されています。 私が、行うとびびりではなく、ざらついているような感じに なってしまいます。 ボーリング自体、最近始めたので、切削に関することを アドバイスしていただいきたです。 加工条件は、材料S45Cの、 径12の深さ6mmの貫通穴です。 メーカーは、ビックプラスの仕上げ用のボーリングです。 突き出しは、30mmくらいです。 チップは、超硬のT1200Aです。 回転は、S2500の送りが、F120です。 R0.2のチップを使用する場合、 S2500 × 0.06とカタログに書いてあったので、 多少落として、F120にしてみました。 ボーリング加工は、回転・送りを出来るだけ、 落としたり、上げたりしたほうがいいとか、 あるのでしょうか? 長くなりましたが、なかなか、うまくいかなくて 悩んでます。 よろしくお願いします。
- 締切済み
- 切削
- ボーリングの断続切削について
現在、ボーリングの断続切削で悩んでいます。 加工内容はΦ160mm程のH7公差の穴が二つ並んでおり、穴同士が三分の一程重なっている為(「 ф 」の様な形です)、ボーリングを通すと断続切削になってしまう形です 。深さが100mm近くありエンドミルでは少し厳しい気がします。 材質はSCS14です。 現在、色々試してみましたが、大昭和精機の仕上げ、荒用のボーリングを使い、仕上げ代0.05mm程度までもっていき、仕上げボーリングをいれましたが、一穴とチップがもちません。 仕上げの切削条件はS200 F10でファインボーリングサイクルです。 深さ2/3程までは綺麗に切削されますが、それ以降から引目が急激に悪くなり、寸法も急激に変わります。摩耗ではなくやはり断続によるチップの破損が大きく影響しているようです。 現在チップが持ち合わせのノーズR0.2を使用したので本日R0.4を注文したので明日こちらを試す予定ですが、それも上手くいくかわかりません。 チップの選定や切削条件等、ボーリングの断続切削に知識のあるかたおりましたら、情報頂けると助かります。 困っているのでよろしくお願いいたします。
- 締切済み
- 切削
- 平成17年 技能検定ペーパー試験 1級 問題6に…
平成17年 技能検定ペーパー試験 1級 問題6について ボーリング加工する場合の切削部位と中ぐり工具のチップとの関係で、この加工を主軸モータの定格15kWのマシニングで行う場合の最大の送り速度を回転当りの送り量(mm/rev)で解答。解答は、小数点以下第3位を四捨五入。 条件1、主軸の出力効率は90% 2、主軸回転数は600(min-1) 3、π=3.14 √2=1.41とする。 4、切削動力計算式 kW=V×a×s×K / 6120×9.8 kW:切削動力kW V:切削速度m/min a:切削幅mm s:送り量mm/rev K:比切削抵抗係数2940N/mm2 5、切削速度は2穴の切削速度の平均値で計算。 6、図の▼印はチップを意味する 7、図の( )寸法は素材形状である 図は(φ78)の中心に(φ40)の開いた素材に、中心にφ62深30とφ44深32の穴(ザグリ?をボーリングで中ぐりしてある図が書いてあります。 受験経験者の方、解答できる方ぜひ解き方を教えていただきたいのでよろしくお願いします。
- 締切済み
- マシニングセンター
- リーマ加工の面粗さ・寸法精度
被削材S45で、Φ13穴公差±0.005面粗さRa0.8(Rz3.2) 。加工深さは20mm程度ですが、段下に穴がある為 刃物の最低突出量85mm必要です。 現状、BIGのボーリングを使用し(超硬丸バイト) チップはノーズR0.1(ビリ対策用)を使用しました、 加工条件V=50 f0.05で加工した結果Ra13程度になっ てしまったので、ボーリング後にリーマΦ12.99(EIKOUSHA ハンドリーマ(ハイス)) を追加し、取代片0.1mmクーラントは油性で加工を行った結果Φ13.012 Ra1.5と公差・面粗さ共に図面スペックを満たす事が出来ませんでした。 何か改善策がありましたら、ご指導願います。 リーマ加工条件はV=6 f=0.05です。 Φ13.000公差±0.005までの加工手順 スローアウェイドリルΦ12.5(先端超硬タイプ)→ボーリングでΦ12.8→リーマΦ12.99(刃物公差+0.007~+0.015) という流れです。ボーリングを入れているのは穴を真っ直ぐにする為です。 ボーリング時の加工条件: 回転数 S=1220min-1 テーブル送り F=60mm/min 1刃の送り f=0.05mm/rev 切削速度 V=50m/min 理論値 Rz=3.13μ → 実測値Ra13.0
- 締切済み
- マシニングセンター
- ダイヤチップについて。
ダイヤチップ(燒結)を用いて、アルミの仕上げ加工をしています。 この時に出る切粉を細かく分断したいのですが、チップブレーカ付のダイヤチップなどは出ているのでしょうか?また、切粉を分断する良い知恵があったら教えてください。 加工条件は周速500m、切り込みが0.2、送りが0.15です。
- 締切済み
- 切削
- BTA加工の切削条件についておしえてください
会社でBTA加工を行っています。 一般的な組み立て式のボーリング ヘッド(トップ刃、中間刃、肩刃 +ガイドパッド2枚)を使用して φ50×1800?の深孔開けを行いたいのですが、適切な切削条件がわかりません。材質はSNCM616です。 回転500、送り75でやってみましたが、面相度が悪くむしれ、ビビり が多く発生してしまいます。 一般的なBTAボーリング加工では周速、送りはどの程度なのでしょうか? 切削工具の会社に問い合わせてみましたが、明確な回答は一切もらえません でした。 どなたかおしえていただけないでしょうか?
- 締切済み
- 切削
- チップの選定
S45CFSの加工についてですが。 NC旋盤主軸移動型 (2タレット)使用、前挽きでΦ22からΦ14に加工していますが50個~100個ほど加工するといきなりマイナス0.1位してしまいます。 加工方法:切削油は油性で加工長さ30mm、バランスカット荒挽きΦ18、仕上げΦ14、荒挽きのバイトを仕上げより1mm前にしてます、チップ形状は55°先端R0.2でバイト16角、(回転数1800RPM、送りF0.04)です。 いろいろとチップを試しました。 NTK TAS、ZM3、CP7。 京セラ VP7020。 切粉はどれも細かくなって良いのですが・・・ 何か良いチップの材種を教えて頂けないでしょうか? 宜しくお願いします。
- ベストアンサー
- 切削
- 銅板(t=2.5mm)正面フライスによる打ち抜き…
銅板(t=2.5mm)正面フライスによる打ち抜き穴まわりの引っ掻き傷の対策 半年ほど前からマシニングで正面フライスでの切削を担当しています。 銅板の仕上げ加工で、打ち抜き穴近辺に引っ掻き傷が残ります。 対策を教えて下さい。 先日厚さ2.5mmほどの銅板(タフピッチ)の平面切削を任されました。 条件:S4000F450ダイヤモンドチップ使用、切り込み0.2mm切削油なし 加工自体は平面度0.1mmで単純なのですが、取り付け穴と思われる 打ち抜き穴?が銅板の4隅にあいており、カッターが逃げる片方の穴の 外側だけに、引っ掻き傷が残ります。 原因として考えているのは下記です。 ?穴につまった切粉を噛んでいる ?穴があいているため切削が断続となり穴を抜け、再切削に入る時に 抵抗が大きいため、切削条件が崩れている ?平面部の切削段階で、少し押されていたチップが、穴により 解放され弾かれたようになり、再度穴の外側の切削に入る時にチップが ぶち当たるようになり、傷がはいる。 どなたか経験のある方対策と原因を教えていただけませんでしょうか。 引っ掻き傷ができるのが、カッターが逃げる側の穴だけなのがきになります。 4隅に打ち抜き穴があり、全部で傷が生じるのではなく、片側の2ヶ所だけです。カッターが銅板に入る側では、面取りなどされてなくても、傷は生じません。 そこで、原因として下記を追加します。 ?切削動力の変動のため ・切削開始部では傷はできない→動力に余裕があるため負荷に対して対応しやすい。 ・切削終了部で傷ができる→切削してきたので、負荷がかかっており、穴部で負荷が解放された途端、また切削しなければならないので、負荷への対応がスムーズにできていない。 とすると、穴部近傍のみ、送りを下げる対応がいいのでしょうか。 素人考えでおこがましいとは思いますが、ご意見をお願い致します。
- 締切済み
- マシニングセンター
- 切削水、切削油の回収
当社はNC旋盤で旋削加工をしております。 そこで、切粉をチップコンベアから切粉箱で受けておりますが、切粉についた切削水が切粉箱にたまり、切粉箱の底に切削水回収用の穴を空けてあり一応ポリ箱で受けてはいるのですが、床にこぼれてしまい汚くなります。 一応切削水をチップにかけるポンプから回収用のチューブがあり使ってはいますが、時がたつとほとんど使い物にならないようになってしまいます。 また、切粉箱にたまった切粉を切粉捨て場に回転リフトでもっていき、切粉を回収する大きなコンテナに入れるのですが、ここにも切削水の持ち出しが多くコンテナに溜まり、回収業者がトラックに入れる際、たくさん切削水をこぼしていきます。 皆さんの会社ではどのように回収していますか? このようにするとこぼれないし綺麗に出来るよというアドバイスがあればおしえてください!! よろしくお願いいたします。
- 締切済み
- 旋盤
- 内径ボーリングバイト(オール超硬)のオイルホール
内径ボーリングバイトにオイルホール付きは市場にあるのですか?ホルダーに付いているのは見たことが有るのですが、オイルホールがあれば切削性が上がるか 又、その穴を使用して切り粉のエアーブローに使用できるか?ご意見求めます。
- 締切済み
- 旋盤
- インクを補充後、残量情報をリセットしても再度更新を促す画面が出る。
- 電源を切り、再起動し、30秒位は正常だがその後再度更新を促す画面となる。
- この現象は最新のファームウェア10.61.LT22LAに更新してから発生と思われる。ファームの破損を可能性が考えられたので強制更新を試みたが改善せず。
お礼
ワーパー形状というものはどういうものでしょうか?もしよろしければ簡単なたとえでもいいのでぜひ教えていただけないでしょうか?(お時間があるときでよろしいですので。) バニシングのほうはネットで検索してみましたが、結構いい感じの面相が出そうですね。 径などもきちんと出せればボーリングのあとになんか使えそうな気がします。 貴重なご意見ありがとうございました。